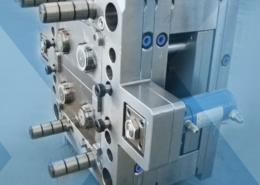
What is Thermoforming? - heat plastic to mold
Author:gly Date: 2024-10-15
Lol they don't make an injector large enough for my mold. It's 5 cavity ,I'm not even sure yet if 10 oz will shoot all 5 -16" worms
Did bass tackle sell anything bigger than a 6 oz I have a 8" fluke mold 3 cavities and a 4 oz injector right now and it fills like 1/4 of the whole mold
Ya, not just the cavity, but the sprue or runner volume to the cavity(s). Many of us have though that the 4 oz is plenty, and it may be, because our bait is 1/8 oz. But, if you have 6 baits in the mold, that is 1.5 oz and if the runner takes 4 oz you don't have enough.
10oz. should be enough to fill it. We have some 20 cavity 8" worm custom bookshelf molds & it takes around 13-14oz. to fill. Don't know the diameter of the worms your shooting but it shouldn't take much over 1/2 of what it takes to shoot 20 8" worms.
In 3D Printing, Supports for overhangs and voids are also printed with the part, as well as additional features to reduce warping and other defects. 3D printing is a lengthy process, taking at minimum several hours, and can take a few days depending upon the size and complexity of the printed object. 3D printed parts are commonly produced out of thermoplastics, but other possible materials include thermosets, impregnated plastics, ceramic powder, and metal/alloy powder.
Once the plastic has filled the mold including its sprues, runners, gates, etc., the mold is kept at a set temperature to allow uniform solidification of the material into the part shape. A holding pressure is maintained while cooling to both stop backflow into the barrel and reduce shrinking effects. At this point, more plastic granules are added to the hopper in expectation of the next cycle (or shot). When cooled, the platen opens and allows the finished part to be ejected, and the screw is drawn back once more, allowing material to enter the barrel and start the process over again.
Highly skilled machinists and toolmakers, using the product design, fabricate a tooling mold for the injection molding machine. A tooling mold (also known as simply a tool) is the heart and soul of the injection molding machine. They are carefully designed to contain the negative cavity for the product design and additional features such as sprues, runners, gates, vents, ejector systems, cooling channels, and moving components. Tooling molds are made out of specific grades of steel and aluminum that can withstand tens of thousands (and sometimes hundreds of thousands) of heating and cooling cycles, such as 6063 aluminum, P20 steel, H13 steel, and 420 stainless steel. The mold fabrication process takes upwards of 20 weeks to complete, including both fabrication and approval, making this step the most extended aspect of injection molding. It is also the most expensive part of injection molding, and once a tooling mold is fabricated, it cannot be drastically changed without incurring additional costs.
Plastic granules are fed into the hopper and into the barrel. The reciprocating screw is drawn back, allowing materials to slip into the space between the screw and the barrel. The screw then plunges forward, forcing the material into the barrel and closer to the heater bands where it melts into molten plastic. The melting temperature is kept constant as per the material specifications so that no degradation occurs in the barrel or in the mold itself.
A good pointer to keep in mind is material selection also depends on the product design, both in the application and in complexity. For example, designs calling for bendable sections/living hinges will require a strong yet flexible plastic like polypropylene. Similarly, structural parts that must be resistant to chemicals, abrasions, etc. should prioritize plastics like PEEK, Nylon, and others within these families. Â
3D printing is a separate set of processes from injection molding. With 3D printing, the material is deposited in a layer-by-layer process guided by a 3D model of the desired part. With injection molding, molten plastic is injected into a mold cavity under high pressure, creating a part all at once. Both processes are considered to be "Additive Manufacturing".
In Plastic Injection Molding, plastic injection molds come out with suitable surface quality and are essentially ready for application (with only sprues, runners, gates, and minor defects to manage). Thermoplastics are generally the preferred material used in injection molding, though newer injection molding processes can accept thermosets, impregnated materials, some metal powders, and some types of ceramics.
You can post now and register later. If you have an account, sign in now to post with your account. Note: Your post will require moderator approval before it will be visible.
The reciprocating screw forces this melted plastic through the nozzle, which is seated within a depression in the mold known as a mold sprue bushing. The moving platen pressure fits the mold and the nozzle together tightly, ensuring no plastic can escape. The melted plastic is pressurized by this process, causing it to enter all parts of the mold cavity and displacing cavity air out through the mold vents.
I just unpacked my mold. taped the spru and filled half with water but the tails were mostly empty and i was ia 5oz of water. So a solid 10 oz might work but more than likely me a little short. Ill call bass tackle tommorrow and see if they will make one a little bigger 11-12oz
Choosing the right plastic for plastic injection molding can be difficultâthere are thousands of options in the market from which to choose, many of which will not work for a given goal. Luckily, an in-depth understanding of the desired material properties and intended application will help narrow the list of potential options into something more manageable. When considering the application, it is important to keep in mind the following questions:
The Basstackle injector is a good one might look at the twin setup it will run u about 200.00 i think in the 6 oz injector . It might save u money in the long run. I have a injector 4 oz i bought the mixing block but they won't sell me the rest of the setup so i have spent about a 100.00 and will have to spend 200.00 more if i get the twin. I have ordered a twin setup off ebay it has not come in yet i will let u know how well it is made when i get it been almost a month may of blowed another 100.00 and still not have what i want. LOL Cub48
Included below is a table of the common injection molding plastics, each with its own set of advantages and general industry applications:
When I was looking for a large injector basstackle didn’t have one listed and did not respond to a couple emails asking about the 10oz availability. It’s still not on the site. I would have probably gotten one of those, but glad I got the quality injector since it’s much shorter than the basstackle and looks less awkward to handle (IMO)
no just making for me. I already made one with plunger and tip in teflon. but i could not find it when i grabbed my mold.
The content appearing on this webpage is for informational purposes only. Xometry makes no representation or warranty of any kind, be it expressed or implied, as to the accuracy, completeness, or validity of the information. Any performance parameters, geometric tolerances, specific design features, quality and types of materials, or processes should not be inferred to represent what will be delivered by third-party suppliers or manufacturers through Xometryâs network. Buyers seeking quotes for parts are responsible for defining the specific requirements for those parts. Please refer to our terms and conditions for more information.Â
After operators obtain the finished mold, it is inserted into the injection molding machine, and the mold closes, starting the injection molding cycle.
Check out Quality Injector & More. They are on Facebook and may have a website. Newer company makes all the way up to a 20oz. injector.
The components of an injection molding machine include hopper, a barrel, a reciprocating screw, heater(s), movable platen, a nozzle, a mold, and a mold cavity.
You will never get the whole amount out of an injector. At the end you will get plastic that has started to cool to much. Your best bet is see if Basstackle will sell you two of there 10oz one with a Twinjector set up. It will be big but will work well and give you plenty of Plastic. Not sure what you use to heat Plastic but it will work in a presto just fine. Both of the injectors with the same color.
Designers (engineers, mold maker businesses, etc.) create a part (in the form of a CAD file or other transferrable format), following fundamental design guidelines specific to the injection molding process. Designers should try to include the following features in their designs to help increase the success of a plastic injection mold:
When I was looking for a large injector basstackle didn’t have one listed and did not respond to a couple emails asking about the 10oz availability. It’s still not on the site. I would have probably gotten one of those, but glad I got the quality injector since it’s much shorter than the basstackle and looks less awkward to handle (IMO)
Lol they don't make an injector large enough for my mold. It's 5 cavity ,I'm not even sure yet if 10 oz will shoot all 5 -16" worms
The injection molding cycle works by this continuous processâclosing the mold, feeding/heating the plastic granules, pressurizing them into the mold, cooling them into a solid part, ejecting the part, and closing the mold again. This system allows for the rapid production of plastic parts, and upwards of 10,000 plastic parts can be made in a workday depending upon the design, size, and material.
Lots of good ones, just depends on what you want. I think I would prefer the locking style of head, but all most of them work if you are careful and use protective gloves and full length shirts, and I suggest safety glasses.
Plastic injection molding is a popular manufacturing technique in which thermoplastic pellets are converted into high volumes of complex parts. The injection molding process is suitable for a variety of plastic materials and is a vital aspect of modern lifeâphone cases, electronic housings, toys, and even automotive parts would not be possible without it. This article will break down the basics of injection molding, describe how injection molding works, and illustrate how it is different from 3D printing.
Check out Quality Injector & More. They are on Facebook and may have a website. Newer company makes all the way up to a 20oz. injector.
Xometry offers a full range of injection molding capabilities to help with your production needs. Visit our website to explore the full range of our capabilities or to request a free, no-obligation quote.
I have a 12oz from them and it’s great ( other than the o-rings), quality construction, heats up quickly and keeps the heat nicely.
I just bought a 10oz. basstackle injector last week. I have a 6 oz. & a cheaper, but smaller twin injection system too. The 10 oz. lets me shoot my brush hog, super hog & beaver style baits in one shot now. As usual the basstackle injector is great.
This article presented the basics of injection molding to explain how it works, the materials that can be used, and how the process differs from other techniques such as 3D printing. We hope this article helped readers understand this manufacturing process and how it can add immense value to manufacturing capacity, given a few key considerations.
With 3D printing, the material is deposited in a layer-by-layer process guided by a 3D model of the desired part, while with injection molding, molten plastic is injected into a mold cavity under high pressure, creating a part all at once. To learn more, see our guide on 3D Printing vs. Plastic Injection Molding.
I called them & asked specifically about the 10 ouncer & Sarah walked into the shop & said they only had two. Luckily i got one of them.She did say they weren't listed on the website & sent me a link to it.
The basics of plastic injection molding process includes creating the product design, making a tooling a mold to fit the product design, melting the plastic resin pellets, and using pressure to inject the melted pellets into the mold.
I just bought a 10oz. basstackle injector last week. I have a 6 oz. & a cheaper, but smaller twin injection system too. The 10 oz. lets me shoot my brush hog, super hog & beaver style baits in one shot now. As usual the basstackle injector is great.
I just unpacked my mold. taped the spru and filled half with water but the tails were mostly empty and i was ia 5oz of water. So a solid 10 oz might work but more than likely me a little short. Ill call bass tackle tommorrow and see if they will make one a little bigger 11-12oz
GETTING A QUOTE WITH LK-MOULD IS FREE AND SIMPLE.
FIND MORE OF OUR SERVICES:
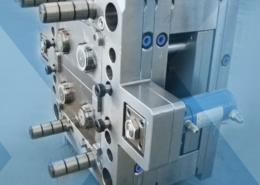
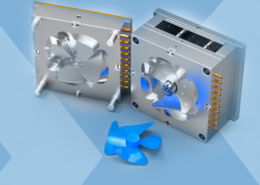
Plastic Molding
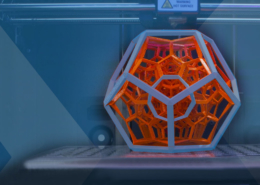
Rapid Prototyping
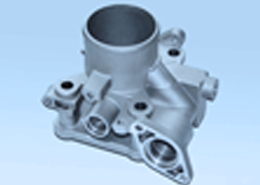
Pressure Die Casting
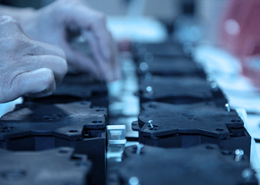
Parts Assembly
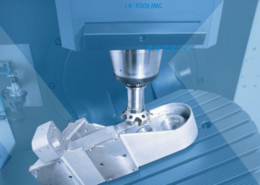