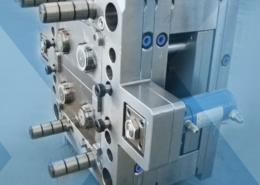
Exploring Large Scale Injection Molding: Revolutionizing Manufacturing
Author:gly Date: 2024-06-08
Large scale injection molding stands as a cornerstone of modern manufacturing, captivating industry professionals with its ability to produce complex components on a massive scale. Originating from the process of injecting molten material into a mold cavity at high pressure, large scale injection molding has revolutionized the production of various products across diverse industries. This article delves into the intricacies of large scale injection molding, exploring its applications, advancements, challenges, and future prospects.
Introduction to Large Scale Injection Molding
Large scale injection molding, also known as high-volume injection molding, involves the mass production of plastic parts through the injection of molten material into a mold cavity. This process is characterized by its high efficiency, repeatability, and precision, making it a preferred choice for industries requiring large quantities of identical components. With advancements in machinery, materials, and automation, large scale injection molding has become indispensable in automotive, consumer electronics, packaging, and beyond.
Applications Across Industries
Automotive Industry
Large scale injection molding plays a pivotal role in the automotive industry, where it is used to manufacture various components ranging from interior trim panels and dashboard components to exterior body parts and structural elements. The ability to produce lightweight, durable, and aesthetically pleasing parts at high volumes makes injection molding indispensable for automotive manufacturers seeking to optimize performance, safety, and cost-effectiveness.
Consumer Electronics
In the realm of consumer electronics, large scale injection molding enables the production of sleek and functional components for devices such as smartphones, laptops, and home appliances. The demand for lightweight, durable, and customizable parts drives innovation in injection molding technologies, allowing manufacturers to meet the ever-evolving needs of consumers while maintaining competitive pricing and time-to-market advantages.
Packaging Industry
The packaging industry relies heavily on large scale injection molding to produce a wide range of containers, caps, closures, and packaging components. With growing emphasis on sustainability and product differentiation, injection molding offers packaging manufacturers the flexibility to create eco-friendly designs, intricate shapes, and vibrant colors to enhance brand visibility and consumer appeal.
Advancements in Technology and Materials
Machinery and Equipment
Advancements in injection molding machinery and automation have significantly enhanced the efficiency, speed, and precision of large scale production. Modern injection molding systems feature advanced controls, robotics, and digital monitoring capabilities, enabling real-time adjustments and optimization of production processes to maximize output and minimize waste.
Materials Innovation
The development of new materials and additives has expanded the capabilities of large scale injection molding, enabling manufacturers to achieve superior performance, aesthetics, and sustainability. From engineering-grade resins to bio-based polymers, the versatility of injection molding materials continues to grow, offering solutions tailored to specific applications and regulatory requirements.
Challenges and Considerations
Tooling and Mold Design
Designing molds for large scale injection molding requires meticulous attention to detail, considering factors such as part geometry, material selection, and production volumes. The complexity of tooling design influences production costs, cycle times, and part quality, necessitating collaboration between designers, engineers, and mold makers to optimize mold performance and longevity.
Quality Control and Assurance
Maintaining consistent quality across large scale injection molding operations requires robust quality control measures and inspection protocols. Variations in material properties, processing conditions, and environmental factors can impact part dimensions, surface finish, and mechanical properties, highlighting the importance of comprehensive testing, monitoring, and corrective actions to ensure compliance with industry standards and customer requirements.
Future Perspectives and Innovations
Large scale injection molding continues to evolve with ongoing advancements in technology, materials, and sustainability initiatives. Research efforts are focused on improving process efficiency, reducing environmental impact, and enhancing part performance through innovations such as bioplastics, digital twin simulations, and additive manufacturing integration. Furthermore, the adoption of Industry 4.0 principles, including data analytics and predictive maintenance, promises to usher in a new era of smart manufacturing, where large scale injection molding becomes even more agile, adaptive, and sustainable.
Conclusion
In conclusion, large scale injection molding represents a cornerstone of modern manufacturing, offering unparalleled efficiency, precision, and scalability for producing complex components across diverse industries. Despite facing challenges such as tooling complexity and quality assurance requirements, the benefits of large scale injection molding outweigh the drawbacks, making it a vital technology for meeting the demands of global markets. As we look to the future, continued investment in technology, materials, and sustainability initiatives will drive innovation and propel the evolution of large scale injection molding towards greater efficiency, flexibility, and environmental responsibility.
Through this exploration, we have gained insights into the transformative potential of large scale injection molding and its implications for industry stakeholders. By embracing innovation and collaboration, we can unlock new opportunities and address existing challenges, ensuring that large scale injection molding remains at the forefront of manufacturing excellence in the years to come.
GETTING A QUOTE WITH LK-MOULD IS FREE AND SIMPLE.
FIND MORE OF OUR SERVICES:
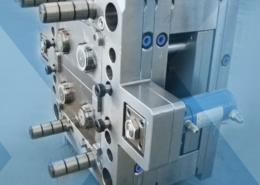
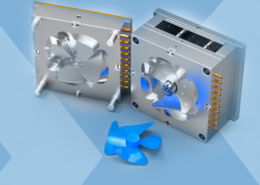
Plastic Molding
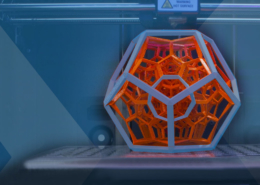
Rapid Prototyping
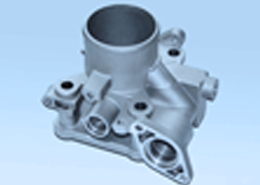
Pressure Die Casting
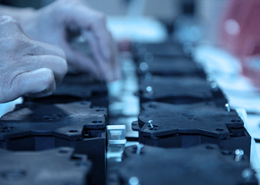
Parts Assembly
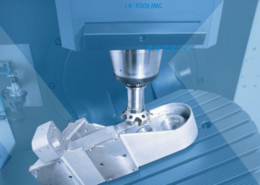