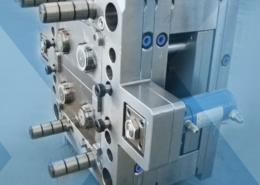
Exploring Medical Molding: Revolutionizing Healthcare Solutions
Author:gly Date: 2024-06-08
In the realm of healthcare, medical molding stands out as a cornerstone of innovation, offering transformative solutions that enhance patient care and drive medical advancements. This article delves into the intricate world of medical molding, unveiling its significance, processes, applications, and future prospects.
The Evolution of Medical Molding
Medical molding traces its roots back to the mid-20th century when advancements in materials science and manufacturing techniques paved the way for the production of intricate medical devices and components. Since then, the field has undergone a remarkable evolution, driven by technological innovation, regulatory requirements, and market demand.
From simple syringes to complex implantable devices, medical molding encompasses a diverse array of applications, spanning diagnostic equipment, surgical instruments, prosthetics, and drug delivery systems. The ability to precisely mold polymers and other materials into intricate shapes and configurations has revolutionized the healthcare industry, enabling the development of safer, more effective, and patient-centric solutions.
Precision Engineering and Quality Assurance
Central to the success of medical molding is precision engineering and stringent quality assurance processes, ensuring that products meet exacting standards for performance, reliability, and safety. Manufacturers employ advanced molding techniques, such as injection molding and micro-molding, to achieve precise geometries and tolerances required for medical devices.
Furthermore, comprehensive quality control measures, including rigorous testing, inspection, and validation protocols, safeguard the integrity of medical products throughout the manufacturing process. Compliance with regulatory frameworks, such as ISO 13485 and FDA guidelines, underscores the commitment of manufacturers to uphold the highest standards of quality and patient safety.
Material Innovation and Biocompatibility
Material selection plays a pivotal role in medical molding, with manufacturers leveraging a diverse range of polymers, metals, and ceramics to meet the unique performance and biocompatibility requirements of medical devices. Biocompatible materials, such as medical-grade plastics and implantable alloys, ensure compatibility with biological systems, minimizing the risk of adverse reactions and promoting tissue integration.
Advancements in material science continue to drive innovation in medical molding, with the emergence of novel biomaterials and bioresorbable polymers expanding the possibilities for next-generation medical devices. By harnessing the unique properties of these materials, manufacturers can develop implantable devices that promote healing, reduce the need for additional surgeries, and improve patient outcomes.
Customization and Personalized Medicine
The advent of 3D printing and additive manufacturing technologies has ushered in a new era of customization and personalized medicine, offering tailored solutions that address the unique needs of individual patients. Medical molding plays a pivotal role in this paradigm shift, enabling the production of patient-specific implants, surgical guides, and prosthetics with unprecedented precision and accuracy.
By leveraging advanced imaging techniques, such as MRI and CT scans, healthcare providers can capture detailed anatomical data and collaborate with manufacturers to design customized medical devices that fit seamlessly with the patient's anatomy. This personalized approach not only improves treatment outcomes but also enhances patient satisfaction and quality of life.
Conclusion:
In conclusion, medical molding represents a nexus of innovation, engineering excellence, and healthcare advancement, driving transformative change in the medical landscape. By embracing precision engineering, material innovation, and personalized medicine, manufacturers continue to push the boundaries of what's possible, revolutionizing patient care and shaping the future of healthcare.
As we look ahead, the convergence of medical molding with emerging technologies, such as artificial intelligence and nanotechnology, holds immense promise for further enhancing medical device performance, efficiency, and accessibility. By fostering interdisciplinary collaboration and investing in research and development, we can unlock new opportunities to address unmet medical needs and improve health outcomes for patients worldwide.
GETTING A QUOTE WITH LK-MOULD IS FREE AND SIMPLE.
FIND MORE OF OUR SERVICES:
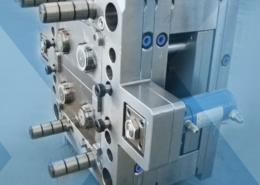
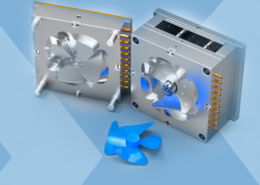
Plastic Molding
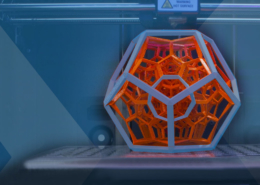
Rapid Prototyping
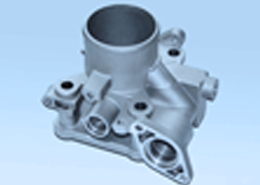
Pressure Die Casting
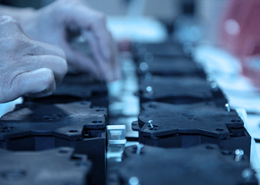
Parts Assembly
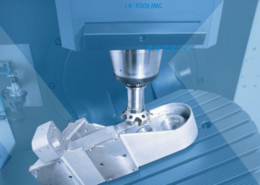