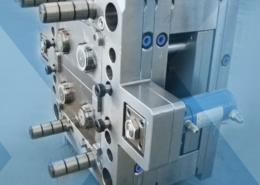
Aluminum Die Casting Design Guide
Author:gly Date: 2024-05-26
Designing for aluminum die casting involves a combination of engineering principles, material characteristics, and manufacturing considerations. Here is a guide to help you design parts for aluminum die casting effectively:
1. Understand the Die Casting Process:
Familiarize yourself with the aluminum die casting process, which involves injecting molten aluminum alloy into a steel mold (die) under high pressure.
Recognize the constraints and capabilities of die casting, such as parting lines, draft angles, and gating.
2. Part Complexity:
Consider the complexity of your part. Die casting is ideal for producing intricate, complex shapes with high accuracy.
3. Material Selection:
Choose the right aluminum alloy for your application based on factors like strength, corrosion resistance, and thermal conductivity.
Common aluminum alloys used for die casting include A380, A383, and A360.
4. Draft Angles:
Incorporate draft angles (taper) into the design. Draft angles facilitate easy ejection of the part from the mold and reduce the risk of damage.
5. Wall Thickness:
Maintain uniform wall thickness to prevent defects like porosity, shrinkage, or warping.
Avoid sharp corners, as they can lead to stress concentrations.
6. Ribs and Bosses:
Use ribs and bosses to add strength to the design where needed. These features can enhance structural integrity without significantly increasing weight.
7. Fillets and Radii:
Incorporate generous fillets and radii in corners and intersections to reduce stress concentrations and improve mold fill.
8. Undercuts and Core Pins:
Minimize undercuts or complex features that may require additional operations, such as side-core pulls or slides.
Be mindful of core pins and their placement, as they can affect part geometry.
9. Surface Finish:
Specify the desired surface finish and texture early in the design process. Die casting can achieve a range of surface finishes, from matte to highly polished.
10. Tolerances:
- Communicate tight tolerances as needed for critical dimensions, and understand that some dimensions may require additional machining after casting.
11. Gating and Runner Design:
- Work with your die caster to determine the most efficient gating and runner system to ensure even material flow and minimize defects.
12. Ejection:
- Design the part with features that allow for easy ejection from the mold. Ejector pins should be strategically placed.
13. Tooling and Tool Life:
- Be aware that the tooling (dies) used for aluminum die casting can be expensive. Design for tool life by minimizing wear and tear on the dies.
14. Wall Thickness Transition:
- Avoid abrupt transitions in wall thickness, which can cause defects. Instead, use gradual transitions when changing wall thickness.
15. Simulation and Prototyping:
- Consider using computer-aided design (CAD) software with simulation capabilities to optimize your design before production.
- Prototyping can help validate your design and identify potential issues.
16. Testing and Validation:
- Perform material and structural testing to ensure that the die-cast part meets required specifications and standards.
17. Sustainability:
- Consider recyclability and sustainability factors when designing for aluminum die casting. Aluminum is highly recyclable.
Collaboration with experienced die casting engineers and manufacturers is crucial during the design process to leverage their expertise and ensure a successful outcome. Regular communication with your chosen die casting supplier can help address specific design considerations and production requirements.
GETTING A QUOTE WITH LK-MOULD IS FREE AND SIMPLE.
FIND MORE OF OUR SERVICES:
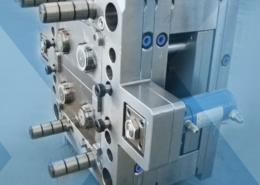
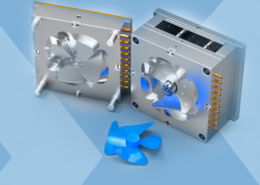
Plastic Molding
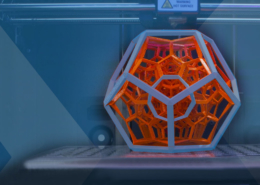
Rapid Prototyping
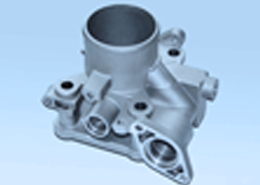
Pressure Die Casting
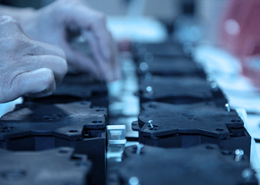
Parts Assembly
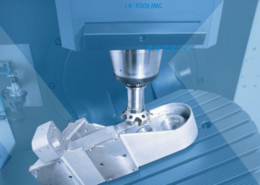