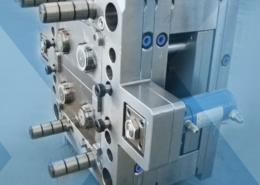
Exploring the Best Plastic for Injection Molding
Author:gly Date: 2024-06-08
In the dynamic landscape of manufacturing, the selection of the appropriate plastic for injection molding is pivotal. It not only influences the quality and durability of the final product but also significantly impacts production efficiency and cost-effectiveness. Join us on a journey as we delve into the realm of plastics and uncover the best candidates for injection molding applications.
Background Information
Injection molding stands as a cornerstone in modern manufacturing, facilitating the production of a diverse range of products across various industries. Plastics, owing to their versatility and ease of molding, reign supreme as the material of choice for this process. However, the sheer variety of plastics available poses a challenge for manufacturers, necessitating a thorough understanding of their properties and suitability for injection molding.
Material Characteristics
Durability
Durability is a non-negotiable aspect when considering plastics for injection molding. The chosen material must withstand the rigors of the molding process as well as the intended application environment. Polypropylene and acrylonitrile butadiene styrene (ABS) are renowned for their exceptional durability, making them popular choices among manufacturers.
Flexibility
Flexibility plays a crucial role in determining the applicability of a plastic for injection molding. Depending on the intricacy of the design and functional requirements of the product, materials with varying degrees of flexibility may be preferred. Thermoplastic elastomers (TPE) and polyethylene are prized for their flexibility, offering manufacturers the versatility to cater to diverse design needs.
Chemical Resistance
In certain applications, exposure to chemicals is inevitable. Therefore, it is imperative to select plastics with robust chemical resistance properties to ensure product integrity and longevity. Polyethylene terephthalate (PET) and polyvinyl chloride (PVC) stand out for their excellent chemical resistance, making them ideal candidates for applications in harsh chemical environments.
Manufacturing Considerations
Melt Flow Rate
The melt flow rate (MFR) of a plastic determines its flowability during the injection molding process. Materials with high MFR facilitate faster filling of molds, resulting in shorter cycle times and improved production efficiency. Polypropylene and polystyrene are prized for their high MFR, making them preferred choices for high-volume production.
Shrinkage
Shrinkage is a common phenomenon encountered during the cooling phase of injection molding, wherein the material contracts slightly as it solidifies. Minimizing shrinkage is critical to ensure dimensional accuracy and consistency in the final product. Polyethylene and acetal exhibit low shrinkage rates, making them well-suited for precision molding applications.
Surface Finish
The surface finish of the molded part is a reflection of the quality of the injection molding process. Certain plastics inherently lend themselves to achieving superior surface finishes, thereby reducing the need for secondary finishing operations. Polycarbonate and polypropylene boast excellent surface finish capabilities, enhancing the aesthetic appeal of the final product.
Conclusion
In conclusion, the selection of the best plastic for injection molding is a multifaceted decision that requires careful consideration of material characteristics and manufacturing requirements. By understanding the unique properties and advantages offered by different plastics, manufacturers can optimize their injection molding processes to achieve superior results in terms of product quality, efficiency, and cost-effectiveness.
Future Research Directions
Looking ahead, further research into the development of novel materials with enhanced properties and sustainability credentials holds immense promise for the field of injection molding. Additionally, advancements in material science and process optimization techniques are poised to revolutionize the way plastics are utilized in manufacturing, paving the way for unprecedented innovation and progress.
GETTING A QUOTE WITH LK-MOULD IS FREE AND SIMPLE.
FIND MORE OF OUR SERVICES:
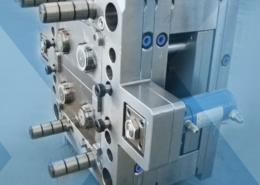
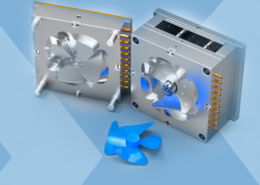
Plastic Molding
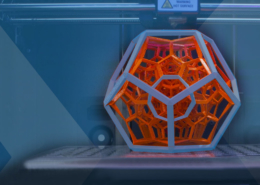
Rapid Prototyping
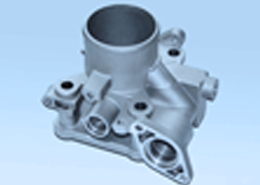
Pressure Die Casting
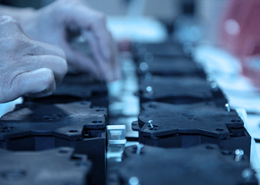
Parts Assembly
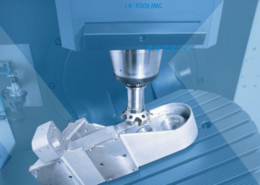