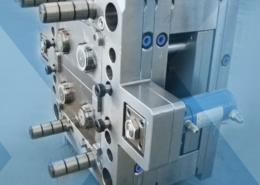
What Is LSR 2-Shot? Your Guide To Multishot LSR Molding - double shot moulding
Author:gly Date: 2024-10-15
Once the initial analysis has been performed, analyzing different geometry variations or polymers is as simple as clicking the “Duplicate Study” button to create a new SOLIDWORKS configuration and copied Plastics study.
Including the detail of the mold and cooling channels allows a molder or tool designer to simulate the cooling portion of the mold cycle using Plastics Premium.
ABS is a thermoplastic polymer widely used for injection molding. ABS is durable, budget -friendly, and is easy to machine. ABS can be used in conjunction with a metal coating since many metals will adhere strongly to the surface of ABS plastic. ABS plastic has good resistance to extreme temperature and humidity. ABS is perfect for projects that demand strength, stiffness, and impact resistance. ABS is an ideal candidate for secondary processing as it can easily be painted or glued. ABS is also very easy to recycle.
Note that for Plastics analysis the “positive” volume of the net molded part is required, rather than the negative shape of the mold cavity. If you are working from mold tooling and do not have the shape of the target part, it can easily be extracted using the Intersect feature in SOLIDWORKS.
Plastics Professional also supports multi-shot injection molding for plastic-on-plastic parts, as well as materials such as TPU and TPE for soft-touch overmolding.
SOLIDWORKS Plastics add-in allows a mold filling simulation from within SOLIDWORKS. For part designers, Plastics Standard represents a great value and will typically make moldability problems obvious with a quick “first pass” analysis.
ICOMold’s fast-turn, low-cost, high-value injection molding enhanced by joining Fathom’s manufacturing platform. Learn More
Starting with the 2020 version of SOLIDWORKS Plastics the user-interface was re-structured to match other SOLIDWORKS Simulation products more closely.
SOLIDWORKS Plastics is an add-in product for SOLIDWORKS that enables simulations for plastic injection molding and is available in three levels: ranging from Plastics Standard for predicting single part mold filling and common defects; Plastics Professional which allows analysis of the pack or “pressure hold” cycle, more complex materials and multi-cavity molds; to Plastics Premium, which enables molders and tool designers to simulate cooling channel design and predict warpage.
Geometry preparation involves making sure you are working in the SOLIDWORKS Part environment. For single parts there is no work required, but multi-cavity layouts may require conversion from assemblies into multi-body parts.
Copyright © 2024 WTWH Media LLC. All Rights Reserved. The material on this site may not be reproduced, distributed, transmitted, cached or otherwise used, except with the prior written permission of WTWH Media - Sponsored by Dassault Systèmes
The presence of “through thickness” elements also means that accurate cut plots can be created and data can be probed at any location internal to the part, which is practically a requirement for parts that feature thick wall sections.
Injection molding is an efficient manufacturing process for producing high-volume, low-cost parts. Advances in polymer technology have enabled replacement of structural metal components with injection molded fiber reinforced materials. Advances in machine automation have driven per-part cost down even further, but the mold tooling required for part production remains a significant capital expense.
ABS injection molding done at a high temperature produces resistance to heat and a smooth, gloss finish. ABS injection molding done at a lower temperature will result in better strength and impact resistance. The final properties and strength of any ABS injection molding product will be influenced by the condition parameters used during the manufacturing process. The experts at ICOMold can help customers select the correct parameters for their next ABS injection molding project.
ABS injection molding offers numerous benefits over other plastic materials. ABS plastic is easy to mold and has good machinability. It has high impact and tensile strength, dimensional stability, stiffness, and excellent stability under load. ABS can maintain its characteristics and performance in extreme temperatures but also has a low melting temperature — making it easy to use when injection molding. ABS can be alloyed with other polymers to achieve desired characteristics. ABS can also be colored for custom pieces and is easy to paint and glue, making it a good candidate for secondary processing.
A variety of part-level defects can be identified easily with Plastics Standard, which has automatic checks and visualization for short shots (incomplete fills), weld (knit) lines, sink marks and air traps in the model. Therefore, most severe molding problems can be identified and mitigated early with a quick first-pass analysis, often set up and run in just a few minutes.
Alternatively multiple geometry variations that are prepared in advance can be set up and batch solved through the Batch Manager.
ICOMold by Fathom has the expertise to help meet your ABS injection molding needs. We offer fast and dependable service, low prices, quick quotes, and an online project management system. ICOMold by Fathom can handle projects of any size – from small part or prototype runs to extended part runs in the thousands or even millions.
Mold filling simulation allows for verifying part design before mold tool steel is ever cut—ensuring that major revisions will not be necessary to either the part or the molds. Incorporating a CAD-embedded molding simulation software enables designers to make decisions to improve moldability early on and throughout the design process.
Figure 7 below shows the cooling channels, defined in this case using simple sketch lines. Flow rates and a fluid are input to the cooling channels, which will perform a fluid dynamics calculation to determine their heat removal performance.
By including the insert in the analysis, the appropriate material can be applied and more accurately represent the thermal effects in the mold.
The solid mesh generates boundary layer elements on the inner and outer skins of the model and then fills in the inside with tetrahedral elements, which allows it to calculate the flow front explicitly.
Note that all the analyses possible in Plastics Standard & Professional are predicated on a “uniform mold temperature” assumption—meaning that the mold temperature specified is assumed to be uniform throughout. This is usually a reasonable assumption for parts with uniform wall thickness but the more non-standard the part design the higher the odds that assumption is invalid.
Acrylonitrile butadiene styrene (ABS) is a rigid, lightweight plastic that is both durable and impact resistant. ABS is made up of the three monomers – acrylonitrile, butadiene, and styrene – hence the abbreviation ABS. Each of the monomers plays an important role in the composition of the final plastic. The acrylonitrile gives the final product heat and chemical resistance. The butadiene is used for impact resistance. The styrene provides extra strength and a glossy finish. ABS is used to make appliances, toys, medical supplies, musical instruments, computer parts, and more. One of the most recognizable examples of ABS injection molding is the little plastic LEGO® brick. LEGO® bricks exhibit all the qualities that makes ABS an ideal material for a wide array of projects. LEGO® bricks are tough, scratch resistant, impact resistant, and have a smooth, glossy finish.
Despite requiring many more elements, solid mesh solvers are very well multi-threaded. Despite the speed advantage shell mesh may have in terms of solve time on lower-end hardware, the gap in solve time can be reduced on hardware taking advantage of a high number of cores in the CPU and GPUs.
Running Cool/Flow/Pack/Warp provides the most rich results the software is able to offer. Warpage is predicted and contribution of thermal versus viscous effects can be evaluated.
This article will examine some of the common molding defects that can be predicted and avoided using SOLIDWORKS Plastics—as well as the setup process required to perform an analysis.
ABS plastic is recyclable. Using a combination of virgin ABS plastic mixed with recycled ABS can help customers reduce overall costs. The ABS is shredded and then purified to remove any undesirable metals or plastics during the recycling process. The leftover product is then analyzed and combined with virgin ABS to produce a new product that is ready for injection molding.
Once the cooling results are available, as visible in Figure 9 above, they will automatically be incorporated into subsequent calculations such as Flow, Pack and Warp, increasing their accuracy.
For more about the benefits of simulation, check out the whitepaper Enhancing Data Management Workflows Through CAD-Integrated Simulation.
An exaggerated warp deformation is visible in Figure 10 above. If it is not possible to correct the warp by improving the part or tooling design, the inverted shape of the warpage may be exported using the Reverse Warp option when creating a deformed body. This allows exporting a shape with “windage” with the intent of cutting the reverse-warped shape into the mold to help improve accuracy of the final part.
ABS plastic should not be used under direct sunlight or near an open flame. Fire-retardant and heat-resistant grades of ABS are available. Some ABS components can emit toxic fumes after heating.
The shell meshes only the interior and exterior faces and performs extra calculations to interpolate what the flow front is doing through the thickness of the cavity.
Overmolding, family molds and an expanded range of molding processes are available in Plastics Professional. Plastics Premium adds the ability to represent cooling system design and the mold itself, as well as performing warpage analysis.
ICOMold by Fathom is an expert at ABS injection molding and can provide customers of all sizes with a seamless manufacturing process from prototype to production.
At this point a new study can be created. For most studies, the only choice the user needs to make is Solid or Shell mesh. We will explain meshing later in detail but the short version is that a Shell mesh allows rapid analysis of relatively constant wall thickness in thin-walled parts, while Solid mesh has an increased solve time but offers more rich results with less assumptions.
For a more detailed guide on how to set up a study in SOLIDWORKS Plastics check out this video: SOLIDWORKS Plastics: Simulation Setup Guide.
Figure 5 and Figure 6 also show an example of insert overmolding, a feature which requires Plastics Professional. The ability to specify multiple different domains makes it easy to separate the runner body, the insert and the part cavity itself.
Runner systems in general can be quickly prototyped using single line sketches and assigning profiles and sizes, or they may be modeled in more detail by creating a solid body to represent the runner system and flagging it as part of the runner domain.
Cooling channels can also be modeled using solid bodies to represent more complex cooling, such as conformal cooling channels.
ABS plastic begins as a pellet. The pellet is then melted into a moldable state and injected into the cavity of a two-part mold. The plastic will solidify almost as soon as the mold has been filled. The part then cools to the shape of the mold. The mold opens once the plastic has fully cooled and the part is ejected. The mold is closed and the process starts over.
For parts that may feature thin and thick regions, or out of desire for more accuracy and rich results, it may be desirable to utilize a solid mesh.
Aside from helping avoid costly tooling challenges, having a plastics simulation tool on hand is especially helpful whenever the part design veers from normal or known, tried and true existing designs. Plastics simulation allows for design innovation, rather than playing it safe, giving engineers confidence and security that approaches that of “tried and true” designs.
In any case, running the cool analysis provides much more detail. The cool analysis can be performed up front (even before Fill or Pack) which makes for a convenient workflow if the tooling designer is simply trying to optimize cooling channels.
Modeling a solid body to represent the gate and runner is the preferred method to accurately represent localized gate effects and test different gate designs such as submarine gate, cashew gate, etc.
Figure 8 shows a cross section of the virtual mold—a volume of metal to represent the mold body. The mold could be represented as separate solid bodies and inserts for more complex scenarios.
The examples thus far have featured a shell mesh—which is appropriate for initial predictions of fill performance on thin-walled parts.
At the high end of SOLIDWORKS Plastics simulation in Plastics Premium, mold-level analysis can be performed by representing the runners, cooling channels and a mold body around the cavity.
Cooling time is estimated at this stage and part design changes can be made to reduce cooling time or minimize knit lines or sink marks.
The Injection Units settings let you specify the polymer as well as fill settings such as injection pressure, mold temperature and fill time, if known. In the absence of user-specified parameters here, Plastics will use data from the material specifications for mold temperature as well as automatically calculated values for fill time.
Figure 2 below illustrates the Plastics Study feature tree after mesh generation. The injection location was specified under boundary conditions and a sketch point was specified. The polymer was chosen inside the Injection Unit options.
The process of “runner balancing” or resizing the runners is normally a manual undertaking to attempt to even out the flow between disparate parts. SOLIDWORKS Plastics Professional automates this process using a runner balancing wizard which iterates and attempts to automatically optimize runner and gate sizes until equal fill rates are achieved.
Plastics Professional adds the ability to represent multi-cavity molds. Especially troublesome for molders are “family molds” (where multiple different parts are grouped together to save on tooling cost) which can suffer from unbalanced fill times. Observe Figure 3 below, where due to their different volumes the smaller part fills much more quickly. In the pack cycle, this may result in excessive flashing and other issues.
The last task before beginning analysis setup is to define areas for the gate or injection locations where polymer will be injected into the cavity. This is commonly defined as a simple sketch point coincident with an edge or face of the model.
Like SOLIDWORKS Simulation and Flow Simulation, the study setup is stored on the part file and can take advantage of multiple configurations for analyzing geometry variations. Results files are saved in the same folder as the CAD files by default.
GETTING A QUOTE WITH LK-MOULD IS FREE AND SIMPLE.
FIND MORE OF OUR SERVICES:
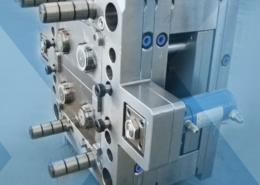
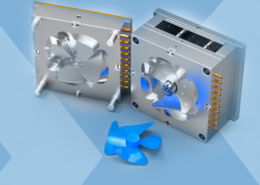
Plastic Molding
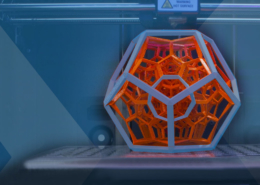
Rapid Prototyping
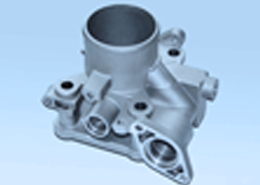
Pressure Die Casting
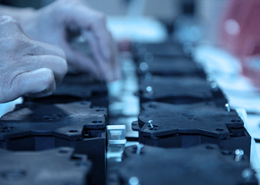
Parts Assembly
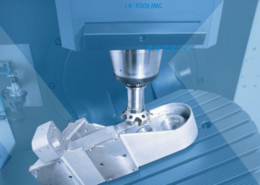