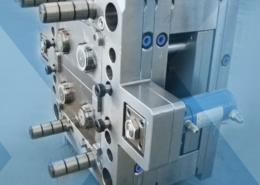
WHY OVERMOLDED A METAL PART ? - Delmon Group - overmolding metal with plastic
Author:gly Date: 2024-10-15
Once these new devices are produced, we assist our customers in transitioning the project into the production phase. Quality and customer satisfaction are our primary goals, and Aberdeen can work with both high and low quantity requirements with over 700 square feet of cleanroom injection molding space.
The EM Granulator Series is designed for maximum versatility. This press side granulator is operator friendly, easy to service and maintain. Precision scissor cut action provides maximum through-put efficiency. Four models are available with features including manual or robotic feed, safety interlock time delay, D2 high carbon steel knives and a tangential feed design.
TempTek chillers provide precision temperature control in fluid cooling for industrial processes. Our units are affordable and dependable. Chillers come in models for Indoor, outdoor, portable use plus remote condenser models with enough capacity to serve multiple process applications. Temptek is the affordable answer for processors in plastic injection molding, blow molding, extrusion and other industrial applications that require cooling.
Prime examples were molding non-communicating passageways through a plastic manifold, molding critical tolerance pacemaker components, and even molding around glass formations without breaking or cracking. Our advanced injection molding equipment makes even the most difficult projects possible.
The hot oil temperature controller is built with cast and welded components in the circulation system to minimize leaks and is suitable for use in plastics, rubber, die casting and other processes that require fluid temperatures to 500°F.
Pump tank stations are available with Polyethylene and steel tank models designed to support cooling equipment including evaporative cooling towers, central chillers, and fluid coolers. Our stations have a vented reservoir with fluid pumps and controls selected to meet the needs of your process and/or the entire facility. Standard units are designed to be installed indoors or in an environment protected from the elements.
The process is capable of making FDA approved medical devices that are both durable and reliable. This type of molding can also be used to make prototypes to send and get the much-needed FDA approval. Medical injection molding can be performed in a clean room and the components can be sterilized without harm as well. Let's take a look at injection molding.
Since 1988 Temptek has provided reliable and affordable auxiliary equipment to use industrial manufacturing companies in a wide range of industries across a variety of industries in Material Handling, Process cooling, Size reduction, Temperature control. With over 160 years of combined service providing for all industries. since 1988. Injection Molders, extruders, blow molders, thermoformer, roto molders and compounders
However, there are other types of plastics called thermosets that also can be used for injection molding, but the process is far different. These materials are most likely not going to be used for medical molding as they cannot be recycled as easily as the thermoplastic materials. Because of this, you don't see thermosets used as often as you do thermoplastics. A good example of a thermoset is your car tires. This is where they cannot be melted down and reshaped into something.
Southwest Heater & Controls is dedicated to providing customers with process solutions, technical expertise, quality equipment, and prompt professional service. We hold to a high standard of integrity, customer service, and respect for our business partners.
The most common types of materials used in medical insert molding are thermoplastics. These are materials that can be heated up into a molten state and pushed through a barrel into a mold. These molds can simply be open and shut type designs, which are what you would expect for, say a simple product such as a cake mold. Or they can be very complex with moving side parts called slides. Of course, the simpler the mold the better for maintenance and longevity. However, complex parts will need these complex designs in order to produce the desired part.
Injection molding is a very common way to form plastic parts and components. Depending on the material, the parts can be very strict with their tolerances as well as easy to process. Injection molding is one of the most common types of forming plastics. It is used in a variety of industries and not just for medical injection molding. In fact, you probably have a wide variety of injection molded parts all around you and simply don't know it. Your basic pens, your keyboard, and even your phone have injection molded components in them.
Temptek cooling towers provide energy efficient evaporative cooling with capacities and flow rates from forty-five tons-135 GPM to 270 tons - 810 GPM. Our towers are a Non-ferrous design with UV stabilized fiberglass shell.
In the medical field, we often see metal combined with the plastic part. This is called insert molding and is a very common practice for injection molders to do. You see this all over the medical arena from needles to EKG hook up leads and more.
We provide assistance throughout each stage of your program, from design recommendation through mold tooling fabrication, prototyping, first article approval, process validation, full scale production medical molding, and transfer of turnkey system to customer facilities if requested.
Temptek desiccant dryers use the industry standard dual-bed drying concept in a compact single blower configuration. One blower and multi-function valve controls both the process and regeneration flow and the heaters are contained within the desiccant beds to minimize space.
Sometimes the components need to be manufactured separately and then assembled. This is very common in many cases and this can be done by hand or robot.
Medical injection molding is a manufacturing process that produces plastic medical devices and components. It involves melting plastic resin pellets and injecting the molten material into a mold to create a specific shape. This process allows for precise control over the product's size and shape and is subject to strict quality and regulatory standards.
Aberdeen’s primary goal is total customer satisfaction for even your most challenging projects. Our company culture is one of honor, respect and service with the highest degree of competence and professionalism that you will find anywhere.
Medical injection molding is a core technology of Aberdeen Technologies and represents a cutting edge solution to the manufacturing needs of healthcare companies who produce medical molded devices. As an insert molding manufacturer, we provide assistance to device manufacturers who approach us with new product concepts and ask us to mold parts for clinical trials and marketing evaluations.
Central water chillers are designed to circulate a fluid medium (typically water, or a water-glycol solution) through a process for cooling and maintaining temperatures from 20F to 65F.Central models provide capacity to serve multiple process applications.
Thermolator water temperature control units circulate water through the process application for temperature control. Temperature control units offer temperature range control from 30°F to 300°F.
emptek Series Vacuum Loaders provide self-contained, vacuum transfer of plastic pellets and regrinds over short distances using powerful single-phase vacuum motors. Standard models are made for flange mounting to existing bins or hoppers. Machine Mount packages provide a quick disconnect glass tube base with integrated vacuum flapper.
Including Water and Oil circulating Thermolators,’ Chillers, cooling towers, pump stations, Granulators, Material Hopper Pellet loaders and resin Dryers.
GETTING A QUOTE WITH LK-MOULD IS FREE AND SIMPLE.
FIND MORE OF OUR SERVICES:
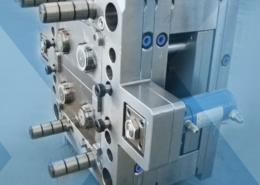
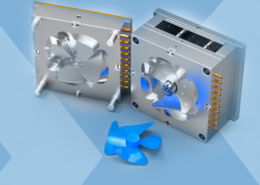
Plastic Molding
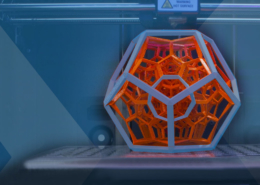
Rapid Prototyping
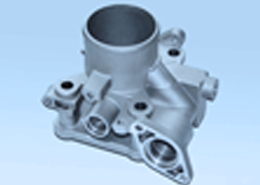
Pressure Die Casting
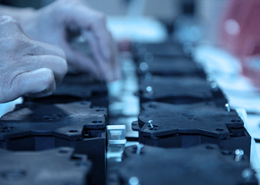
Parts Assembly
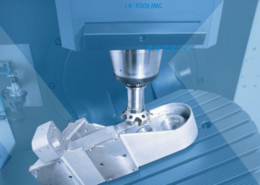