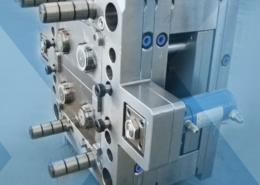
What Products Are Made from Injection Molding - Ace-Mold. - products made by inj
Author:gly Date: 2024-10-15
This article examines the importance of injection molding tolerances and their relationship to tolerance stack-ups. It also explains how part tolerances are specified and describes the factors that affect them. In addition, there’s a section for designers with frequently asked questions (FAQs).
Precision machining adds costs, so it’s essential to consider not only which tolerances are achievable, but also which ones are essential to your part design.
By signing up, you agree to our Terms of Use and Privacy Policy. We may use the info you submit to contact you and use data from third parties to personalize your experience.
By signing up, you agree to our Terms of Use and Privacy Policy. We may use the info you submit to contact you and use data from third parties to personalize your experience.
Our trained employees ensure your parts will be delivered on time and to spec.
T1 samples also provide an opportunity to check your drawing dimensions, especially critical dimensions for medical injection molding. Fictiv can deliver T1 samples (even for low-volume injection molding) in less than 14 days.
Following standard DFM principles is the best way to ensure that parts stay within defined tolerance parameters. Fictiv recommends referring to this free downloadable resource.
Injection pressure, holding time, material density, and mold temperature all have a significant effect on a part’s overall shrinkage. By maintaining these parameters, an injection molder can ensure that parts have repeatable and predictable shrinkage.
By signing up, you agree to our Terms of Use and Privacy Policy. We may use the info you submit to contact you and use data from third parties to personalize your experience.
Combining extensive plastics and engineering know-how with the highest levels of expertise in technical injection molding processes, we offer customised solutions through our comprehensive portfolio of high-performance polymers and complementary, value-adding processing methods
By signing up, you agree to our Terms of Use and Privacy Policy. We may use the info you submit to contact you and use data from third parties to personalize your experience.
By signing up, you agree to our Terms of Use and Privacy Policy. We may use the info you submit to contact you and use data from third parties to personalize your experience.
Different injection molding materials shrink at different rates. Materials from different batches and suppliers can also have different shrinkage rates. Because long, fiber-reinforced polymers shrink less in the direction of the melt flow, expect asymmetrical shrinkage with these materials.
We are your partner for the development of your individual injection molding solutions and the production of high precision plastic injection molded parts for demanding applications in a wide range of industries such as medical, automotive, aerospace and many more.
For complex parts, one of the best ways to determine shrinkage is with a mold flow analysis. This software simulation shows how a plastic resin will fill an injection mold. A mold flow analysis can also help designers identify hard-to-fill mold locations.
This equation describes linear shrinkage for materials with asymmetric properties like long, fiber-filled resins. The calculated value represents decreased shrinkage in the melt flow direction, which can result in overestimating the shrinkage in a part’s transverse direction.
Commercial tolerances are less precise but less expensive to achieve. Fine tolerances are more precise but more expensive to achieve. Remember there isn’t just one type of dimensional tolerance you may need to specify on your part drawing.
There’s plenty to consider when it comes to injection molding tolerances. The list below contains some frequently asked questions.
By signing up, you agree to our Terms of Use and Privacy Policy. We may use the info you submit to contact you and use data from third parties to personalize your experience.
Table 4 below lists the shrinkage range (percentage) of some typical injection molding resins. Note that these values are a general range. For best results, refer to the datasheet for the injection molding material that you plan to use.
The dimensions measured across a parting line cannot be held to the same degree of precision as a feature that’s not bisected. If this is a factor in your part design, it’s essential to account for this mismatch.
Part tolerances are a function of mold tolerances. Yet mold tolerances must account for the desired feature sizes and the injection molding material.
T1 tests are the first part samples produced from the tool that will be used during production. These samples, which require your review and approval, demonstrate an injection mold’s ability to produce end-use parts.
We exist to eliminate bottlenecks in new product development by integrating the people, processes, and platform you need to source custom parts.
Out-of-tolerance molds result in out-of-tolerance parts. That’s why during the CNC machining of tools, mold makers must control tool dimensions. Typically, injection molds are machined to tolerances of ±0.127 mm. However, tight tolerances may require molds machined to ±0.0508 mm, while very tight molds are machined to ± 0.0254 mm.
For flat parts like the plastic base for a medical device, you may need to specify a general tolerance and a flatness callout instead.
Tables 1, 2, and 3 below contain commercial and fine tolerances for common injection molding materials and specialty plastics and polymer blends. If you’re unfamiliar with the acronyms for these materials, the list below explains what they mean.
Even with the best injection molding equipment, process repeatability varies. A skilled molder can calculate shrinkage rates for various plastics, but your design decisions affect part shrinkage and, ultimately, which tolerances are achievable. If an injection molding material has a higher shrink rate, tolerances are harder to control.
By signing up, you agree to our Terms of Use and Privacy Policy. We may use the info you submit to contact you and use data from third parties to personalize your experience.
Injection molding tolerances are acceptable variations in size for part features and overall dimensions. They are expressed as plus or minus (±) values in millimeters or inches and vary by the type of material that’s used and the overall size of the part.
By signing up, you agree to our Terms of Use and Privacy Policy. We may use the info you submit to contact you and use data from third parties to personalize your experience.
There isn’t just one kind of tolerance for an injection molded part. Rather, there are tolerances for specific part features. Here are some of the most common.
We exist to eliminate bottlenecks in new product development by integrating the people, processes, and platform you need to source custom parts.
Part designers add tolerances to CAD files to tell an injection molder the amount of variation that’s allowed. In turn, injection molders use tolerances during design for manufacturability (DFM) reviews and to make tooling and processing decisions.
Fictiv makes it easy for part designers to get a quote in about 24 hours. Plus, every part that you upload to our platform is reviewed by experts and receives next-day DFM feedback. Fictiv’s manufacturing partners can support tight tolerances, and you’ll have real-time visibility of your injection molding project.
Injection molded parts shrink as they cool. Because shrinking affects part tolerances, you’ll need to compensate for these dimensional changes. Practically speaking, this means designing the part to its nominal dimensions and then scaling up the injection mold by the expected shrinkage.
Consider the example of three injection molded parts that are bolted together. Each part has a hole with tolerances within the dimensions you specify. That’s great, but all three holes still need to align so that a fastener can pass through them.
Shrinkage is determined by testing a material’s linear shrinkage rate according to a standard such as ASTM D955. First, a sample is injection molded and allowed to cool over a period of time. Then the shrinkage is calculated according to this equation.
Create high quality custom mechanicals with precision and accuracy.
For injection molded parts of any size, maintaining a uniform wall thickness helps prevent uneven shrinkage. When a part’s wall sizes are non-uniform, the walls cool and shrink at different rates, which increases the risk of warping.
Designers also need to consider that semi-crystalline resins have higher injection molding shrinkage rates than amorphous resins. The mold shrinkage chart in Figure 1 below illustrates this.
Injection molding tolerances aren’t just about part features. They can be divided into commercial and fine tolerances depending on the amount of precision that you need.
Many injection molded parts are used in larger assemblies. A tolerance stack-up refers to how all assembled parts must fit together. Because each component has its own tolerances, designers need to account for the cumulative effect of dimensional deviations.
Access a wide breadth of capabilities through our highly vetted network.
For all your injection molding needs, Fictiv has you covered. Our injection molding experts are well-versed in managing shrinkage and maintaining tight tolerances. We can produce complex parts at amazing speeds and help you simplify sourcing with streamlined workflows.
By signing up, you agree to our Terms of Use and Privacy Policy. We may use the info you submit to contact you and use data from third parties to personalize your experience.
The image below shows the shrinkage variation of an injection molded part. It’s from a simulation within Autodesk Moldflow, a commonly used software application for computer-aided engineering (CAE).
Because larger injection molded parts experience more shrinkage, their dimensions are harder to control. Therefore, it’s harder to hold tighter tolerances for them in terms of overall part size and specific part features.
With assemblies of injection molded components, remember to consider how all parts fit together. This tolerance analysis, or tolerance stack up, must account for any interference, such as from a fastener head while providing adequate clearance.
Injection molding supports the use of many different materials, some of which are strengthened or modified with additives such as glass fillers and UV stabilizers. This broad material selection is attractive, but different plastics have different shrinkage rates. Moreover, these rates differ not just with the size of the overall part, but also with the inclusion of additives.
To maintain part tolerances, injection molds must provide consistent, repeatable heating and cooling. Mold makers need to place cooling channels with care and provide additional cooling for multi-cavity molds. When mold cavities are made from steel, such as with the tooling that Fictiv offers, the baseline for shrinkage calculations is more stable.
Accelerate development with instant quotes, expert DFM, and automated production updates.
For non-critical applications like consumer products, injection molding tolerances are typically ±0.1 mm. For applications that require tighter tolerances, such as injection molded medical parts, ±0.025 mm is typical instead.
As a rule, parts with tighter tolerances are more expensive because they have stricter tooling and processing requirements. Mold quality is critical, as are proper cavity fill rates and consistent cooling temperatures.
The Society of the Plastics Industry (SPI), a U.S.-based trade association now known as the Plastics Industry Association (PIA, or PLASTICS), defines typical tolerances. Because these are typical values, it’s essential to discuss them with your mold manufacturer.
GETTING A QUOTE WITH LK-MOULD IS FREE AND SIMPLE.
FIND MORE OF OUR SERVICES:
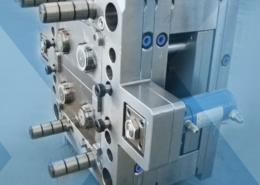
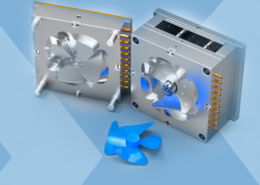
Plastic Molding
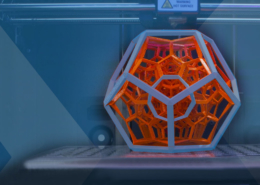
Rapid Prototyping
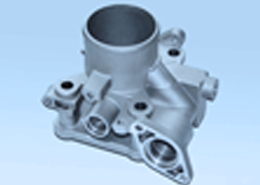
Pressure Die Casting
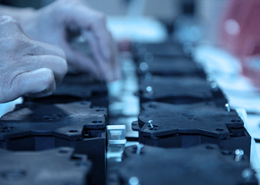
Parts Assembly
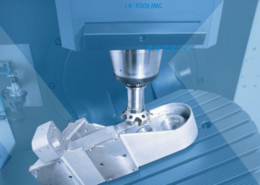