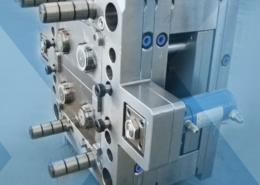
▷ Injection moulding machines at a glance - ENGEL - plastic injection molding pr
Author:gly Date: 2024-10-15
Parts that are made with the structural web process are solid with hollow channels and hollow thick sections packed out by internal injection of low-pressure nitrogen. Benefits of using the structural web process include:
The cost of structural foam injection molding varies based on many factors, including the type and complexity of the product, material used, project requirements, and production run size. There are additional services that can be added that increase costs. These services include finishing processes like drilling and assembly or various post-production testing services.
With Reliant Plastics, an injection molding provider with decades of experience, we can help you to make sense of your options and chart a course towards the best production decisions possible. To explore rapid prototyping with aluminum mold tooling or solutions for producing your parts at a larger scale, contact the Reliant Plastics team today for a free quote.
At Cooper Plastics, we offer numerous other value-added services in addition to our structural foam molding service. These services include product development, finishing, assembly, and more. By offering these services, we elevate the experience for our customers and help them get the most out of our partnership.
Structural foam molding is a desirable plastics manufacturing process if you need to produce large, complex parts with excellent strength-to-weight ratios. It is popular for the production of:
At Cooper Plastics, we are capable of producing both structural foam core and web core plastic products. This versatility is relatively rare in the industry and makes it possible to produce a wide range of plastic structural elements that are durable and cost-effective.
In simple terms, aluminum injection molding is an injection molding process that uses mold tooling made entirely out of aluminum rather than steel. Companies often use this process for large production runs, and the long-term durability of steel is a common demand. However, advances in tooling creation make the use of aluminum a more viable solution for certain scenarios. There is nothing different about the molding process aside from the tooling material.
We can provide customized solutions to meet strength, weight, and materials specifications. Below is an overview of Cooper Plastics structural foam and web capabilities.
Let’s turn our attention to the “gold standard” for most molding projects: steel. Why does steel occupy the top spot over aluminum? The answer lies in three specific benefits.
Consider the company’s capabilities to manufacture both structural foam and structural web products. That’s something you won’t find with every plastic manufacturer. Think about the company’s quality control and testing protocols as well. A company that takes quality control seriously is a company worth considering.
As the material cools, it solidifies into a lightweight yet rigid and strong structure. Companies can mold medium wall thickness or very thick wall sections based on need. This makes structural foam injection molding particularly advantageous for producing large, complex parts that need to be durable without being heavy. Additionally, the reduced pressure involved in the process allows for the use of larger molds and can lead to lower material costs, making it an efficient and cost-effective option for many industries.
Injection molding is a common industrial manufacturing process with multiple businesses relying on the technique to produce items for every industry from healthcare to aerospace. However, not all injection mold tooling is the same—and the choice that you make regarding tooling materials for your project could have a significant impact on the outcome as well as your overall costs.
Overall, with aluminum molds, you’ll experience lower initial costs, lower rejection rates and more opportunities to quickly begin production thanks to shorter tooling production times. With steel, you’ll enjoy durability for very high part volumes, less concern about wear and tear, and opportunities to create more advanced parts.
Another quality indicator is the company’s investment in advanced technology and equipment. The best structural foam molding companies like Cooper Plastics have state-of-the-art machines that offer precise control over the manufacturing process, resulting in product consistency and strict adherence to project specifications.
Do businesses always want the durability of steel for a molding project? Not necessarily. Manufacturers choose aluminum most often when they need to quickly produce parts without requiring a very high volume. Since aluminum tools wear out faster, their optimal use is for lower part production volumes. They’re also an excellent choice when you need to rapidly produce prototype parts for testing, modification and redesign.
There are several key benefits to using aluminum molds for plastic injection, not only its suitability for prototyping. Consider a few of the perks that make manufacturers choose aluminum just as often as steel.
You must evaluate several factors to identify quality structural foam molding companies. A good place to start is with the level of expertise. Does the company have extensive experience with foam injection molding services? A dependable company will have a proven track record of producing structural foam parts with consistent quality and durability. This means knowing which materials and processes will yield the best results.
As with aluminum, there are some downsides to using steel tooling. It’s crucial to include these factors in your considerations during the project planning stage.
Want to discuss a question or comment related to plastics manufacturing and our services? Contact us via the contact form below. A team member will review your submission and follow up as soon as possible.
While there are some obvious benefits to using aluminum, there are several reasons why steel molds for plastic injection has remained a dominant choice. Aluminum comes with some disadvantages you must consider, including the following.
Key features often include multi-nozzle systems to ensure even distribution of material and foaming agents, as well as precise control over injection speeds, pressures, and temperatures. Advanced structural foam molding machines are also equipped with state-of-the-art monitoring systems that allow operators to fine-tune the process in real time.
Other structural foam materials that can be utilized include polypropylene (PP) and acrylonitrile butadiene styrene (ABS). These materials are known for their strength and impact resistance, making them ideal for components that require a balance of rigidity and reduced weight.
Structural foam injection molding is a method of creating lightweight, durable plastic products. The process is cost-effective due to reduced material usage and the ability to create large, complex parts in a single molding cycle. The structural foam molding process includes the following steps:
The material used in the structural foam process is critical to achieving the desired product properties and aesthetics. Selection is often based on application requirements such as chemical resistance, dimensional stability, or the ability to withstand environmental stress. One of the benefits of working with Cooper Plastics is that we have an experienced team that can provide recommendations to ensure the final product is cost-efficient and meets industry and application specifications.
Structural foam injection molding is a unique manufacturing process that combines traditional injection molding with a foaming agent to create parts with a foamed core and solid outer skin. The process begins by heating thermoplastic material until it becomes molten. At this point, a foaming agent is introduced into the material, which will later cause the plastic to expand and form the characteristic foam structure. The molten, gas-infused material is then injected into a mold under lower pressure than in conventional injection molding. This lower pressure allows the foaming agent to expand within the mold cavity. When the material contacts the mold walls, the surface cells collapse. This results in a core of interconnected cells surrounded by outer layers that make up a smooth, dense, solid skin.
The machine we utilize at Cooper Plastics is relatively unique in that it allows us to manufacture both structural foam and structural web products. This versatility enables our customers to get ultra-large plastic parts that wouldn’t be possible with other molding technologies.
Finally, you never want to overlook customer service. Seek a plastics manufacturing partner that will work closely with you throughout the entire process, from initial design to final production. The company should offer guidance, support, and communication that will ensure a project that you are completely satisfied with.
Structural foam molding machines are typically high-tonnage injection molding presses equipped with advanced controls and capabilities to manage the lower pressure required for the foaming process. The machines are designed to accommodate larger molds and produce consistent, high-quality components.
Traditionally, injection mold tooling uses steel as the primary material, but it is not the only option. Today, aluminum molds have earned a place in the industry. Let’s explore aluminum injection molding and why it is worth your consideration in some cases.
Which should you choose: steel or aluminum? With clear pros and cons to each material, the answer depends on the specific needs of your projects. Partnering with an experienced and highly capable plastics manufacturer offers you the insights that you require to make smart decisions at every step, including in material selection.
Want to partner with Cooper Plastics for your structural foam injection molding needs? Request a free quote or contact us for more information.
Seek transparency from the company you’re considering by requesting a detailed quote. Getting a breakdown of anticipated production costs will allow you to decide whether you want to proceed with the project, make adjustments and get a new quote, or drop the company from your consideration list and vet a different company.
GETTING A QUOTE WITH LK-MOULD IS FREE AND SIMPLE.
FIND MORE OF OUR SERVICES:
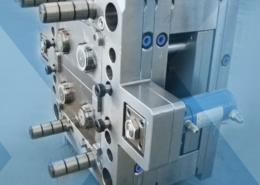
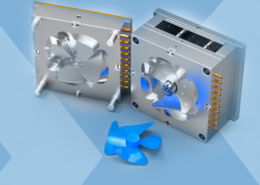
Plastic Molding
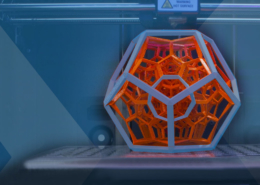
Rapid Prototyping
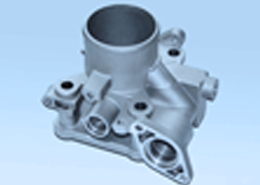
Pressure Die Casting
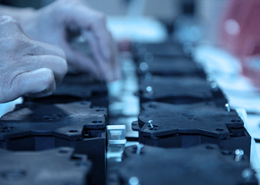
Parts Assembly
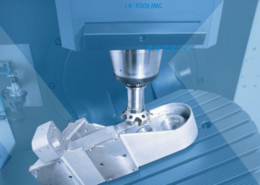