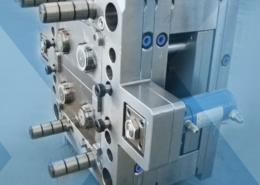
What is Tooling? And Why Is It Essential to Plastic Injection ... - tooling and
Author:gly Date: 2024-10-15
Plastic injection moulding allows for mass production at speed, with a high level of precision and at a low cost. To fully take advantage of this manufacturing process, you need to understand the jargon attached to it. Here’s a breakdown of the primary process, along with three terms central to plastic injection moulding.
Plastic injection moulding starts with feeding plastic pellets into a loader. The pellets are rotated forward by a screw in the loader so that they touch a heated barrel. This melts the plastic, which then builds up in front of the screw. Once enough plastic resin accumulates, the machine turns off the screw motor, and the screw uses pressure to push the resin through the nozzle and into a mould.
These are channels (or indented ‘pathways’) within a mould that channel either a cooling or heating medium to fill the part’s cavities. Both have their pros and cons. If heated and you maintain a consistent temperature throughout the plastic injection process, the cycle is faster which reduces waste. However, a hot runner system tends to be more costly than a cold runner system. Not only is it more cost-effective, but a cold runner system also allows for faster design changes, and it handles a wide range of resin pellets.
Channels allow the plastic to cool or remain heated through a runner system, depending on the application. A cold runner system causes the plastic to harden in the mould. After a complete cycle, the mould opens and pops out a plastic part from the machine. This process is then repeated, usually on a mass scale.
Pellets are small plastic granules that are all the same size. Resin is initially in pellet form, and these tiny pieces of plastic are used as feeder stock for plastic injection moulding machines. Once heated, the pellets melt down into a plastic resin, which is injected into the mould. Depending on what you need manufacturing, you’ll have to choose the right type of resin. This can be quite a task, as there are over 100 varieties.
As with any technical process, encountering jargon is inevitable – and plastic injection moulding is no exception. Of course, there’s a whole lot more to it than pellets, moulds, and runners. However, if you understand the basics of how plastic injection moulding works, you’ll make better decisions on what’s best for your manufacturing needs.
Usually made from stainless steel, you make a mould into the shape of the desired part. It’s hollow so plastic resin can be injected into it via a hole.
Moulds can be expensive to make, but there are cheaper ways of doing things. These include using aluminium instead of stainless steel, and having fewer cavities in the mould design. Moulds are often used for rapid prototyping or on-demand manufacturing.
GETTING A QUOTE WITH LK-MOULD IS FREE AND SIMPLE.
FIND MORE OF OUR SERVICES:
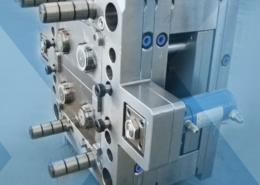
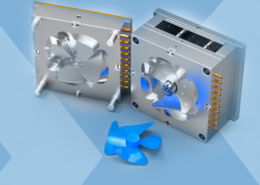
Plastic Molding
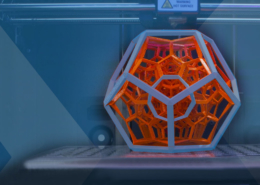
Rapid Prototyping
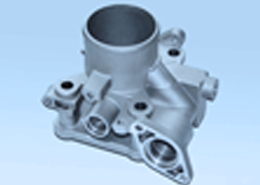
Pressure Die Casting
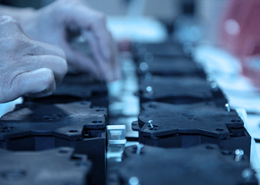
Parts Assembly
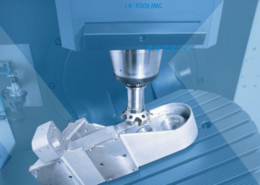