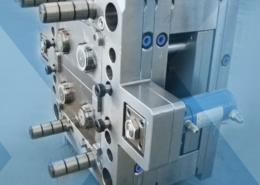
What Is Two Shot Injection Molding and When Is It Used? - shot molding
Author:gly Date: 2024-10-15
Manufacturing a multitude of identical parts with injection molding is marvelously useful. Hardened metal molds cost a lot to tool, so it is necessary to produce large quantities to make the project cost-effective.
Topworks customers benefit from flexible communication between departments as well as flexible production schedules. Two to three production shifts are available to meet the mold requirements of our customers. We have 14 sets of injection machines ranging from 80 to 1,000 tons in capacity.
Its team of injection molding experts helps the customers build a plan for success for prototyping, design validation, and production applications. With the help of production-grade steel tooling, it accepts tight tolerance and 2D drawings for all applications.
Anyone looking for a supplier offering engineering services, from initial parts analysis to final delivery, must consider linking with Precision Associates. Its engineers are experienced in proving prototypes to the clients quickly and economically while also helping them reduce costs without compromising the performance of any part.
The technology can be used to minimize the molding time for your products, to produce pre-mass quantities with real material, or to construct small quantities of finished products. Not surprisingly, molding costs of low volume production are significantly lower than those of conventional methods.
Furthermore, it may produce a more accurate result (and be less expensive) than a computer simulation. Taking shortcuts everywhere is possible, as long as the material used to construct the mold is sufficiently strong and can withstand the heat and pressure of the plastic injection. This applies to mold materials such as mild steel, aluminum, even plastic (epoxy, etc.).
Tooling costs can be reduced and production schedules shortened by strategic use of soft molds. Injection molding for low-volume parts involves less than 1,000 pieces. To the layperson, that number seems a bit high, but compared with high-volume production, it is still relatively low.
The main advantages of low volume injection molding are its speed and flexibility. LIM can shorten product lifecycles by allowing businesses to quickly construct and test prototypes. This process is also much more flexible than other manufacturing methods, as it can be easily adapted to changes in design or specifications.
The medical plastic components manufactured from the medical molding factory are resistant to vibration, harsh conditions, and force. They can also withstand tough situations without shattering, cracking, or breaking.
We are committed to going in for high-quality, cost-effective parts in a speedy way. By utilizing our expertise in rapid injection molding and efficient bridge tooling solutions, we can help you reduce your production costs to reap huge fruits while providing you with the highest quality products on time.
There are different approaches to building this vital link. One way is by partnering with low volume injection molding firms known for their expertise in short run productions, which enables them to work closely with businesses developing new products.
In order to evaluate the aesthetics and function of a newly designed product, prototype molds are needed to make samples of the new product. Tests on molded samples are more accurate than those on hand-made (machined or assembled) samples.
Natech Plastics understands the importance of quality in the design process, as poor quality can adversely impact the health and safety of the end user. That’s why it has a team working towards adding value and detailed structure to ensure all the medical equipment makes it from the design and tooling phase into full-scale production.
Fictiv is among the leading cleanroom injection molding suppliers around the globe. By using innovative ways and with the assistance of a dedicated and hard-working team, it has turned its vision into reality, working tirelessly to bring forth digital manufacturing transformation.
Since 1975, Falcon Plastics has been engaged in molding customer ideas into a wide variety of quality plastic products. It has become a mid-to-high volume custom plastic molder with the vision and capacity to manufacture, engineer, assemble, and distribute products in the leanest, most effective way.
It is also possible to mount prototypes in a mold shoe, saving even more money if prototypes are frequently needed. An edge gate might consist of sprue and a short runner or a simple sprue gate directly into the product. A manual cut will then be performed on the gate.
Since 1984, Silcotech has been a global leader in producing liquid injection molding for medical, automotive, healthcare, packaging, and electronics. It also offers turnkey, mass production, and a large volume of molding solutions.
Rapid prototyping techniques are also useful as they facilitate speedy prototype creation for testing before committing resources towards mass production
There is no official cutoff for aluminum molds, but 1,000 acts as general benchmark for when they become less cost-effective than hardened steel molds. While traditional molds require hardened steel, the initial investment is significant. Aluminum and lower-grade steel molds can be produced more quickly and for less cost.
If you’re looking to get your product to market quickly and efficiently, low volume injection molding is the way to go. By producing smaller quantities of parts, you can more easily identify any potential issues and make the necessary changes before going into full production.
Injection molding is a reliable technique for bulk producing components for the pharmaceutical and healthcare sector. Unlike other methods, it can easily handle extremely complex parts and provide uniformity to the products while maximizing their precision and quality. That’s why it is crucial for a business to partner with a company that easily fulfills all the required criteria.We hope this blog helps everyone learn more about the plastic injection molding procedure and the best firms worldwide employing this technique. Anyone who wishes to purchase medical equipment from a reliable and reputed manufacturer must contact us without a second thought.
Injection molding from Topworks is the perfect solution – we’ll take care of everything so you can focus on your business.
A vertical face should have at least 0.5 degrees of draft, although two or three degrees is better if possible. In some cases, 5 degrees of draft may be necessary. When working with thermoplastic materials, thicker walls don’t necessarily make a component stronger or more effective.
Seaskymedical is a famous injection molding manufacturer and supplier for the medical sector that also provides its customers with low-risk solutions. Its professional and all-inclusive support at all project stages includes product development, material selection, injection molding production, and mold design and manufacturing.
Low volume injection molding is a flexible and recognizable alternative to traditional, high volume injection molding. It is ideal for short runs of highly customized parts, or for prototyping new designs.
Being a rubber and plastics expert provides greater development and production efficiencies, thereby reducing development time and minimizing the overall costs. It is one of the top medical device injection molding companies in China having a team of engineering experts offering state-of-the-art design services, from prototyping to final production.
It is usually unnecessary to maintain close tolerances. Surface appearance (polishing, engraving, even flashing) won’t be an issue in general. As long as the plastic has cooled enough, the molded sample can be removed from the mold without cooling channels.
Today, rapid injection molded parts can be created in smaller quantities by using advanced manufacturing processes and technologies, as well as efficient bridge tooling solutions. Topworks strives to be more efficient in everything we do.
Founded in 1980 as a plastics engineering consulting firm, TESco Associates is another famous medical plastic injection molding company. Since its founding, the firm has put tremendous effort into researching and developing medical device molding, with special emphasis on bioabsorbable materials devices and their development.
It is also effortless for entrepreneurs who are looking to start a business in an emerging market. Another way to connect to an emerging market is to use a 3D printer. This type of printer can be used to create prototypes or small batches of products. It is also possible to use crowdfunding platforms to raise money for a business venture in an emerging market.
With our low volume injection molding manufacturing dominance, you can intend to build your plastic parts in cost-conscious manner.
By starting production soon, manufacturers can accelerate their time-to-market significantly, thereby reducing their time to see a return on investment.
We chooses the most feasible and economically advantageous tool steel and structure based on the customer’s design or sample. A manufacturing method that Topworks finds suitable to meet the needs of its customers is also chosen.
Furthermore, to meet the medical sector’s diverse challenges and stringent needs today, it employs ISO 8 cleanroom and 10 cutting-edge machines from Japan and Germany. The technology of medical overmolding, insert molding, micro molding and clean room injection molding is well-known in the medical industry.
Overall, low volume injection molding is an efficient and versatile manufacturing process that can be used to create high-quality parts in a shorter timeframe.
Additionally, ejector mechanisms are not always necessary. There may be no need for more sophisticated ejector pins than one or two air jets directed at the edge of the product at the parting line. For example, loose inserts in the mold can be used to produce threads in the product, which are then ejected with the finished product and unscrewed by hand.
Established in 1956, Rodon Group is a celebrated turnkey, innovative manufacturing solutions provider, including mold design, mold building, and high-volume parts. With over 125 plastic injection molding presses, it is among the largest family-owned and operated molders in the United States. It serves a diverse group of industries, including consumer products, windows and doors, medical and pharmaceutical, construction, and food and beverage.
The Topworks team analyzes the product design for manufacturing feasibility and offers recommendations on how to develop a product that can be produced in low-volume injection molding. Material selection also plays a crucial role in the development process.
Today, it strives to offer efficient and sustainable custom plastic molding solutions while offering comprehensive value in a competitive market. The firm is among the best medical molding suppliers across China that have created an environmentally responsible workplace for their employees and customers.
By employing advanced technology to the production challenges, this medical injection molding company reduces the risk to each customer. For the past 10 years, it has been engaged in precision mold making and injection molding. It inherits more than 11 years of experience in project and supply chain management.
Prototyping is a critical step in ensuring that products meet customer expectations before mass production making it an essential part of product development for businesses. By creating a strong connection between prototyping and mass production companies can save time and money.
Walls should remain between 0.040 and 0.140 inches (1 to 3.5 millimeters) thick across the part’s entirety to reduce the likelihood of warping or sinking of the part during cooling. Forgoing unnecessary surface finishes on molds can also reduce tooling costs and lead time.
Low volume injection molding (LIM) is a process that allows manufacturers to acquire small quantities of parts quickly and efficiently.
Customers can choose between 3D printing or CNC machining for the creation of prototypes. To avoid later tool modification and higher costs, this is done before any injection tools are built.
A draft is a design feature that makes ejection from the mold easier. A rectangular pan would make removing a cake difficult if it were truly rectangular. Cakes can easily be removed from the pan due to its rounded edges and tapered sides. Similarly, injection-molded parts can be removed from their molds.
The molding process also enhances the strength and durability of products if they are produced by reliable medical molding manufacturers.
Businesses must pay close attention to cost reduction measures in any project undertaking, including injection molding where low minimums can lower expenses considerably by reducing cavities or lowering order quantities. The notion that larger purchases equal lower prices per item is something we’ve all heard before – but this concept isn’t universally applicable across all products or industries.
Based in Ontario, Canada, the company equips trained and specialized technicians, serving the global customer base for all their design, tool-making, and manufacturing molding needs. From straightforward projects to those with complex needs, its goal is to offer value to the customers.
Precision Associates is a leading manufacturer and supplier of high-quality, custom rubber seals and other products for a variety of markets. Today, it is a reputed and reliable medical molding manufacturer, leveraging its mold design and production expertise to enhance its capabilities.
We offer injection molding low-volume manufacturing services, providing our clients with the ability to manufacture hundreds of plastic parts so that their products can be brought to market.
They make it possible to develop prototypes and produce viable parts without committing to large minimum orders while improving part design and manufacturing as needed.
Today, people know it as “the vendor of choice” for contract research and development and contract manufacturing of bioabsorbable devices. Anyone looking for an absorbable medical device manufacturer offering a significant cost-effective approach to their client’s project can turn to TESco Associates without a second thought.
One must partner with an experienced medical or pharmaceutical component manufacturer that emphasizes quality and provides its users part with traceability from start to finish.
We encourage you to contact our team once you are ready to begin your next project and upload your 3D CAD files for a free quote.
Employing the injection molding process helps curtail the timeline of product development, causing minimal scope of errors in final plastic medical products.
“I’m glad to inform you that all plastic parts are perfect!!! We are delighted, and therefore there are good chances to continue our relationship for any coming new project.”
Since 1982, Currier has followed the path of setting a new standard for service and quality in the molding industry. It offers innovative custom bucket mould solutions to help businesses succeed in manufacturing. Even today, the company continues to follow the legacy of its founder by emphasizing quality technology, automation, time-competitive business practices, and strong relationships with customers.
Minnesota Rubber & Plastics is a global leader in the manufacturing and supplying custom molded elastomeric and thermoplastic components and assemblies. Anyone looking for a firm that can produce tough parts and offer a commitment to quality, product performance, and service support can turn to it without a second thought.
Additionally, low volume injection molding allows for more flexibility in design, as you can easily make changes to the mold during the production process. This means that you can iterate on your design until it’s perfect, without incurring huge costs or delays.
Plastic medical injection molding is the best way to optimize cost through bulk manufacturing, using more compact and cost-efficient methods. It helps both the buyer and the manufacturer in saving significant costs throughout the production process.
Seaskymedical is one such firm specializing in full-service, turnkey plastic component molding providers. Its comprehensive manufacturing capabilities allow customers to maintain oversight over the production, thus resulting in greater transparency and accountability.
For low-volume injection molding, softer aluminum inserts are more welcome to hardened steel molds, since they are usually easier to make and cheaper. Hardened steel molds are obviously more durable, but when producing low volume parts, these molds do not need to be.
They can help streamline the design process by providing advice on part geometry, material selection, and mold construction.
Plastic injection molding is an efficient and cost-effective way of manufacturing pharmaceutical and medical components to high precision, accuracy, and quality levels. It is used to produce parts, from medical devices and equipment to lab tools and testing instruments.
By cooperating with more than 10 raw material companies, Seaskymedical holds a COC factory certificate. One can also find their ISO10993 biocompatibility report through a special request. In addition, their dust-free manufacturing practices help reduce the environmental impact on items, thus improving their quality.
Once the molded piece is cool, it can be machined with rounds or simple openings. This is merely a sample of the mold features that can be eliminated to simplify stacks and to lower the cost of prototype molds.
Depending on the manufacturing method, low-volume injection molded products can be production-quality parts in smaller quantities, usually less than 1,000 unique pieces.
With a background in the design and application of injection molding, the engineer of medical plastic injection molding producer works closely with clients to bring their medical designs to life.
Its engineers’ dedication and commitment to product quality and deadline sensitivity are the one motto driving this medical molding factory and keeping its customers returning.
In addition, there is a 2000 square meter warehouse where the production molds are kept on solid shelves. Tooling maintenance is conducted regularly to keep production running smoothly.
Medical and pharmaceutical equipment plays a central role in ensuring the health and safety of the patients. That’s why one must partner with a medical molding supplier with experience in component manufacturing that emphasizes quality and offers complete part traceability.
Seasky Medical serves you with medical injection molding solutions from design to tooling to material selection and manufacturing. Contact our specialized team and solve your problem now.
Medical injection molding products play an essential role in the healthcare sector in maintaining the safety of patients. That’s why it is crucial to ensure the quality of each product and its individual components throughout the manufacturing procedure – from design to final inspection.
In designing parts for manufacturability at low volumes, there are a few things to keep in mind, such as general part complexity, draft, wall thickness, and surface finish. When working with aluminum, you do not want to build in lifters or side actions common to complex builds.
Even a minor glitch in medical equipment manufacturing can cost a million lives. That’s why it is essential to turn to a reliable medical injection molding company. Such a firm should also provide quality, exceptional accuracy, and precision to the users.
“Steven is a very detail-oriented project manager and engineer who can solve problems creatively and also provides excellent service. It was a pleasure working with him.”
Topworks can provide resin material model and type options that describe the physical properties of the different options if the customer does not know what resin type to use for the product. Topworks will need to know the product function and the range of uses of the product, along with other specifications such as UV proofing or flame class requirements. This will enable them to make an appropriate recommendation.
It’s a popular approach for many products, since it enables a rapid product development cycle, offers a fast route from early prototypes to mass production, as well as reducing tooling and material investment.
There are a number of ways to connect emerging markets quickly. One is to use a low volume injection molding . This type of injection molding is designed for small businesses that want to produce a limited number of products.
From design and prototyping to post-production and fulfillment, we are committed to working directly with our customers to deliver high-quality, affordable parts in a speedy manner. Let us help you make your dream a reality.
The low volume injection molding or Rapid Manufacturing method applies to many indispensable industries that make plastic parts by injection molding.
Injection molding simplifies the process of creating high volumes of identical parts with consistent and fundamental characteristics and quality. The part is ejected quickly from the mold after cooling. The press closes after the component is ejected, repeating the process. Plastic injection molding is used to manufacture everyday products. Since injection-molded parts are expensive to manufacture, they were traditionally made in large quantities. Over time, hardened steel molds recoup investment and lower cost-per-part as they are durable and can be tool for weeks or months. As markets change, manufacturers are adapting their operations so they can exploit new, more efficient methods as markets evolve – as evidenced by the shift toward custom and small batch products. This is where low-volume injection molding comes into play.
Currier delivers its customers the two key elements of outstanding capabilities in everything they do: velocity and value.
The company understands that quality cannot be compromised in the medical industry as it significantly affects medical safety. It follows ISO 13485:2016 quality management system and is certified by a third party. Anyone looking for a professional cleanroom manufacturer using stringent inspection and supplying certified raw materials must buy from Seaskymedical.
The injection molding process can be further streamlined by working with a low volume injection molding specialist. Low volume injection molding specialists are experts in designing and manufacturing molds for small production runs.
If you don’t need a very smooth surface on the part, then there’s no need to hand-polish the mold cavity with diamond buffs. Lowering production costs and improving production times can be achieved using the most cost-efficient finish for a given part.
They also have the experience and knowledge to help engineers optimize their designs for injection molding. Low volume injection molding specialists can produce prototypes in as little as 3 weeks. However, large production runs can take up to 2 months to complete.
Injection molding uses various materials, such as silicone, polycarbonate, polyethylene, and polypropylene, to produce medical devices. Medical-grade plastics are made of light-volume material, ensuring biocompatibility, ease of handling, sturdiness, and quality.
Perhaps our prototyping services would be of benefit to you if you only need a few parts or prototypes. Throughout the prototyping and production process, we at Topworks are by your side.
The injection molding technique is extensively used in medical device manufacturing to realize the envisioned product design. It offers a range of customization and an array of undercuts to serve an extensive customer base, including medical knobs, component design, medical device housing and casings, enclosure design, and wearable healthcare technology.
There are many merits to low volume injection molding, but one of the most important is that it can help prevent hidden weakness. By producing smaller quantities of parts, you can more easily identify any potential issues and make corrections before they become costly problems.
Low volume injection molding has a number of vital advantages over traditional high volume injection molding. First, it is much more flexible, allowing for shorter runs of highly customized parts. Second, it is perfect for prototyping new designs. Third, low volume injection molding generally requires less upfront investment than high volume injection molding.
When such operations wear down the tool – soft aluminum cannot withstand such pressure – low-hardness steels like P20 are the best replacement material.
Seasky Medical serves you with medical injection molding solutions from design to tooling to material selection and manufacturing. Contact our specialized team and solve your problem now.
Besides, Seaskymedical applies automated equipment such as robotic arms to reduce personal connection. It also conducts daily disinfection of the cleanroom and tests the cleanliness twice daily.
GETTING A QUOTE WITH LK-MOULD IS FREE AND SIMPLE.
FIND MORE OF OUR SERVICES:
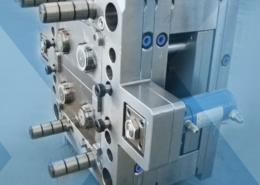
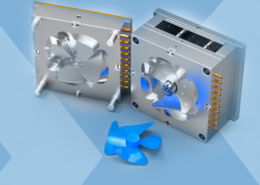
Plastic Molding
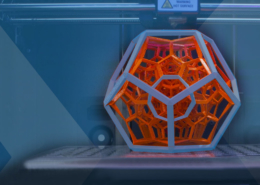
Rapid Prototyping
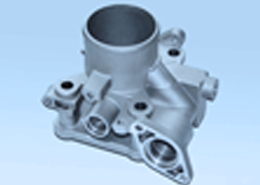
Pressure Die Casting
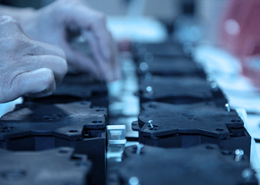
Parts Assembly
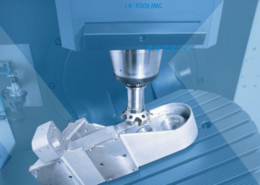