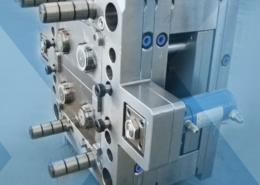
Zephyr Bros. Injection Mould Machine - recycled plastic injection molding
Author:gly Date: 2024-10-15
Overall, it is crucial to comprehend the various varieties of plastic injection molding equipment and how varying sizes and types might be beneficial.
Poor venting happens when air is trapped during filling the cavity, creating counterpressure. When the melt is first injected into the hollow, under most circumstances, it immediately seals the cavity, trapping air in the remaining local spaces.
Any standard plastic molding machine that’s engineered for large parts will require the assistance of other equipment to support it. This is because the parts processed and ejected from these machines tend to exceed 10,000 lbs in weight, needing heavy machinery to lift, transfer, and store in the designated location.
Therefore, it is squeezed instead, leaving some partially empty spaces in the cavity and shortening the shot of the molded item. To remove the air, the process must have vents built or ejection pins installed.
Aside from the large tonnage needed for any large molding process, a dedicated gas-assisted implementation is also required to fulfill large manufacturing requirements. The use of a gas medium allows a better dispersion of pressure throughout the molding, thereby reducing the injection rate or hydraulic shot pressure as the molten resin travels from the runners and into the cavities.
When plastics are heated, cooled, or undergo any kind of reversible physical transformation, stresses tend to be introduced into their workings. These internal stresses lead to material shrinkage or cracks as the part undergoes cooling. As a way of preventing this from happening, gas-assisted molding is introduced to the molding system. This is done in order to ensure that all the molten resin required for the mold fills its cavities and that the material maintains consistent surface contact throughout the entire cycle.
Different types of pressure forces are at play in just one molding cycle. As you’ve learned previously, one of these is clamping force, or the force required to close the mold during injection. When the low clamping force/pressure has not been configured to the right values, the mold will be prematurely opened, thus creating flashes on the part.
You have to be able to work with a professional molding company in China like Richfields Plastics for any successful large part mold. We have the right tonnage of machinery available, can perform gas-assisting, and will assist you throughout the project lifecycle. Click here to request a quote!
One of the more innovative developments in injection molding is gas assisted molding which improves the way plastic parts are produced. A large part molding manufacturer will want to incorporate gas assisted molding in their processes as this improves quality, greatly reduces cycle times, and lessens the weight of the finished part.
However, when the cavity has been filled up to 90% or above, spikes in the pressure can lead to flashing or force the mold to open. This is why the injection pressure has to be controlled during the changeover point where the cycle starts switching over to the holding pressure.
Therefore when it comes to injection pressure (a type of injection molding force applied by the reciprocating screw in the machinery), this should always be balanced against the machine’s clamping pressure. Calculations for injection pressure can be done by determining the part’s size, shape, and the dimensions of the gate opening.
Consult Flying Tiger today if your business is looking for a partner to co-create reliable, high-quality manufacturing outputs.
When working with a plastic molding company to determine the design of the mold, choose one with a greater wall thickness as much as possible. The cost of manufacturing the pre-hardened steel mold may be higher, but you’ll end up with better cost-savings due to a reduction in molding issues.
Like any production process, plastic injection molding manufacturing can have problems and faults. Short shots, often known as "shorts," are one of the most typical quality concerns when the final product is incomplete because the mold did not entirely fill. This article will examine the most frequent causes of this issue and how plastics manufacturers can troubleshoot short shots to maintain high-quality and lean production.
Another potential reason is that the vacuum condition is not suitable for molds—Molds require a place for displaced air to escape, or they will develop air traps or poor venting.
Therefore, beyond the choosing material, better control of mold and melt temperatures also aids in enhancing plastic flow. Flying Tiger offers a range of mold temperature controllers that help you achieve just that.
A "short shot," as the name suggests, occurs when the mold-forming filling stops before the mold chamber is fully filled with the melt, leaving holes or thin sections and producing a defective product.
In this short guide to the injection molding of large plastic parts, you’ve tackled some of the many few requirements needed before starting any large injection molding project. As mentioned, the injection molding process involves similar steps all throughout, but large parts have specialty requirements.
These holes frequently appear around the borders of the finished product or in areas where the mold wall is typically thin—these areas are the last places a mold would commonly fill.
The imbalanced flow in each cavity of a multi-cavity mold can generate local short shots. But when the injection molding machine's capacity is adequate, this defect is primarily brought on by the uneven flow in each gate or the uneven distribution of the mold cavities.
The most frequent cause of failure to fill the mold is the appearance of something that interferes with the flow, and one of the leading candidates for flow issues is the type of plastic polymer itself.
Overall, several factors can lead to the occurrence of short-shot defects, and they all have mutually limiting and influencing effects. Manufacturers must consider how these factors relate to one another, in order to devise a solution to reduce and correct short-shot defects. Note that It is often an ongoing process of monitoring and reviewing.
There is no drastic difference between normal injection molding and large part molding. Both start off with pre-manufactured resin pellets that are poured into the feed hopper, through the nozzle, and heated before being transmitted through the mold’s runners. The main difference, however, has to do with the tonnage which directly affects the clamping force of the machine. When the surface area of the molded part is sizeable, this also requires greater tonnage from the machinery — typically classified as 500 tons of clamping force and above.
Nozzles, sprues, runners, gates, and thin product walls are among the parts that could obstruct melt flow. By raising the nozzle's diameter and temperature, besides utilizing a nozzle with a low flow resistance, the flow resistance of the nozzle can drop to the desired level.
Molding firms will normally want to produce as many large parts in a single cycle as possible, since this reduces time-consuming efforts and labor costs. But, this won’t always be possible due to the limitations of the machinery. For example, an empty mold cavity will allow easier flowing of molten resin due to the lack of resistance at the start of the cycle.
Understanding this, the machine operator should understand how to properly control the opening and closing of the mold. This process is meticulously supervised by the mold operator because the capabilities of the machinery affects the volume of parts per hour, cost, and cycle times.
The production line might have a resin with a high viscosity measured by the Melt Flow Index (MFI), depending on the chosen material. MFI is a good starting point, even though it may not tell the complete story since there are two other factors of concern that may also be involved.
The secret to effective manufacturing and preventing either flow or pressure concerns is to match the right part with the proper molding machine.
Manufacturers can immediately notice that the choice of material affects the flow or movement of the molten plastic inside the mold chamber in the mold cavity because it is a recurring factor in many problems.
There are a variety of tools, procedures, and materials available for manufacturers to avoid short-shot defects. Four of the most tried-and-tested remedies are listed below:
Before undertaking any injection molding project, any molding company in China understands how crucial it is to determine the press size of the injection molding machine. For clients that are new to the industry, bigger doesn’t always translate to better. The injection molding process may remain straightforward, but this isn’t always the case as different industries have varying requirements on molded plastic parts. Manufacturers will ultimately have to follow a guide to injection molding of large plastic parts so that the manufacturing process remains consistent and meets tight tolerances.
Just as your firm would have to choose a company that houses these machines, you also need to consider their capabilities. Ask your prospect molding companies if their manufacturing plant size is adequate enough to house these machines and large molds subsequently. Make sure that they also have the resources to operate, maintain, and repair components of these large tonnage machines, if needed.
In plastic injection molding, a flow hesitation occurs when the flow slows down or stops due to variations in mold thickness. Inconsistent mold thickness causes the flow range of the melt to be too broad and its flow resistance to be excessive.
For instance, an oversized machine may have trouble controlling pressure if the shot size is less than 25% of its capacity, whereas an undersized machine will not have enough pressure or ram speed. Meanwhile, the barrel and mold wall should be heated to prevent the molded plastic from cooling too quickly.
Additionally, because the filling speed is excessively high, chances are that there is insufficient time to release the air via the separating surface.
With all of the above in mind, if you’re coming up with a prototype for any large plastic part, you have to make sure that your manufacturer has the right type of equipment. Generally, a large injection molding machine can take up too much resources. Industry standards set the size for a large molding equipment at an estimate of 40’ x 8 x8. Due to the sheer size, they may cost upwards of $250,000.
Short shots are one of the most frequent problems with plastic injection molding. There are numerous causes of them, but the primary ones are improper injection pressure and speed, including uncontrolled pressure loss brought on by resistance.
Flow restrictions, hesitation of flow, and inadequate venting are all common short-shot defects due to inadequate mold design. Flow restrictions often come from the positioning, dimensions of runners and their gates, and how the molten plastic is poured into the mold.
Finally, a large part injection molding project always considers the wall thickness of the mold. Ideally, thicker wall sections will offer move volume or room for the molten plastic resin to flow. More than just that, they also provide excellent insulation to the resin, thereby allowing it to flow freely and further throughout the mold’s cavities without requiring an increase in pressure.
With many accumulated years of experience with numerous domestic and foreign clients, Flying Tiger is confident in assisting corporate customers in quickly identifying the cause of short shots and other injection molding defects, thereby assisting in cutting down on resource waste and boosting product yield.
GETTING A QUOTE WITH LK-MOULD IS FREE AND SIMPLE.
FIND MORE OF OUR SERVICES:
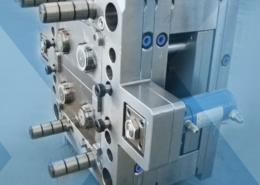
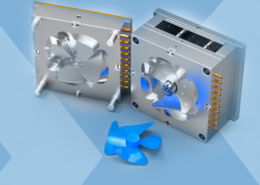
Plastic Molding
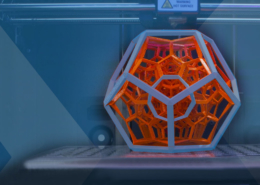
Rapid Prototyping
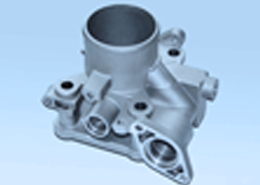
Pressure Die Casting
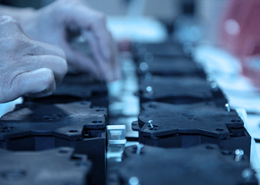
Parts Assembly
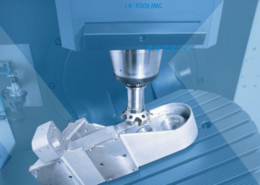