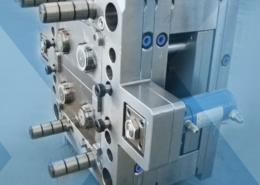
What should we pay attention to plastic crate mould? - plastic crate mould
Author:gly Date: 2024-10-15
Even if you’ve already done a short run, you’ll need to invest in a more complex set of molds for a long run manufacturing process. In a long run, each mold typically contains multiple cavities, meaning they are more expensive to produce than the molds used in limited short runs.You can also expect high material costs at the start of long run production, as large quantities of material are needed to produce the high part counts characteristic of this production process. ROI in a long run comes from volume. Long runs work quickly to churn out large numbers of parts; the more parts that are produced, the lower the cost per part as the price of the mold and material is distributed among them. The faster parts are produced, the more quickly you get your investment back and the run begins to pay dividends. Whether you need a short or a long run for your project, Thogus is here to help. Learn more about our injection molding capabilities.
Plastic injection molding is a highly versatile manufacturing process; it can produce large quantities of parts relatively inexpensively in a short period of time, or it can allow for meticulous product development, smaller batches of parts, and more extensive prototyping. The kind of run you need will depend on your end goals for your part, as well as its complexity and your project timeline. The following considerations and expectations will help you decide between short run production and long run production for your project.
Experience the Thogus Difference Connect with us today to discuss your project and to learn more about our capabilities.
Plastic News magazine reviewed over 500 companies with injection molding capabilities and Inteva Products ranked in the top 20, earning Inteva a Top 100 Injection Molders Honor. Companies are ranked by sales of injection molded products in the most recent full fiscal year. Plastic News is a noted authority and is the largest circulation magazine among all plastic publications.
Plastic injection molding is famous for long run production, where large quantities of parts (often in the millions) are produced quickly. To accommodate this capacity, long run production uses bigger molds than short run production, and tends to have higher startup costs, though the cost per part is low when compared to other manufacturing methods.
Short run production follows essentially the same manufacturing process as any other injection molding run. That means that appropriate materials need to be selected and tooling needs to be created specifically for each short run project. Plastic injection molders will have some things that you need for your project, like the injection mechanism, on hand. However, the mold itself must be custom created for each project. Because the mold has to be manufactured regardless of the size of the run, you can expect higher cost per part in short run production. However, short runs have the advantage of extremely fast time to market. Prototypes can be produced and evaluated quickly and working models can be in customers’ hands within a very short timeframe.Short run production can also help prepare for long run production, if that’s where your project is headed. Short run tools can be easily and inexpensively modified to become long run tools, and the revenue from an initial short run can help finance production costs in a long run.
Short run production, also sometimes called small batch injection molding, produces a limited number of parts, either for highly specialized projects or for preliminary manufacturing of eventually larger runs. For this reason, short run production is often used in initial product development to create a set of pieces to determine whether they work together as intended. Short run production can also be used to create replacement parts after a product is on the market. During the initial product release, a long run may be necessary, but after that point a smaller number of parts may need to be continually produced for service and replacement.
Founded in 1950, Thogus is an established, family-owned custom plastic injection molder and contract manufacturer headquartered in Avon Lake, Ohio.
GETTING A QUOTE WITH LK-MOULD IS FREE AND SIMPLE.
FIND MORE OF OUR SERVICES:
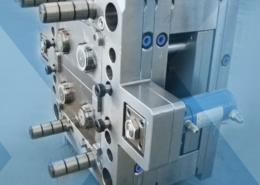
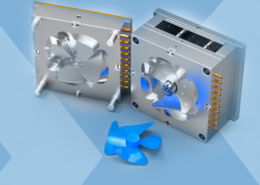
Plastic Molding
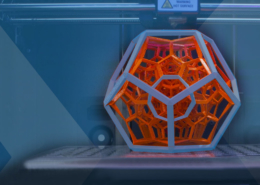
Rapid Prototyping
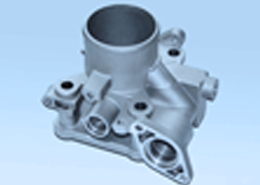
Pressure Die Casting
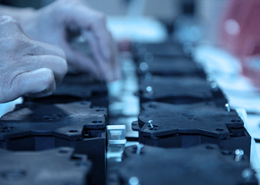
Parts Assembly
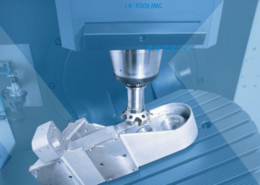