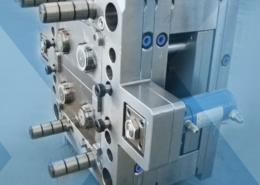
WHY OVERMOLDED A METAL PART ? - Delmon Group - overmolding metal with plastic
Author:gly Date: 2024-10-15
Our large part injection molding operation is optimized for producing high-quality, complex products. we support our customers providing knowledge and expertise to make better products, solve plastic parts manufacturing problems, and find economic solutions that help drive product development to yield higher quality parts.
Large parts necessitate careful consideration of material flow within the mold to prevent issues like uneven filling, weld lines, or voids.
• Capabilities include: Injection, structural foam and gas-assist.• Robotics and in-house manufactured end-of-arm tooling ensures competitive cycle times.• Full finishing capabilities including: paint, decorating, shielding, and assembly.
Large part injection molding is a specialized manufacturing process used to produce large and complex plastic components or parts. This technique is an extension of traditional injection molding, which is commonly used to make smaller plastic parts. Large part injection molding is typically employed when the size, shape, or complexity of a component exceeds the capabilities of standard injection molding machines.
Metal is expensive and heavy. Polyethylene molds are inexpensive and lightweight, which cuts costs in transportation as well as production. With a polyethylene mold, you can create a varied design with hollow parts, complex undercuts, or varied shapes and sizes. Roto Plastics can take an intricate design and simplify it using polyethylene.
Plastic injection molding machines are categorized based on their tonnage or clamping pressure, and they come in various sizes, ranging from as low as five tons to as high as 3,000 tons of clamping force. Importantly, the higher the ton rating, the larger the machine itself. Large-tonnage injection molding machines demand significant resources, occupying a substantial footprint, typically around 40′ x 15′ x 15′, and costing anywhere from $250,000 to well over $1 million. These machines are used for processing injection molds that can exceed 10,000 pounds and require special lifting equipment. The key distinction between large-part plastic injection molding machines and standard ones lies in the complexity of parts they produce, their higher acquisition cost, and the considerable space needed for staging, packaging, and storing parts. Consequently, fewer companies opt for machines surpassing 500 tons, making them rarer and unique in the industry.
When determining the appropriate press size, several factors come into play, including the part’s dimensions, the type of polymer being used, and a safety margin. The safety margin is an extra percentage added to the calculation to minimize the risk of defects in the final product, with experts often recommending a 10% buffer for this purpose. A general guideline for calculating the necessary tonnage for plastic production is to use 2-8 tons per square inch. For example, a 10″ x 10″ part (100 square inches x 2 tons/sq. in.) would require 200 tons. It’s crucial to note that larger parts necessitate more clamp force to secure the mold halves during the injection process.
Overcoming the challenges of large part injection molding while managing costs requires a combination of careful design, advanced technology, and skilled personnel. Companies must weigh the initial investment against the long-term benefits of producing large parts with high precision and quality. Additionally, the choice of materials and production methods can influence both cost and quality outcomes.
Plastic large part injection molding differs from standard plastic injection molding in several key ways due to the unique challenges posed by the size and complexity of large components. Here are key considerations in large part injection molding.
Converting your product to plastic has many advantages for you. Molding with polyethylene is an excellent choice if your business wants to cut costs, make product design more effective, increase durability, or simplify an intricate, outdated part.
Large part mold designs may require additional features like ribbing and stiffening to maintain structural integrity without adding excessive weight.
Here are some specific parts or products that are commonly produced using large part injection molding in various industries.
Quality, innovation, and value have laid the foundation for our success as a nationwide rotational molder. Roto Plastics goes above and beyond by rotomolding custom parts with polyethylene to meet and exceed our customers' needs. We listen to our clients' concerns and assist them in creating the parts they need, even if they've never considered plastics for their product before.
Instead of several heavy, metal pieces, your design can become one lightweight polyethylene piece. We can also create variable wall thicknesses, to create a pleasing, durable custom molded part for you. Aesthetics are made easier with polyethylene. Changing colors, creating a piece that is opaque or translucent is easy with a polyethylene mold. Parts can be used as insulators, are relatively stress-free, and resist corrosion.
Specialized injection techniques, such as sequential valve gating, may be employed to control the flow of molten plastic in large molds, reducing the likelihood of defects.
Plastic Mold Manufacturing Plastic Injection MoldingRapid PrototypingCNC MachiningSheet Metal StampingPressure Die CastingSilicone & Rubber PartsSurface Finishing
Designers at Roto Plastics are leaders in converting metal products to polyethylene parts. Consider converting your metal piece into plastic.
One-stop services provided: mold creation, rapid prototyping, large part CNC machining, injection molding, overmolding ,insert molding, etc.
Molds for large parts are more substantial and intricate. They need to withstand the forces of injection and the weight of the molten plastic.
Large parts are more susceptible to defects due to their size, so stringent quality control measures are essential to ensure they meet design specifications.
Large part injection molding differs from standard injection molding due to the need for specialized machinery, molds, and techniques to handle the size and complexity of the components. The challenges of material flow, cooling, and quality control are amplified when producing large parts, making this process a distinct and specialized branch of plastic injection molding.
Handling and removing large parts manually can be impractical and unsafe. Robotic systems are often used for these tasks.
Sungplastic is a plastic product manufacturer with rich experience in injection molding. According to the different product development requirements, we flexibly adjust the manufacturing process to achieve high quality, high efficiency and more economical.
Designing for large part injection molding demands careful consideration of these principles to achieve high-quality, defect-free parts. Collaboration between part designers and mold designers is essential to optimize part and mold geometry for efficient and cost-effective production. Additionally, computer-aided design (CAD) and simulation tools can aid in refining part and mold designs before physical production begins, reducing the risk of costly errors.
Large parts require specialized, often much larger injection molding machines with higher clamping forces. Standard machines are typically not equipped to handle the size and weight of large molds and parts.
Plastic materials with excellent flow properties and strength are typically chosen for large parts. Reinforced plastics may be used for added strength.
We offer a variety of manufacturing services: Rapid Prototyping, Tool Making, Injection Molding, Product Design and Development, CNC Machining and Metal Stamping. You can choose from a variety of plastics, silicone rubber, or metal for your product. Regardless of mass production or small batch customization, Sungplastic has always been committed to providing assured, efficient and more economical one-stop processing services for your projects.
Determining whether large part injection molding necessitates a large-ton machine also involves a comprehensive assessment of various factors, encompassing measuring and weighing the parts, considering the size and intricacy of the molds, reviewing material requirements, injection pressure, and shot size, as well as accommodating longer cooling times and quality standards. Cost considerations, both for machine acquisition and operation, play a crucial role.
Cooling large parts can be challenging due to their thickness, requiring longer cooling times and more extensive cooling systems.
At Sungplastic, we are not only good at large parts CNC machining, but also have ample production experience in large part injection molding. If your project involves large part injection molding services, please learn more to proceed successfully.
Polyethylene is the most widely used form of plastic. Because of its unique chemical properties, polyethylene is a diverse plastic with many uses. This plastic is lightweight, tough, resistant to corrosion, impermeable, and a great insulator.
If you are investing in large part injection molding projects, Sungplastic will solve your doubts and provide the best manufacturing services.
Gas assist injection molding might be used to hollow out thick sections of large parts, reducing material usage and cycle times.
GETTING A QUOTE WITH LK-MOULD IS FREE AND SIMPLE.
FIND MORE OF OUR SERVICES:
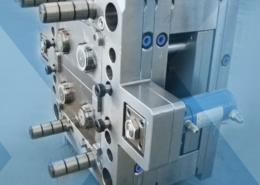
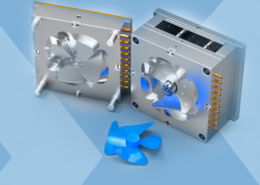
Plastic Molding
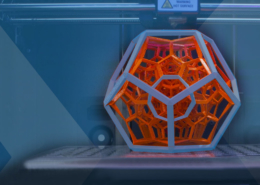
Rapid Prototyping
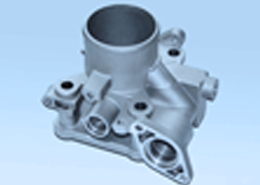
Pressure Die Casting
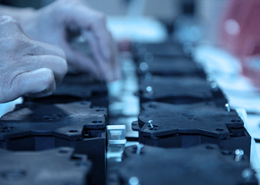
Parts Assembly
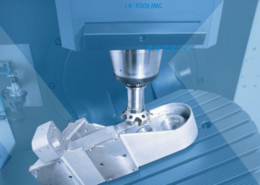