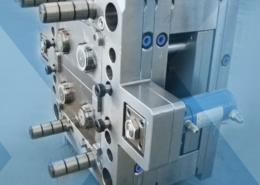
Exploring the Versatility of Molded Parts: An Insight into Manufacturing Excelle
Author:gly Date: 2024-06-08
Molded parts represent the epitome of precision engineering and manufacturing ingenuity, serving as integral components across a myriad of industries. From automotive components to consumer electronics and medical devices, molded parts play a ubiquitous role in modern-day life. This article embarks on a journey to unravel the multifaceted world of molded parts, shedding light on their significance, applications, design considerations, and future prospects.
The Significance of Molded Parts
Molded parts stand as pillars of innovation and efficiency in manufacturing, offering unparalleled versatility, precision, and cost-effectiveness. By harnessing the power of injection molding, rotational molding, or compression molding processes, manufacturers can produce intricate components with consistent quality and dimensional accuracy. From intricate geometries to high-performance materials, molded parts encapsulate the essence of modern engineering excellence, enabling the realization of complex designs and product functionalities.
Applications Across Industries
The versatility of molded parts transcends industry boundaries, finding applications in automotive, aerospace, healthcare, consumer goods, and beyond. In the automotive sector, molded parts constitute essential components of vehicle interiors, exteriors, and under-the-hood assemblies, contributing to safety, performance, and aesthetics. Similarly, in the healthcare industry, molded parts play a critical role in medical device manufacturing, ensuring reliability, biocompatibility, and regulatory compliance. From everyday consumer products to mission-critical industrial machinery, molded parts underpin diverse applications, underscoring their indispensability in modern manufacturing.
Design Considerations and Material Selection
The design and material selection process is pivotal in ensuring the functionality, durability, and cost-effectiveness of molded parts. Design engineers must consider factors such as part geometry, material properties, manufacturability, and regulatory requirements to optimize part performance and production efficiency. Utilizing advanced CAD software and simulation tools enables engineers to iterate on designs, optimize part geometries, and anticipate potential manufacturing challenges. Additionally, selecting the appropriate material, whether it be thermoplastics, thermosets, or elastomers, dictates the mechanical, thermal, and chemical properties of the molded part, influencing its suitability for specific applications and operating conditions.
Optimization Strategies and Future Prospects
Continuous innovation and optimization drive advancements in molded part manufacturing, paving the way for enhanced performance, sustainability, and cost-effectiveness. Leveraging technologies such as additive manufacturing, micro-injection molding, and multi-material molding enables manufacturers to push the boundaries of design complexity, material versatility, and production efficiency. Moreover, embracing principles of circular economy, such as material recycling and closed-loop manufacturing, fosters sustainability and resource conservation across the product lifecycle. Looking ahead, the convergence of digitalization, automation, and materials science holds promise for unlocking new frontiers in molded part manufacturing, heralding an era of unprecedented innovation and efficiency.
Conclusion: Embracing Excellence in Molded Part Manufacturing
In conclusion, molded parts represent the epitome of manufacturing excellence, embodying precision, versatility, and innovation. As industries continue to evolve and embrace new technologies, the demand for high-performance, cost-effective molded parts will only continue to rise. By understanding the significance, applications, design considerations, and future prospects of molded parts, stakeholders can navigate the complexities of modern manufacturing with confidence and foresight. As we embark on the journey towards a sustainable and innovative future, molded parts will remain at the forefront of technological advancement, driving progress and shaping the world around us.
GETTING A QUOTE WITH LK-MOULD IS FREE AND SIMPLE.
FIND MORE OF OUR SERVICES:
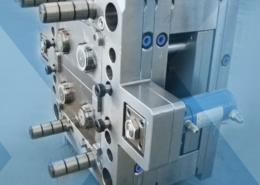
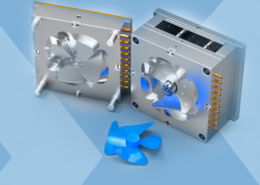
Plastic Molding
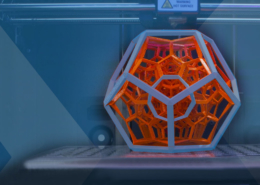
Rapid Prototyping
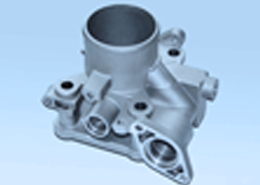
Pressure Die Casting
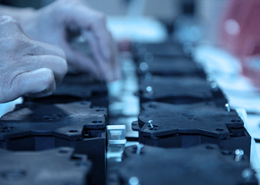
Parts Assembly
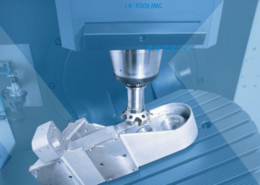