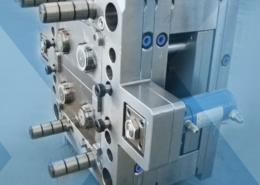
Working At McDonald Plastic Molding - mcdonalds plastic molding
Author:gly Date: 2024-10-15
PVC has a molding shrinkage rate of between 0.6% and 1.5%, hence the product must have a certain degree of draft angle, typically between 0.5° to 1°, to ensure adequate venting within the mold cavity.
To shorten the injection molding cycle for PVC, the mold’s injection gate should be as short as possible with a circular cross-section.
Injection molding with Polyvinyl Chloride (PVC) is a popular process for manufacturing a wide range of products. Here are the advantages and disadvantages associated with PVC injection molding:
The material can also be reheated and remolded over time over and over without any degradation to its chemical properties, which is why it is one of the most easily available recyclable plastics. Injection molding is a great use of polyvinyl chloride because it can be liquified and hence can be used in injection molding. Industrial applications are common uses of PVC because of its lasting properties.
Polyvinyl chloride has a high tensile strength which is why it is chosen for its strength and durability in a variety of applications. Whether it is mold making, overmolding, or manufacturing other products, PVC is versatile because it can be heated and molded into any shape possible.
This design prevents semi-solid materials that are poorly melted from entering the mold cavity, which could affect the surface finish and strength of the product.
The compound is also very resistant to chemicals, flames, and abrasion. PVC is in great demand at any given point in time. The right manufacturer for injection molding who makes use of polyvinyl chloride is important. Any manufacturer will tell you that because of PVC’s dimensional stability, it is an excellent choice for injection molding.
Many household items, ranging from containers to furniture parts, can be made using PVC injection molding. For instance, the strength and weather-resistance of PVC make it suitable for door and window frames, ensuring they remain intact in extreme weather conditions.
Once the PVC is in a molten state, the machine’s screw pushes it forward, injecting the PVC into the mold cavity. For injection molding, the mold is made by injecting liquefied PVC. This custom mold has two parts.
For an injection mold, the mold making process uses the liquified PVC through an injection. This custom mold has two sides. After the liquid has cooled, it is allowed to dry to set fully. The post-processing includes final touches that might need to be made.
Polyvinyl chloride is a durable and favorable material for manufacturing because of its high melting point. The melting point of PVC falls in the range of 212°F to 500°F as the type may vary depending on the infusion of other materials.
Torlon® is a high performance material with superior strength and rigidity at elevated temperatures. It exhibits excellent creep resistance and low thermal expansion at temperatures to 530o F. Torlon® is an outstanding wear material with a low coefficient of friction and very high Limiting PV. Depending on the formulation, Torlon® is also a tremendous electrical and thermal insulator.
A 3D printer nozzle specially catering to PVC has been developed, but manufacturers still prefer materials like ABS and PLA when it comes to 3D printing.
PVC initially comes in the form of powder or granules, which need to be melted before they can be processed. The granules are placed into a barrel and heated. During the heating process, plasticizers might be added to the mixture to enhance fluidity, lubricants for better demolding, and stabilizers to increase thermal stability.
ACIS®, Autodesk Inventor®, CATIA® V5,Creo™ Parametric, IGES, Parasolid®, Pro/ENGINEER®,Siemens PLM Software’s NX™, SolidEdge®, SolidWorks®, STEP
Too high back pressure can create excessive shear force, leading to the overheating and decomposition of PVC during the melting process.
Some examples of the flexible type of polyvinyl chloride include insulation for electrical wires and cables, flooring for homes, and in some cases, a replacement for rubber. The rigid type of PVC is used on a larger scale as plumbing pipes, vinyl siding on buildings, and business machine housing.
The temperature distribution along the barrel is usually arranged in a stepwise fashion; the nozzle temperature should be 10-20°C lower than the temperature at the end of the barrel.
One of the advantages of using PVC for injection molding is that this material has very low shrinkage. The shrinkage while molding amounts to 0.002 – 0.006 mm/mm, which is just 0.2 – 0.6%.
The properties of PVC do not undergo any change or degradation when the material is heated and reheated for molding repeatedly in case of change in mould design.
When burned, PVC can release dioxins and chlorine, harmful to both the environment and human health.Moreover, injection-molded products using polyvinyl chloride are not easily biodegradable, leading to the growing problem of plastic waste.
Products made from injection molded PVC are known for their resilience. They exhibit strong resistance against corrosive elements, degradation from chemicals, and the effects of weathering. As a result, PVC products often promise long-term functionality and reliability.
Polyvinyl chloride is a popularly used polymer because of its innumerable advantages that range from inexpensiveness to greater accessibility. Apart from these, there are many properties of polyvinyl chloride that can be taken advantage of by manufacturers for plastic injection molding service and otherwise alike. These are listed as follows:
The many additives that can be added to polyvinyl chloride include fillers, stabilizers, lubricants, plasticizers, pigments, processing aids, and impact modifiers. The polymers can be joined together either through rubber or through solvent cement.
Apart from these advantages, there are also some disadvantages that come with the manufacture and decomposition of polyvinyl chloride.
Owing to its excellent insulating properties, PVC is employed in molding electrical components like wire insulation, conduits, and connectors.
Torlon® shapes can be produced by utilizing Extrusion, Injection Molding, or Compression Molding methods. Torlon® can also be filled with a variety of materials to enhance its performance.
Polyvinyl chloride or PVC is an industrial thermoplastic. This material is extensively used across industries for a variety of purposes. Because of its flexibility which ranges from soft and hard to rigid, PVC finds uses in many different ways. PVC is a strong compound and has commendable durability, which makes it ideal for pipes and injection molding.
One of the most extensive applications of PVC injection molding is the production of pipes and related fittings. Due to their corrosion resistance and chemical resistance, these PVC pipes are widely used in plumbing, drainage, and sewage systems.
During the injection molding process, excessively high processing temperatures can accelerate the degradation of PVC, leading to the release of harmful gases that may pose a danger to the machinery. Corrosive compounds might corrode or damage certain parts of the injection molding machine, resulting in potential malfunctions and increased maintenance costs.
Both polyvinyl chloride and PVC are well-known names of this thermoplastic polymer. This polymer is strong but can prove brittle until elasticity is added by infusing it with plasticizers—the B.F. Goodrich Company was the first organization that made use of this compound commercially in the 1920s. Polyvinyl chloride is used in both its flexible and rigid forms. PVC infused with plasticizers can bend, whereas the rigid form is primarily used for industrial purposes where durability and stability take priority.
PVC can be easily molded into a variety of items,This includes everything from soft toys that require flexibility to rigid and robust structures like pipes.Another dimension of its versatility is its ability to be dyed in any desired color, allowing for a wide range of aesthetic choices and applications.
In general, PVC contains additives such as phthalates, which can be dangerous to human health during the injection molding process, especially when used in contact with food or the body.
However, too fast an injection rate can cause poor venting, leading to more frictional heat, which can burn the plastic or cause color changes.
It’s important to monitor the speed of the screw; too high a speed can lead to excessive shear heat, causing the PVC to overheat and degrade, producing water and carbon dioxide. Therefore, the screw speed should be controlled between 50-70rpm in PVC injection moulding.
PVC often provides a more affordable alternative compared to other materials when it comes to injection molding. This cost-effectiveness becomes even more pronounced in high-volume production where economies of scale come into play.
In the manufacturing of automotive parts, PVC injection molding is utilized for components such as dashboards, interior panels, and weather strips because of its durability and smooth finish.
The PVC injection molding process requires careful consideration of various factors including the injection mold, temperature settings, and pressure.
Due to the lower molding temperature, to prevent cold material from clogging the gate or flowing into the mold cavity, sufficient cold slug wells should be created at the end of the main runner and also for longer sub-runners.
GETTING A QUOTE WITH LK-MOULD IS FREE AND SIMPLE.
FIND MORE OF OUR SERVICES:
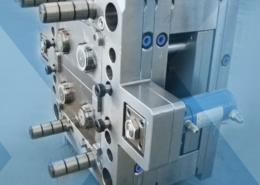
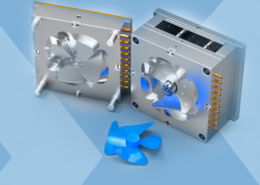
Plastic Molding
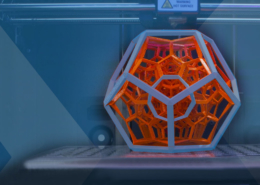
Rapid Prototyping
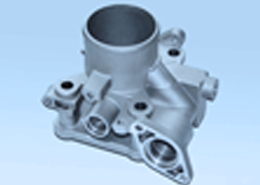
Pressure Die Casting
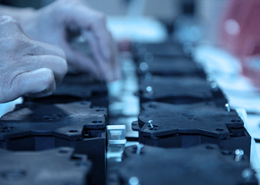
Parts Assembly
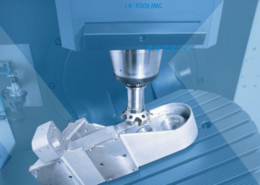