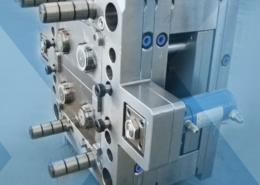
▷ Plastic recycling process - ENGEL - recycled plastic moulding
Author:gly Date: 2024-10-15
Our experience with plastic injection molding and broad knowledge of plastic resins provide us with a wealth of expertise we leverage on behalf of our clients. Stelray has an outstanding supplier record associated with many Fortune 500 companies, and we take pride in knowing our customers rely on Stelray for consistent quality, superior service, and on-time delivery for their injection molding projects.
We understand the importance of meeting critical dimensional tolerance requirements for high-precision applications such as in tech, bioscience and OEM replacement. Among the industries we serve:
As a full-service American Injection Molding Institute, we offer in-house mold tooling, mold design and engineering support, and custom manufacturing for a variety of plastic injection molded products all in our North East Injection Molding facility. Backed by advanced machinery and seasoned expertise, our facility is fully prepared for large part injection molding, ensuring precision and efficiency at scale. Our clients include top U.S. and international brands such as ITT, Panasonic, Hill-Rom, Hubbell, Sub-Zero and Welch Allyn.
Every new project at Stelray begins with a preliminary plastic design for manufacturing (DFM) review to ensure that we understand your plastic product needs from the beginning. Our comprehensive precision quality assurance systems ensure that the components you pay for are exactly what you need. Our range of custom plastic injection molding services and creative approach to streamlined manufacturing problem-solving also allows us to manufacture high-quality complex components and assemblies at the best possible price.
In simple terms: one mold, two injections, one cycle. The first plastic injection runs through the mold and then gates are closed, the mold is automatically rotated (rotary mold), or a part is transferred within the same mold (pick and place) and a different type of plastic is injected into the mold.
Our Connecticut Injection Molding facility is ISO 9001:2015 certified to ensure that every project we take on meets all applicable quality requirements. We also are an FDA Registered Plastic Manufacturing Company and compliant with 21 CFR 820 and Good Manufacturing Practices, among other plastic industry certifications and standards.
Get in touch to start your next project or to receive a no-obligation free quote generated by our team of experts on your latest plastic design.
Double shot, or two-shot mold design, combines two materials into one part in a single mold. One mold helps in the reduction of secondary machines, processes and molds. When designed right, two-shot molds significantly reduce the amount of scrap, cycle times, resin, work-in-process, and assembly, thus, driving down costs and improving the quality and consistency of the finished product. Two-shot molds can even be used with Rotary or Pick and Place mechanical actions.
Stelray Plastic Products is a leading global custom plastic injection molding company providing cost-effective solutions across a wide array of applications and industries.
All design and manufacture of tooling is done by our team—for a complete custom application. As a plastic products company, we offer a range of post-mold secondary operations, including ultrasonic welding, pad printing, heat-staking, soldering, assembly, and packaging as a part of our plastic injection molding services. Our engineering staff and machine technicians are experienced in a broad range of plastic resins; everything from commodity-grade to engineering-performance polymers and exotic resins. Given this knowledge, we can help guide you in selecting the best material for your project. We also offer biodegradable plastic resins when appropriate.
The customer needed a sturdy lightweight plastic handle for a cooler, however also desired a non-slip over-mold for comfort and function.
Mold closes and the lower four cavities are filled with the first shot of hard plastic. Mold slides are retracted after the mold opens. Robotics will remove the parts from the lower cores as the ejector plates advance. Parts are placed on the cores of the upper (over-mold) side. Slides are advanced to capture the parts, the mold closes and is filled with the second non-slip soft shot.
A two-shot mold offers different resins in the same part and same mold. Those different resins in a second shot could be for:
GETTING A QUOTE WITH LK-MOULD IS FREE AND SIMPLE.
FIND MORE OF OUR SERVICES:
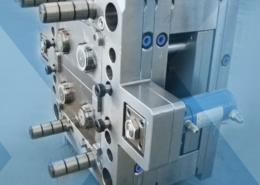
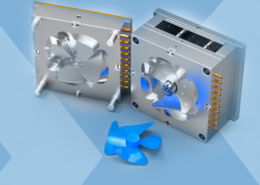
Plastic Molding
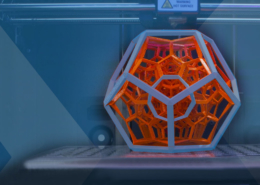
Rapid Prototyping
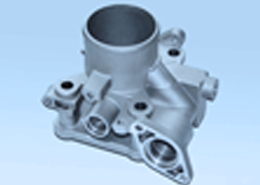
Pressure Die Casting
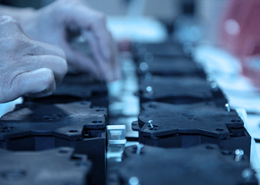
Parts Assembly
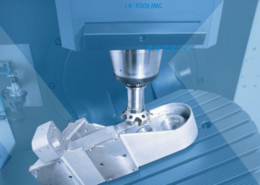