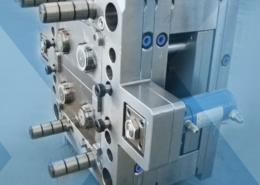
Why make prototype injection mold tooling? - prototype plastic molding
Author:gly Date: 2024-10-15
Manufacturers can immediately notice that the choice of material affects the flow or movement of the molten plastic inside the mold chamber in the mold cavity because it is a recurring factor in many problems.
Recycled plastics offer a compelling alternative, addressing both environmental concerns and the need for sustainable manufacturing. Contrary to misconceptions, recycled plastics have evolved into high-quality materials suitable for injection moulding, offering a plethora of advantages.
To get your components or sub-assemblies manufactured by us, you can call our team on 01543 462 561 or send an email enquiry to [email protected]. Our team of experts will be in contact within hours to help you with your project.
The secret to effective manufacturing and preventing either flow or pressure concerns is to match the right part with the proper molding machine.
Looking ahead, the future of recycled plastics in injection moulding is teeming with possibilities. Researchers and industry experts are exploring innovative methods to enhance the performance of recycled materials, opening doors to even more sustainable practices.
The production line might have a resin with a high viscosity measured by the Melt Flow Index (MFI), depending on the chosen material. MFI is a good starting point, even though it may not tell the complete story since there are two other factors of concern that may also be involved.
Quantifiable benefits extend beyond cost reduction. Improved product quality, a significant decrease in waste generation, and a positive response from consumers all contribute to the success of manufacturers embracing recycled plastics.
Mould design plays a crucial role in the successful implementation of recycled plastics. Consult with experienced mould designers who understand the unique characteristics of recycled materials. Adjustments may be necessary to optimise the performance of recycled plastics in the moulding process.
For instance, an oversized machine may have trouble controlling pressure if the shot size is less than 25% of its capacity, whereas an undersized machine will not have enough pressure or ram speed. Meanwhile, the barrel and mold wall should be heated to prevent the molded plastic from cooling too quickly.
These holes frequently appear around the borders of the finished product or in areas where the mold wall is typically thin—these areas are the last places a mold would commonly fill.
I recall a project where initial scepticism was replaced by amazement as a state-of-the-art injection moulding machine effortlessly processed recycled plastics, producing components of exceptional quality. Technological progress is propelling the industry towards a future where recycled plastics are not just viable but preferable.
During my tenure, I’ve observed that regulatory compliance, when approached as an opportunity rather than a burden, fosters long-term business sustainability. Adhering to eco-friendly practices is not merely a legal requirement; it is an investment in the company’s future resilience.
2. Cost Efficiency: Recycled plastics often come at a lower cost, providing manufacturers with a competitive edge while contributing to overall cost reduction.
Navigating the regulatory landscape is a concern for every conscientious manufacturer. However, the use of recycled plastics aligns seamlessly with existing environmental standards and often exceeds compliance requirements. This alignment not only ensures legal adherence but also positions the company as a responsible industry leader.
Undoubtedly, the environmental impact of traditional plastic manufacturing cannot be ignored. The proliferation of plastic waste has reached alarming levels, prompting global concern and stringent regulations. As manufacturers, we hold a pivotal role in steering the industry towards eco-friendly practices.
One common hurdle is the perception that recycled plastics compromise product quality. Allow me to dispel this myth. Technological advancements have elevated the quality of recycled plastics, ensuring they meet or exceed the standards set by their virgin counterparts.
With many accumulated years of experience with numerous domestic and foreign clients, Flying Tiger is confident in assisting corporate customers in quickly identifying the cause of short shots and other injection molding defects, thereby assisting in cutting down on resource waste and boosting product yield.
Like any production process, plastic injection molding manufacturing can have problems and faults. Short shots, often known as "shorts," are one of the most typical quality concerns when the final product is incomplete because the mold did not entirely fill. This article will examine the most frequent causes of this issue and how plastics manufacturers can troubleshoot short shots to maintain high-quality and lean production.
1. Reduced Environmental Footprint: Utilising recycled plastics significantly diminishes the demand for new raw materials, alleviating the strain on our ecosystems.
Consult Flying Tiger today if your business is looking for a partner to co-create reliable, high-quality manufacturing outputs.
A "short shot," as the name suggests, occurs when the mold-forming filling stops before the mold chamber is fully filled with the melt, leaving holes or thin sections and producing a defective product.
Therefore, it is squeezed instead, leaving some partially empty spaces in the cavity and shortening the shot of the molded item. To remove the air, the process must have vents built or ejection pins installed.
The most frequent cause of failure to fill the mold is the appearance of something that interferes with the flow, and one of the leading candidates for flow issues is the type of plastic polymer itself.
Overall, several factors can lead to the occurrence of short-shot defects, and they all have mutually limiting and influencing effects. Manufacturers must consider how these factors relate to one another, in order to devise a solution to reduce and correct short-shot defects. Note that It is often an ongoing process of monitoring and reviewing.
Nozzles, sprues, runners, gates, and thin product walls are among the parts that could obstruct melt flow. By raising the nozzle's diameter and temperature, besides utilizing a nozzle with a low flow resistance, the flow resistance of the nozzle can drop to the desired level.
Short shots are one of the most frequent problems with plastic injection molding. There are numerous causes of them, but the primary ones are improper injection pressure and speed, including uncontrolled pressure loss brought on by resistance.
Additionally, because the filling speed is excessively high, chances are that there is insufficient time to release the air via the separating surface.
Flow restrictions, hesitation of flow, and inadequate venting are all common short-shot defects due to inadequate mold design. Flow restrictions often come from the positioning, dimensions of runners and their gates, and how the molten plastic is poured into the mold.
The imbalanced flow in each cavity of a multi-cavity mold can generate local short shots. But when the injection molding machine's capacity is adequate, this defect is primarily brought on by the uneven flow in each gate or the uneven distribution of the mold cavities.
In the dynamic landscape of manufacturing, the call for environmental sustainability has become increasingly resonant. As a seasoned professional in the field of plastic injection moulding, I am eager to guide environmentally conscious manufacturers, on the transformative journey of incorporating recycled plastics into their injection moulding processes.
3. Enhanced Corporate Image: Embracing recycled plastics showcases a commitment to environmental responsibility, enhancing brand reputation and resonating with conscientious consumers.
In plastic injection molding, a flow hesitation occurs when the flow slows down or stops due to variations in mold thickness. Inconsistent mold thickness causes the flow range of the melt to be too broad and its flow resistance to be excessive.
In conclusion, the journey of recycled plastics in injection moulding is a testament to the industry’s adaptability and resilience. As we stand at the intersection of environmental consciousness and manufacturing innovation, the decision to embrace recycled plastics is not just a choice; it’s a commitment to a future where waste is minimised, and opportunities are maximised.
I urge manufacturers, particularly those with a keen eye on sustainability, to consider the transformative power of recycled plastics. In doing so, we not only safeguard the environment but also future-proof our businesses, ensuring they thrive in a world that values ecological responsibility.
Let’s delve into real-world examples of manufacturers overcoming challenges. In a recent case study, a forward-thinking company integrated recycled plastics into their injection moulding processes, witnessing a 20% reduction in material costs without compromising product quality. These success stories underscore the tangible benefits awaiting those willing to embrace change.
Therefore, beyond the choosing material, better control of mold and melt temperatures also aids in enhancing plastic flow. Flying Tiger offers a range of mold temperature controllers that help you achieve just that.
As industry leaders, we bear a collective responsibility to shape a sustainable future. Collaboration, knowledge-sharing, and the pursuit of cutting-edge technologies will define the next chapter in injection moulding. By fostering an environment of continuous improvement, we ensure the longevity of our industry and the planet.
Another potential reason is that the vacuum condition is not suitable for molds—Molds require a place for displaced air to escape, or they will develop air traps or poor venting.
While the initial investment in transitioning to recycled plastics may raise concerns, conducting a thorough cost analysis reveals the long-term savings potential. Factor in reduced material costs, potential tax incentives for sustainable practices, and the positive impact on brand perception.
There are a variety of tools, procedures, and materials available for manufacturers to avoid short-shot defects. Four of the most tried-and-tested remedies are listed below:
Overall, it is crucial to comprehend the various varieties of plastic injection molding equipment and how varying sizes and types might be beneficial.
In these success stories, there is a common thread of adaptability, open-mindedness, and a willingness to experiment. Embracing recycled plastics requires a cultural shift within the organisation, with employees at all levels understanding and championing the cause.
Transitioning to recycled plastics requires a strategic approach. Begin by conducting a comprehensive assessment of your current processes and materials. Identify suitable recycled plastics for your specific applications and gradually integrate them into your production line.
Poor venting happens when air is trapped during filling the cavity, creating counterpressure. When the melt is first injected into the hollow, under most circumstances, it immediately seals the cavity, trapping air in the remaining local spaces.
We can advise on the design of your product to suit the manufacturing processes required. We can organise tooling for you and manage the project for you so that you receive conforming parts at a competitive price. And we’ll keep doing that for you for as many years as you need us to.
Allow me to share a notable success story from my own experience. A mid-sized manufacturing firm, initially hesitant to adopt recycled plastics, witnessed a remarkable transformation. After implementing recycled materials, they not only contributed to environmental conservation but also experienced a 15% reduction in production costs.
GETTING A QUOTE WITH LK-MOULD IS FREE AND SIMPLE.
FIND MORE OF OUR SERVICES:
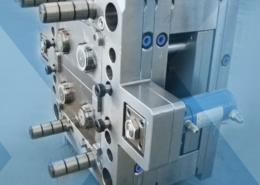
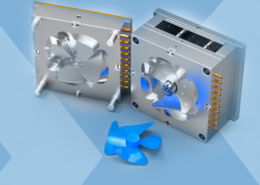
Plastic Molding
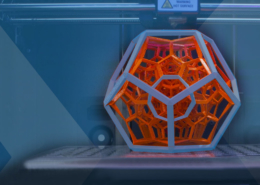
Rapid Prototyping
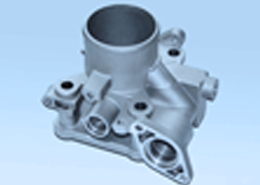
Pressure Die Casting
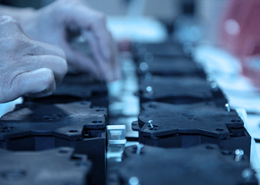
Parts Assembly
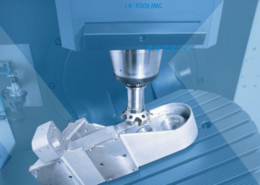