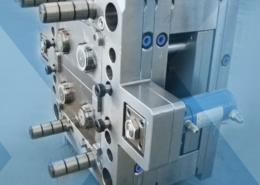
What is Overmolding? | Richfields Blog - plastic overmolding
Author:gly Date: 2024-10-15
The facility has 3,000 square feet of office space and was built to accommodate logistics operations. The company ships finished products directly to retailers, said John Berg, director of marketing for Sussex.
Koth said the company turned its experience with the bedrock from a negative into a positive. Contruction workers crushed the rock on site, which eliminated the need for trucking it out of the location. And, the company used it as the stone base under the building and parking lots.
In the automotive industry, short run injection molding plays a vital role in customizing parts for specific models. It enables manufacturers to produce limited quantities of high-quality components with precision, ensuring a perfect fit and finish. This top-tier quality is particularly valuable for luxury and exotic car manufacturers who offer high-end vehicles in limited numbers. By leveraging short run molding, they can maintain exceptional quality standards while meeting the demand for exclusivity.
By leveraging our advanced products experienced team, and commitment to excellence, we aim to make your production processes more efficient, cost-effective, and responsive to market demands. Contact us today to explore how our short run injection molding products can empower your business to create precise, high-quality parts quickly and easily.
Short run injection molding provides a game-changing solution for companies seeking efficient and cost-effective manufacturing processes for small-scale production. We have explored the numerous benefits of this innovative technique, from its ability to meet the demands of various industries to its flexibility in customization and rapid prototyping.
Officials also wanted to find a way to economically use the bedrock that was blasted away during construction. Construction workers had to deal with bedrock that was jutting out of the ground. "The entire site is on bedrock," Koth said. "We had very little soil at all, and in some places the rock was projected. With massive bedrock, you have to blast it."
The village of Sussex has a tree policy that supports the community's efforts to retain its rural character, Berg said. The trees that were cleared for the building, driveway, loading dock areas and parking lot needed to be replaced within the village at a cost up to the value of the trees removed, which was $100,000. Sussex planted 127 trees on the new lot and on the corporate headquarters and manufacturing facility lot.
As an injection molder, Sussex IM is used to handling complex parts and big projects. In some ways, building a new plant called on the same skills.
"We just don't make little widgets," Everson said. "We literally are shipping finished, packaged products. We have to lay things out differently than it was 20 years ago."
The packaging industry benefits from short run injection molding by enabling the creation of unique packaging designs for limited-edition products. It allows companies to meet specific packaging requirements for new product launches, ensuring eye-catching and functional packaging solutions. Short run molding provides the flexibility to produce a limited number of parts while keeping options open for future design changes or additions.
"We have done that, we will do that, and that is another reason we did a higher ceiling," Everson said of using mezzanines. "That is definitely a trend. It is a much more efficient way of using your space."
"We just became landlocked and couldn't expand anymore," Everson said. The original plant still is the "mother ship," he noted. It is sized at 125,000 square feet on 14 acres.
"When these trucks are coming into the facility, they divert and go to the right; any employee or visitor goes left," Koth said. "The design keeps them separated, which is important for safety."
The Sussex, Wis., company, led by CEO Keith Everson, recently completed a new, 87,000-square-foot building near its 40-year-old facility. It has prepped the 20-acre lot and structure to be able to efficiently add another 70,000 square feet.
Everson's goal was to become more efficient and also to allow for the square footage that will be needed for the fulfillment services it offers to its customers.
Short run injection molding offers cost advantages compared to larger production runs. Since fewer parts are required, less expensive mold materials such as aluminum or lower steel grades can be used, reducing tooling costs. With lower upfront costs, short run injection molding becomes accessible to a broader range of customers with smaller budgets. Additionally, adjustments and modifications can be made without significant financial commitments, and prototypes may require less finishing than in 3D printing, saving both time and cost.
Short run injection molding does not significantly restrict resin requirements due to the mold material. It allows for utilizing a wide range of resins available in higher volume molding processes. Material selection plays a critical role in determining the final product's quality, durability, and performance. Factors such as environmental conditions and specific requirements need to be considered when choosing the appropriate material. By carefully selecting the right material and considering design limitations, companies can ensure that the chosen material meets all necessary requirements while remaining cost-effective.
To accommodate expansion, the building has special features, Koth said. "We used high-efficiency insulated wall panels along the entire west wall," he said, noting that they are 30 feet tall and 3 inches thick with a 24-gauge metal skin. "That is the wall that would be part of the new expansion when that goes. That was done in order to make expansion much easier. It was cost-effective, too."
"We want to use resources in our area; we do not want to stick out like a sore thumb; we want to blend in. That's really the drive, just being a good neighbor," he said.
Short run injection molding finds application in various industries. Still, four key sectors stand out for reaping significant benefits from this manufacturing process: the automotive industry, the electronics industry, the medical device industry, and the packaging industry.
"It is expensive to frequently rearrange molding presses to accommodate the additional space needs of a new project," Berg said. "More often than not, a custom molder will lay out a new cell to fit an existing press environment because they cannot easily — physically or financially — shut down and move a number of other presses to make more room. Our new facility gives us planning options for improvement. Once we get to the point where it is so filled with manufacturing activities that we start to see capacity restraints, we can easily expand."
The site borders wetlands, which the company protected by constructing two detention ponds that prevent flooding while limiting soil erosion and storm-water runoff.
"Clearly, a manufacturer like this, when we sit down with them, we'll always want to maximize square footage on the building," said Terry Koth, director of operations with Design 2 Construct, the design and construction firm that worked with Sussex. "This plant was no different. We had no less than a half a dozen iterations to figure out how to get the best square footage."
Utilizing the right molding products is crucial to enhance the short run injection molding process. Mold sealers are commonly used to fill in the microporosity of molds, resulting in an even finish on the molded parts. Mold release agents aid in easily releasing items from the mold after the molding process is complete. Mold cleaners help maintain the cleanliness and longevity of molds, ensuring optimal performance over multiple production cycles.
Many companies struggle with finding efficient ways to produce high-quality components in small quantities. Traditional injection molding processes may not be suitable due to high tooling costs, extended lead times, and the need for large production volumes. These limitations often hinder the ability to respond quickly to market demands, leaving businesses at a disadvantage.
"We have always done cell manufacturing," Everson said. "We have always done our assembly and automation at our presses. The presses and automation seem to be getting more complex. You need more space, and that is what we were able to do with this greenfield startup that we have."
The new facility has a consistent ceiling height of 30 feet. This was important for several reasons, chief among those to accommodate an ISO Class 8 clean room for contract manufacturing and packaging products for Sussex's health-care industry clients. Sussex plans to complete construction of the clean room early next year.
The electronics industry benefits from short run injection molding through rapid prototyping and quick production of consumer electronics. This fast-paced process allows companies to test and validate product designs before committing to large-scale manufacturing. Unlike 3D prototyping, which often limit sample quantities, short run molding offers the ability to produce more samples in less time, providing greater flexibility for design iterations and improvements.
By considering these factors and leveraging the benefits of short run injection molding, companies can achieve efficient and cost-effective production for their customized components prototypes.
"We measure the current total real estate devoted to the complete manufacture of the product as 980 square feet," he said. "The additional elbow room of our new facility allows us to consider re-engineering the layout of the system based on the needs of the cell. It enables us, for example, to devote more space for in-and-out access for material handling. If we can optimize the process in any way with more layout flexibility and that means we need another 200 square feet, we can now commit the floor space."
Sussex still is trying to determine the volume of material that will be processed through the new site. The company deals with 130 to 140 grades of resin. It does not have rail access so it uses tankers and silos. The original plant houses 65 injection molding presses ranging from 25 tons to 955 tons of clamping force, with 10 presses that are capable of two-shot molding. Sussex also has one blow molding machine for making water bottles.
Short run injection molding refers to a manufacturing process that specializes in producing plastic parts in small quantities, typically ranging from a few hundred to a few thousand units. It offers a cost-effective solution for companies that require rapid prototyping, low-volume production, or customized components. In this process, a mold is created, and thermoplastic materials are injected into the mold cavity under high pressure. The mold is opened once the material cools and solidifies, and the finished part is ejected.
The ceiling height gives Sussex much more flexibility with the clean room and air systems. "When we were looking at putting a clean room in our existing facility, it just made more sense to put it into the new site versus trying to retrofit an older facility," Everson said.
The advantages and benefits of short-run injection molding are numerous. First, it allows for quick turnaround times, enabling companies to bring their products to market faster. This fast process is particularly advantageous for industries where time-to-market is crucial. Additionally, short run injection molding is a cost-effective solution, eliminating the need for expensive tooling and molds associated with larger production runs. Companies with limited budgets can benefit from this approach without compromising on quality. Furthermore, this process allows flexibility and agility in design iterations and product improvements, making it ideal for companies that value innovation and adaptability.
When considering short run injection molding solutions, several factors come into play. These include cost factors and budget considerations, design limitations, material selection, and the use of the right molding products.
Unlike many mold release brands, Stoner Molding Solutions formulates, manufactures, and distributes our own products. Check out our full line of mold releases, sealers, cleaners, rust preventatives, and lubricants. In stock products are ready to ship now!
Sussex plans to maximize the site's efficiency by running programs that are flexible in terms of how the production cells can be arranged.
"We see some new products that we are working on that have some great growth possibilities," he said. "We have to be ahead with the facilities and the growth. It's not 'build it and they will come.' "
"It's all part of our culture," he said. "We try to treat people the way we want to be treated. We try to have a nice-looking campus. If we have a bunch of trees in between us and our neighbors, it's almost as if they do not know we are here.
One of the key decsions with the new building was the ceiling height. Because it was expanded in phases, the original building has a variety of ceiling heights, from 20 to 25 feet, Everson said.
One of the current manufacturing cells that Sussex feels is suited for eventual transfer is a two-stage process to create an athletic hydration bottle assembly. In process one, Sussex uses a robotic transfer injection molding method to create a dispensing cap with molded-in soft touch grip and internal seal. An inline automation system completes assembly by installing a valve and retention ring component. Process two integrates an injection molding machine, via a six-axis robot, with an accumulator head blow molding machine. Injection molded soft touch side grips are inserted into the blow mold along with an in-mold decorating film.
Here's where short run injection molding offers a breath of fresh air. By leveraging advanced technologies and skilled expertise, short run injection molding provides a cost-effective and efficient solution for small-scale production. With reduced tooling costs, quick turnaround times, and the ability to produce quality parts in the thousands or even just a few hundred, short run injection molding empowers companies to respond swiftly to market demands, effectively manage product development, and seize opportunities.
In planning the facility, which has not yet begun molding operations, Sussex took special consideration of the environment and employee safety. For factories undertaking such a project, a greenfield expansion comes with plenty of challenges. They include site selection; dealing with local jurisdictions on items such as access; availability of skilled and unskilled labor; and local taxes and regulations. All of that should be considered before the first shovel of dirt is turned.
Officials also designed for safety on the outside of the facility. To help prevent accidents, the loading docks are located away from parking lots used by employees.
The space for the complex cells was carefully planned with automation and safety in mind. Individual press sizes involved in the manufacturing cell are a key driver to the final floor space needs. The new site will house more involved and expansive cells that integrate distinct production and value- added processes with product validation and final packaging operations. The company envisions a range of different space requirements for the cells, starting from less than 1,000 square feet to double or triple that as project requirements and budgets dictate.
The environmental considerations for the project were critical, officials said, and carefully thought-out for both the exterior and interior. The precast panels that make up 75 percent of the exterior walls have a no-thermal-break design with continuous insulation. The HVAC system is a rotational air system that is more efficient than traditional rooftop units. The company uses LED high-efficiency lighting throughout the building and double-pane, Low-E glass for energy efficiency.
"Our No. 1 priority is safety," Everson said. "I want everyone to come to work healthy and to leave healthy. We have bigger areas for guarding and more complex assemblies. We are molding the product, and it comes off the line so that it is ready to be hung on a retail shelf."
It’s frustrating to have a brilliant product idea or a new project that requires rapid prototyping or small-batch production, but not having the capability to produce the test product. The lengthy and costly tooling process associated with conventional injection molding can be a significant roadblock, hindering innovative product development and market entry. Production delays can result in missed opportunities and potential loss of customers and market share.
In the medical device industry, where stringent regulations and precision are paramount, short run injection molding accelerates the development process for medical devices. It enables cost-effective production of small-batch components, making it suitable for niche applications or specialized medical devices that require limited quantities. Short run molding ensures high quality and reliability while meeting tight timelines and maintaining compliance with regulatory standards.
GETTING A QUOTE WITH LK-MOULD IS FREE AND SIMPLE.
FIND MORE OF OUR SERVICES:
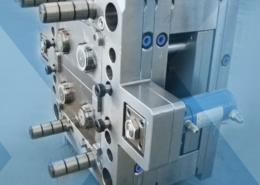
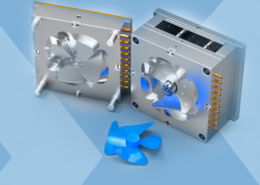
Plastic Molding
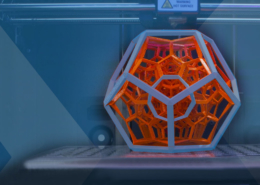
Rapid Prototyping
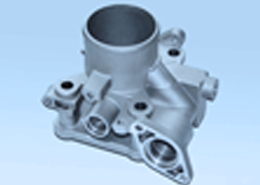
Pressure Die Casting
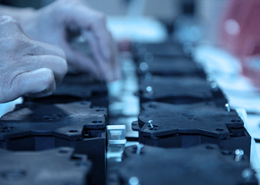
Parts Assembly
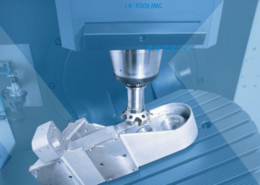