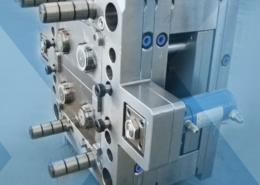
Why Gas-Assisted Injection Molding Simulation? - gas assist injection molding
Author:gly Date: 2024-10-15
The holes, slots, and depressions in plastic parts are crucial features for proper assembly, ventilation, and even providing aesthetic value in some products. These features are formed by the core, the protruding part, of the mold. During the injection molding process, the core with excessive height or length bears higher impact force from the molten plastic, which can easily cause the displacement of the core and result in significant dimensional errors in hole features. Here’re eight design tips for injection molded holes to enhance the part quality and reduce the potential deformation.
To increase the strength of a hole and prevent it from deforming, a boss feature can be added around the edge of the hole. A similar design can also be used for long holes or slots that require increased strength. It is generally considered that at least 0.3-0.5mm of boss should be reserved to ensure the robust hole structure and to provide enough space for possible other elements or coatings.
It is recommended to maintain the space of at least 1.5x the diameter of the part hole or the wall thickness, whichever is greater, between holes and between holes and the part edge. In other words, s ≥ 1.5t or 1.5D should be followed.
RPWORLD is a leading high-mix, low-volume manufacturing service providers for CNC Machining, Injection Molding, Urethane Casting, Free DFM analysis. Our digital approach to manufacturing enables accelerated time to market, reduces development and production costs, and minimizes risk throughout th...
2K, two-shot, multi-shot, and overmolding are all names for similar processes. Traditionally, overmolding involved taking a part molded in one tool / machine and placing it inside a second tool to have the second material molded over the original part. The result is a part that has a robust bond between the two materials. Modern overmolding is now referred to as 2K or two-shot. This process eliminates the intermediate step of packaging, transporting, and manually loading into a second tool.
Try not to complex the mold structure when designing holes. To simplify the mold structure and reduce the cost of the mold, the design of side holes perpendicular to the parting direction should be avoided.Side holes perpendicular to the parting direction of the part needs the extra side-actions (or side-pulls), which increases the complexity of the mold and leads to higher mold costs.
Vent holes are often required in products, due to the need for heat dissipation. In general, when the vent hole is round, the mold core is cylindrical, which makes it easy to process and results in low mold costs. However, when the vent hole is hexagonal, it is more difficult to manufacture and does not necessarily provide better ventilation. Excessive vent hole design can cause a reduction in part strength, which can be addressed by increasing the strength of the part at the vent hole through adding ribs or bosses.
Since the holes are created by removing material from the parts, the part strength is reduced. Therefore, the area around the holes (especially when there are many holes) is prone to welding marks, the strength of the parts will be further weakened. It is advisable to avoid placing too many holes in the loaded areas of the parts.
A deep hole refers to a long and narrow opening. The direction of the elongated hole should be consistent with the flow direction of the molten plastic to avoid being perpendicular to it, which would impede the flow of the plastic. If the direction of the elongated hole is perpendicular to the flow direction of the molten plastic, it may result in defects and non-uniformity in the final product.
The thickness of the bottom of blind holes should be at least 0.2x the blind hole diameter. A thin bottom can result in a weak blind hole, even surface defects on the backside. If the bottom is too thin, its strength is sacrificed, and you may consider thickening the bottom to strengthen the blind holes as the figure b) shows.
The common holes on plastic parts can be roughly divided into three types: blind holes, through holes, and stepped holes. Through holes are easier to manufacture than blind holes because the cores can be distributed on both sides of the molds, and the through hole depths can be appropriately increased. If the hole is too deep, the stepped hole method can be used instead in molding.
Through the use of automation and innovations in machine and tool design, we are able to provide a two-shot part in the same amount of time it previously took to mold only the substrate. This happens using only one tool and one injection molding machine that is equipped with multiple injection units. The savings is significant and allows us to deliver a high quality part that serves our customers' needs at a fraction of the cost compared to the multiple step process used in the past. Let us help you redesign your two component assembly to take advantage of this technology and reduce your costs.
GETTING A QUOTE WITH LK-MOULD IS FREE AND SIMPLE.
FIND MORE OF OUR SERVICES:
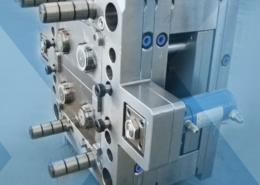
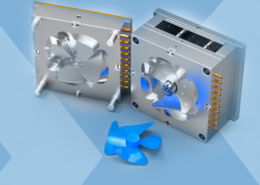
Plastic Molding
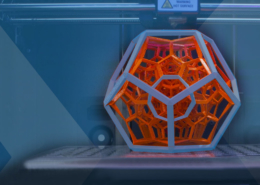
Rapid Prototyping
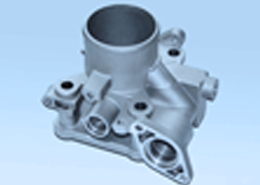
Pressure Die Casting
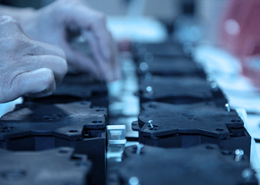
Parts Assembly
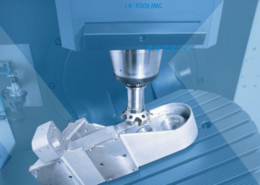