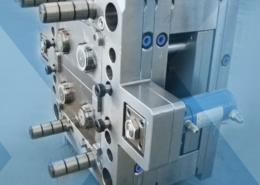
WHY OVERMOLDED A METAL PART ? - Delmon Group - overmolding metal with plastic
Author:gly Date: 2024-10-15
Rotational molding is commonly used to make large hollow plastic products like bulk containers, storage tanks, car parts, marine buoys, pet houses, recycling bins, road cones, kayak hulls, and playground slides. [4]
While other forms of molding use extrusion to get the plastic resins into a mold, this process extrudes the melted plastic directly into a die. The die shape, not a mold, determines the shape of the final product.
Injection molding is commonly used for making very high volume custom plastic parts. Large injection molding machines can mold car parts. Smaller machines can produce very precise plastic parts for surgical applications. In addition, there are many types of plastic resins and additives that can be used in the injection molding process, increasing its flexibility for designers and engineers.
When molding plastics, a powder or liquid polymer such as polyethylene or polypropylene is placed into a hollow mold so the polymer can take its shape. Depending on the type of process used, various ranges of heat and pressure are used to create an end product.
Rotational Molding, also called rotomolding, is a manufacturing process for producing large hollow parts and products by placing a powder or liquid resin into a metal mold and rotating it in an oven until the resin coats the inside of the mold. The constant rotation of the mold creates centrifugal force forming even-walled products. Once the mold cools, the hardened plastic is removed from the mold.
Thermoforming is a manufacturing process where a plastic sheet called thermoplastic is heated to a pliable forming temperature, formed to a specific shape in a mold, and trimmed to create a usable product. [11] Thermoplastic comes in a wide variety of materials, colors, finishes, and thickness.
Modern rotational molding also has a rich history beginning in 1855 when rotation and heat were used to produce metal artillery shells in Britain.
In 1946, the screw injection molding machine was invented by James Hendry, which replaced the plunger injection technique. This is the technique most commonly used today.[2]
Blow molding is a method of making hollow, thin-walled, custom plastic parts. It is primarily used for making products with a uniform wall thickness and where the shape is important. The process is based upon the same principle as glass blowing.[6]
This guide will explain the different kinds of molding processes available today to help you discover the ideal process for your product. *Disclaimer: Even though Fibertech exclusively offers rotational molding, we’ve gone to great lengths to make sure this guide accurately helps you choose the best form of molding for your product. Sometimes, the best choice is rotational molding… other times, it’s another kind of molding. Our goal with this guide is to be as objective as possible while pointing you in the best direction to get your part or product made with the ideal method. If you have questions or comments about this guide, feel free to contact us.
The best use of compression molding is the replacement of metal parts with plastic parts. It is mostly used for small parts and products in very high volume. The automotive industry uses compression molding heavily because the final products are very strong and durable.
Blow molding processes generate, in most cases, bottles, plastic drums, and fuel tanks. If you need a hundred thousand plastic bottles, this is the process for you. Blow molding is fast and economical with the mold itself costing less than an injection molding, but more than rotational molding[8] … sometimes as high as 6 to 7 times as much as a roto-molding tool. [9]
The initial cost of a compression mold is substantial, depending on several factors including the number of cavities, the size of the parts, the complexity of the pieces, and the surface finish among other things. But the cost of each individual part is low at high quantities, so large quantities of parts are ideal for this form of molding. [10]
Extrusion molding is similar to injection molding except that a long continuous shape is produced. Another difference in extrusion molding is that the process uses a “die” not a “mold.”
Molding, also sometimes spelled moulding, is the process of manufacturing by shaping liquid or pliable material using a rigid frame called a mold or matrix. [1]
Very little material is wasted during the process, and excess material is often re-used, making it economical and environmentally friendly.
The cost of extrusion molding is relatively low compared to other molding processes because of the simplicity of the die and the machines themselves.
The mold itself can be highly intricate to facilitate the molding of a wide range of products. Molds can include inserts, curves, and contours as well as logos and slots for plastic or metal inserts to be placed after a product is molded.
Blow molding machines heat up plastic and inject air blowing up the hot plastic like a balloon. The plastic is blown into a mold and as it expands, it presses against the walls of the mold taking its shape. After the plastic “balloon” fills the mold, it is cooled and hardened, and the part is ejected. The whole process takes less than two minutes so an average 12 hour day can produce around 1440 pieces.[7]
Compression molding is done exactly like the name suggests. A heated plastic material is placed into a heated mold and then pressed into a specific shape. Usually, the plastic comes in sheets, but can also be in bulk. Once the plastic is compressed into the right shape, the heating process ensures that the plastic retains maximum strength. The final steps in this process involve cooling, trimming, and then removing the plastic part from the mold.
Thermoforming uses several different types of molds and processes in order to achieve the final product. To create 3D products, the mold is typically a single 3D form made out of aluminum. Because thermoforming uses low pressures, molds can be produced for a low cost using inexpensive materials.
Is it large or small? Should it be flexible or stiff? Is it round, square, or some weird shape? Do you already have a mold, or do you need to have one made?
Extruded parts are made by squeezing hot raw material through a custom die. A simplistic visualization would be like squeezing Play Doh through a shaped hole.
Parts made from extrusion have a fixed cross-sectional profile. Examples of extruded products include PVC piping, straws, and hoses. The parts do not need to be round but they need to have the same shape along the length of the part.
Injection molds, which are usually made from steel or aluminum, carry a hefty cost. However, the cost per part is very economical if you need several thousand parts per year.
Injection molding is the process of making custom plastic parts by injecting molten plastic material at high pressure into a metal mold. Just like other forms of plastic molding, after the molten plastic is injected into the mold, the mold is cooled and opened to reveal a solid plastic part.
Plastic molding began in the late 1800’s to fill the need for plastic billiard balls as opposed to the commonly used ivory billiard balls of the time. In 1868, John Wesley Hyatt invented a way to make billiard balls by injecting celluloid into a mold. Four years later, Hyatt and his brother invented and patented a machine to automate the process. This was the first plastic injection molding machine in existence and it used a basic plunger to inject plastic into a mold through a heated cylinder.
Tooling costs are lower with rotational molds than injection or blow molds. The results are lower start-up costs and cost-effective production runs even when producing as few as 25 items at a time.
If you’re not sure, that’s okay! We’re here to help. Just click the button below to contact us and one of our plastic molding specialists will be able offer expert advice to help you decide if rotational molding is the right process for your part or product. Click the big red button below to contact us today!
On average, it takes about 8 weeks to get a thermoform mold ready for production. The cost of a thermoform mold is based upon the size of the part that needs to be produced. A mold for a small part can cost as little as $20,000 while the cost of a larger mold can be upwards of $50,000. [12]
Plastics were introduced into the process in the early 1950’s, when rotational molding was first used to manufacture doll heads. And then in the 1960’s the modern process of rotational molding that allows us to create large hollow containers with low-density polyethylene was developed. In recent history, process improvements, better equipment, and plastic powder developments have sped up the process of creating finished products which has caused rotational molding to grow rapidly in popularity.[3]
However, the nature of the extrusion molding process limits the kinds of products that can be manufactured with this technique.
Thin-gauge thermoforming is commonly used to manufacture disposable cups, containers, lids, trays, blisters, clamshells, and other products for the food and general retail industries. Thick-gauge thermoforming includes parts as diverse as vehicle door and dash panels, refrigerator liners, and utility vehicle beds.
The most popular techniques in plastic molding are rotational molding, injection molding, blow molding, compression molding, extrusion molding, and thermoforming. We’ll cover all these techniques in this guide to help you discover the best process to make your part or product.
GETTING A QUOTE WITH LK-MOULD IS FREE AND SIMPLE.
FIND MORE OF OUR SERVICES:
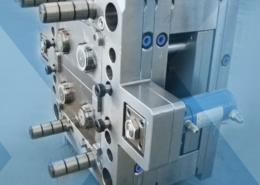
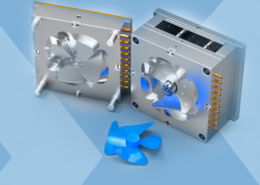
Plastic Molding
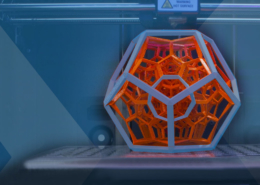
Rapid Prototyping
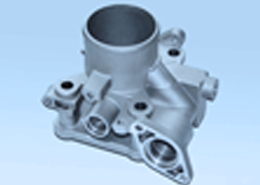
Pressure Die Casting
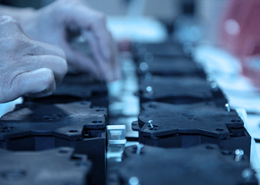
Parts Assembly
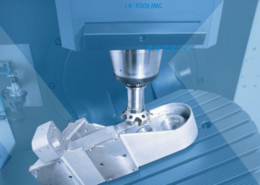