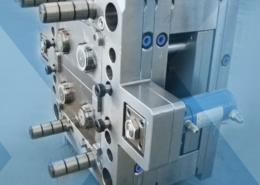
Exploring High Volume Injection Molding: Revolutionizing Manufacturing
Author:gly Date: 2024-06-08
In the realm of modern manufacturing, high volume injection molding stands as a cornerstone, revolutionizing the production of intricate parts and components across various industries. This article delves into the intricacies of high volume injection molding, unraveling its significance, applications, and technological advancements.
The Essence of High Volume Injection Molding
High volume injection molding epitomizes efficiency and precision in mass production. It involves injecting molten material, typically plastic, into a mold cavity at high pressure. Upon cooling and solidification, the mold opens to reveal the desired component, ready for assembly. This streamlined process enables the rapid fabrication of identical parts with minimal variation, making it indispensable in industries ranging from automotive to consumer electronics.
Historical Evolution
The roots of high volume injection molding trace back to the mid-20th century, coinciding with the burgeoning plastics industry. Early iterations were rudimentary, characterized by manual operation and limited material options. However, with advancements in polymer science and engineering, injection molding evolved into a sophisticated technique capable of meeting the demands of mass production.
Technological Advancements
Contemporary high volume injection molding is characterized by cutting-edge technology, epitomized by computer-controlled machinery, precise temperature and pressure control, and sophisticated mold design software. These advancements enhance repeatability, accuracy, and efficiency, paving the way for unparalleled production capabilities.
Applications Across Industries
The versatility of high volume injection molding transcends industry boundaries, finding applications in automotive, aerospace, medical, and consumer goods sectors.
Automotive Industry
In the automotive sector, high volume injection molding underpins the fabrication of intricate components such as interior panels, dashboard elements, and engine parts. Its ability to produce complex geometries with tight tolerances ensures the seamless integration of components, contributing to vehicle safety and performance.
Medical Devices
The medical industry relies on high volume injection molding for the production of precision components used in diagnostic equipment, surgical instruments, and implantable devices. The biocompatibility of medical-grade polymers ensures patient safety, while the scalability of the process facilitates cost-effective mass production.
Consumer Electronics
The proliferation of consumer electronics necessitates rapid and cost-effective manufacturing solutions, making high volume injection molding indispensable. From smartphone casings to computer peripherals, injection-molded components play a pivotal role in shaping the modern technological landscape.
Sustainability and Environmental Considerations
While high volume injection molding offers unparalleled efficiency, its environmental impact warrants attention. The proliferation of single-use plastics and energy-intensive production processes necessitates a paradigm shift towards sustainable manufacturing practices.
Material Innovation
Advancements in bio-based polymers, recyclable materials, and biodegradable additives offer promising avenues for reducing the environmental footprint of injection molding. By embracing sustainable materials, manufacturers can mitigate the ecological impact of mass production while meeting consumer demand for eco-friendly products.
Energy-Efficient Technologies
Furthermore, the adoption of energy-efficient machinery, waste reduction strategies, and closed-loop recycling systems can minimize energy consumption and material wastage associated with injection molding operations. These initiatives not only align with corporate sustainability goals but also resonate with environmentally conscious consumers.
Future Perspectives and Emerging Trends
Looking ahead, the future of high volume injection molding is poised for further innovation and optimization. Emerging trends such as 3D printing integration, micro-molding technologies, and artificial intelligence-driven process optimization promise to redefine the landscape of manufacturing.
3D Printing Integration
The convergence of high volume injection molding with 3D printing technologies holds immense potential for enhancing design flexibility, reducing lead times, and enabling on-demand production of customized components. By leveraging the strengths of both processes, manufacturers can unlock new avenues for innovation and product differentiation.
Micro-Molding Technologies
The miniaturization trend in electronics and medical devices necessitates the development of micro-molding technologies capable of producing ultra-precision components with sub-millimeter dimensions. High volume micro-molding opens new possibilities for miniaturized devices, implantable sensors, and microfluidic systems, driving advancements in healthcare, electronics, and beyond.
Conclusion
In conclusion, high volume injection molding stands as a cornerstone of modern manufacturing, enabling the efficient production of intricate components across diverse industries. From automotive to healthcare, its versatility and precision continue to drive innovation and reshape the technological landscape. As we navigate towards a sustainable future, embracing advancements in material science, energy-efficient technologies, and emerging trends will be paramount in realizing the full potential of injection molding while minimizing its environmental impact. By fostering collaboration and innovation, we can chart a path towards a more sustainable and resilient manufacturing ecosystem, ensuring a brighter future for generations to come.
GETTING A QUOTE WITH LK-MOULD IS FREE AND SIMPLE.
FIND MORE OF OUR SERVICES:
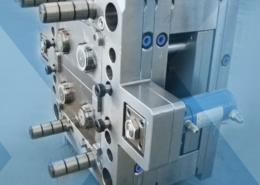
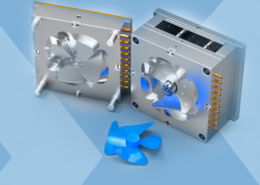
Plastic Molding
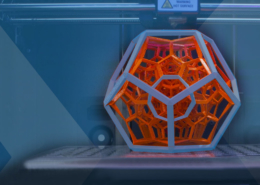
Rapid Prototyping
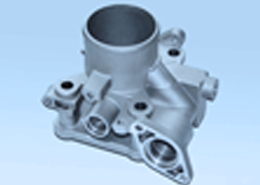
Pressure Die Casting
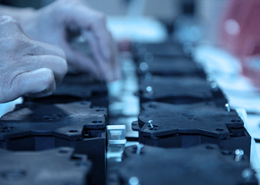
Parts Assembly
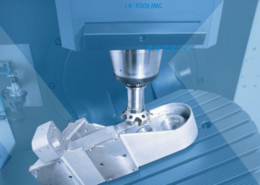