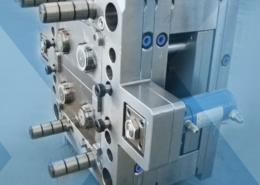
What is the Cost of Plastic Injection Molding? - custom plastic molding cost
Author:gly Date: 2024-10-15
As a thermoplastic suited for a wide variety of products, ABS is not only inexpensive but also remains strong to resist shattering or breakage. One industry in which ABS is not recommended is food applications because it is often flammable and has poor UV resistance; however, it is a great choice for electronic casing or automotive components due to its shock-resistance capabilities. One common product that is known worldwide that is created from ABS is LEGO® blocks.
Most used in consumer-packaged goods and household items, polypropylene can be used in a variety of applications from scientific lab supplies to common items like flatware or garbage cans. Since it has a low overall cost and high flexibility, polypropylene is a great plastic material choice for high-volume production runs and still provides great results for complex molds. Other common products that are made from polypropylene include water bottles and medical applications.
Choosing the right material is critical for nearly every step of the injection molding process. For this reason, it is often one of the most vital steps that a manufacturer and their client will have to make throughout the entirety of the production run. Although there is sometimes secrecy about why specific plastic material types and brands are chosen, several common plastic injection molding materials may be used due to their different qualities and functions. When considering the right material for a project, some key material properties should be considered during the planning and development process. Don’t’ forget about biodegradable material options as well.
PFA, Inc. is the perfect partner for plastic injection molders that are looking for ways to improve their processes and focus on cost-effective production runs. The enhanced processing window available when using high preload KOR-LOK Hydraulic Locking Cylinders and high-speed SMED Quick Mold Change options available with PFA’s Hydra-Jaws™ QMC systems for aluminum and steel molds, can greatly improve productivity. If you have questions, we would be happy to explain how our unique products can enhance your process and cut overall costs. To get started, please contact us and our friendly and knowledgeable staff will happily assist you.
Co-molding is also called to overmolding. It refers two plastic materials to bond, which usually are a hard material like ABS and a soft material like TPE. However, it could be two same hard materials to bond together depending on the melting temperature.
As a thermoplastic that has a high melting point and viscosity, Polyethylene is best suited for high-strength applications that require thin walls. Because of its high viscosity level, polyethylene is also suited for complex molds although setup and cooling times may be longer than other materials. PET is commonly used in applications where recycling is recommended, making it a common plastic material choice for commercial water bottles.
One of the most striking characteristics of acrylic is the ability to closely mimic glass. As you might imagine, this makes it an excellent plastic material choice for applications such as display cases or sunglasses. Since acrylic has a high hardness rating, it also retains scratch-resistant properties and is typically highly resistant to breakage. Other applications in which acrylic may be a suitable choice include medical devices, security barriers, or LCD screens.
When budget is a primary concern, polystyrene is often the most recommended plastic material; however, it is not ideal for products that require strength. For this reason, it is often used to create Petri dishes and food packaging products that are designed for single use. Unlike other materials, polystyrene also provides limited heat resistance and breaks relatively easily compared to other plastic materials that are available at a higher price.
As another thermoplastic, epoxy also offers a high level of strength while adding heat and chemical resistance after curing. Although, caution is required, as the qualities of epoxy can vary widely depending on the curing agent used. It is important for manufacturers and their clients to thoroughly understand the end requirements of a product before using epoxy materials for their products. Common applications for epoxy include transistors and electronic circuit components, as well as marine components and plugs.
One of the strongest thermoplastic materials, polycarbonate is one of the most shatter-resistant plastic materials available for use in injection molding. While commonly used for eyeglass lenses and bulletproof glass, polycarbonate will often need additional treatments to be scratch resistant. Unfortunately, polycarbonate is not resistant to repeated stress or vibration, so it is not a great fit for many aerospace or automotive components.
GETTING A QUOTE WITH LK-MOULD IS FREE AND SIMPLE.
FIND MORE OF OUR SERVICES:
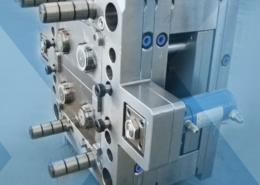
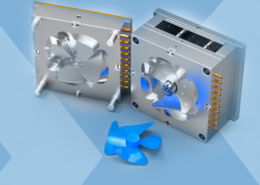
Plastic Molding
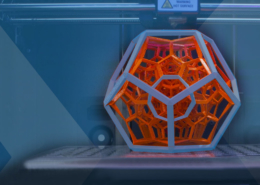
Rapid Prototyping
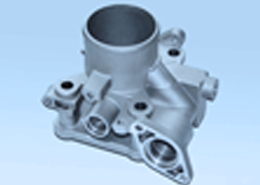
Pressure Die Casting
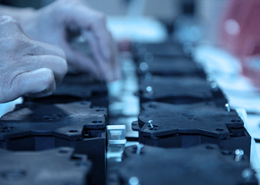
Parts Assembly
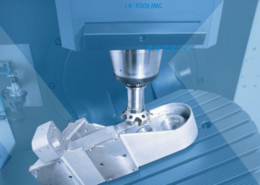