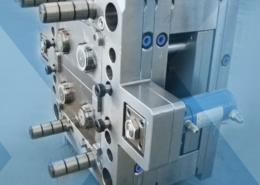
What is the Polyethylene PE material plastic injection molding ... - polyethylen
Author:gly Date: 2024-10-15
AIM Processing specializes in small part plastic injection molding. We define "small plastic parts" as roughly the size of your fingernail to the size of your hand. Injection molding is a process in which plastic resin, in pellet form, is heated and sheared until it reaches a viscous state.
Bioplastic cups are combined from different types of cornstarch or paper and lined with Ingeo™ – a Polylactic acid (PLA) made from plants.
Injection molding is a manufacturing process where molten plastic is injected into one or more cavities in a three-dimensional mold. This mold opens and closes as parts are formed and purged from the mold cavity.
It is then injected under enormous pressure into a steel or aluminum mold, cooled until it hardens, and ejected. With small part injection molding, we are able to manufacture complex, small shapes in a cost-effective, repeatable process.
Discover AIM Processing's customer small part injection molding services, designed to deliver precise, high-quality components for industries requiring intricate and complex plastic parts.
Then there are factors like the manufacturability of gate locations, draft, and ejector pins. It's enough to make your head spin.
Thermoforming is a manufacturing process to form the plastic sheet into a specific shape via mold at a pliable forming temperature. The plastic sheet or film is heated in an oven to a high-enough temperature that permits it to be stretched into or onto a mold and cooled to a finished shape. Injection molding is a manufacturing process where molten plastic is injected into one or more cavities in a three-dimensional mold. This mold opens and closes as parts are formed and purged from the mold cavity.
Thermoforming is used for smaller production quantities and is more limited in terms of what types of materials can be worked. Injection molding is normally used for large volume production runs with wide selections of plastic as base material.
As a leading small plastic parts manufacturer, we work with engineering grade plastics to create custom molded plastic parts that match the requirements for a part with properties like: chemical resistance, flexural strength, durometer, and yield strength to name a few. There are so many material options, and we can help you make the right choice for your program.
Bioplastic cutlery is made from 100% plant-based bio polymer that are different renewable starch. Or combined those plant-based with Ingeo™ – a Polylactic acid (PLA) together.
The design and manufacture of custom molded plastic parts can seem simple at first, but there are many details that must be taken into consideration depending on how the part will be used. For example, there are mechanical properties like:
Providing Bio-polymers of different forms as base material for different applications, via injection or extrusion molding.
Extrusion molding is a manufacturing process used to forming a long ‘tube like’ shape, where molten plastic is pushed through a two-dimensional die opening and and cut at equal intervals at the end stage. Injection molding is a manufacturing process where molten plastic is injected into one or more cavities in a three-dimensional mold. This mold opens and closes as parts are formed and purged from the mold cavity.
“We received the charger base and I want you all to know it looks FANTASTIC! Thank you for getting us this one for the BOD meeting.”
GETTING A QUOTE WITH LK-MOULD IS FREE AND SIMPLE.
FIND MORE OF OUR SERVICES:
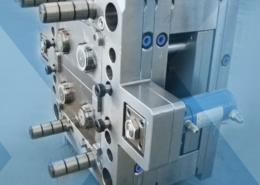
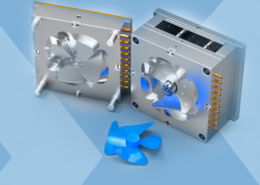
Plastic Molding
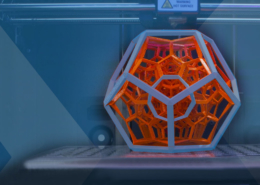
Rapid Prototyping
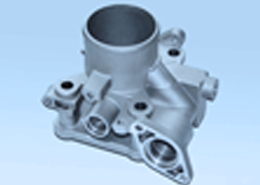
Pressure Die Casting
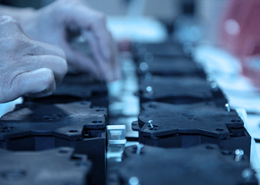
Parts Assembly
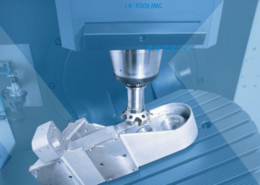