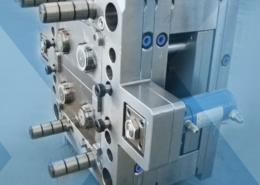
Exploring the Art of Molding Polystyrene
Author:gly Date: 2024-06-08
Molding polystyrene stands as a cornerstone of modern manufacturing, offering a myriad of possibilities for creating lightweight, durable, and versatile products. From packaging materials to consumer goods and construction components, polystyrene molding plays a vital role in shaping our everyday lives. In this article, we delve into the fascinating world of molding polystyrene, uncovering its origins, mechanics, applications, and future prospects.
Origins and Background
Polystyrene, a synthetic polymer derived from styrene monomers, was first discovered in the late 19th century but gained commercial prominence in the 1930s with the development of expandable polystyrene (EPS) and high-impact polystyrene (HIPS). These versatile materials revolutionized the packaging, insulation, and consumer goods industries, thanks to their lightweight, insulating, and cost-effective properties. The advent of polystyrene molding techniques further expanded the utility and versatility of this material, enabling the production of complex shapes and structures with ease.
Mechanics and Operation
Molding polystyrene involves heating polystyrene resin pellets until they reach a molten state, then injecting or compressing the material into a mold cavity to form the desired shape. The choice of molding technique depends on factors such as part complexity, production volume, and dimensional accuracy requirements. Injection molding is commonly used for producing intricate parts with high precision, while extrusion and thermoforming techniques are suitable for creating large, thin-walled components such as sheets, cups, and packaging trays.
Types of Polystyrene Molding Processes
Injection Molding
Injection molding is a versatile process used to produce a wide range of polystyrene parts, from small, intricate components to large, complex assemblies. The process involves injecting molten polystyrene into a mold cavity under high pressure, where it solidifies to form the final product. Injection molding offers fast cycle times, high production rates, and excellent dimensional accuracy, making it ideal for mass production applications.
Extrusion
Extrusion involves forcing molten polystyrene through a die to create continuous lengths of uniform cross-sections. This process is commonly used for producing sheets, films, and profiles used in packaging, construction, and signage applications. Extruded polystyrene (XPS) foam boards, known for their excellent insulating properties, are widely used in building insulation and packaging materials.
Thermoforming
Thermoforming is a versatile process used to shape heated polystyrene sheets over a mold using vacuum, pressure, or mechanical force. This process is used for producing a wide range of products, including packaging trays, disposable cups, and automotive components. Thermoformed polystyrene products offer lightweight, cost-effective solutions for various applications.
Advantages and Benefits
Lightweight and Insulating Properties
Polystyrene is renowned for its lightweight and insulating properties, making it an ideal material for packaging, insulation, and consumer goods. Expanded polystyrene (EPS) foam, commonly used in packaging materials and building insulation, offers excellent thermal insulation and shock absorption properties, protecting products during shipping and storage.
Versatility and Customization
Polystyrene molding processes offer unparalleled versatility and customization options, allowing designers and engineers to create parts with intricate details, complex geometries, and custom finishes. Whether producing consumer electronics, automotive components, or medical devices, polystyrene molding techniques enable manufacturers to meet diverse design requirements and specifications.
Cost-Effective Production
Polystyrene molding processes, such as injection molding and extrusion, offer cost-effective solutions for producing high-volume parts with minimal material waste. The high-speed production capabilities of molding machines, coupled with the ability to replicate molds quickly and efficiently, result in reduced labor costs and shorter lead times, making polystyrene molding an attractive option for mass production applications.
Applications and Industries
Polystyrene molding finds applications across a wide range of industries, each benefiting from its unique properties and capabilities.
Packaging Industry
In the packaging industry, polystyrene is used to produce a variety of packaging materials, including foam trays, clamshells, and protective packaging inserts. Expanded polystyrene (EPS) foam is prized for its lightweight, cushioning, and insulating properties, making it ideal for protecting fragile items during shipping and storage.
Construction Sector
In the construction sector, polystyrene is used in various applications, including insulation boards, building panels, and decorative moldings. Extruded polystyrene (XPS) foam boards offer excellent thermal insulation and moisture resistance, making them ideal for insulating roofs, walls, and foundations in residential and commercial buildings.
Consumer Goods
In the consumer goods industry, polystyrene is used to produce a wide range of products, including disposable cups, food containers, and household appliances. Thermoformed polystyrene packaging offers lightweight, cost-effective solutions for packaging food and beverages, while injection-molded polystyrene components provide durability and aesthetics in consumer electronics and appliances.
Future Directions and Innovations
Looking ahead, the future of polystyrene molding holds promise for further advancements and innovations. Researchers and manufacturers are exploring sustainable alternatives to traditional polystyrene materials, such as bio-based polymers and recyclable plastics, to reduce environmental impact and promote circular economy initiatives. Additionally, advancements in digital modeling, additive manufacturing, and automation are poised to revolutionize the polystyrene molding process, offering increased efficiency, customization, and sustainability.
Conclusion
In conclusion, molding polystyrene represents a dynamic and versatile manufacturing process with vast potential for innovation and growth. From its humble beginnings to its current state-of-the-art technologies, polystyrene molding continues to shape industries and enrich lives worldwide. By embracing sustainability, advancing materials science, and leveraging digital technologies, the future of polystyrene molding holds promise for creating a more sustainable, efficient, and interconnected world. As we navigate the challenges and opportunities ahead, let us continue to push the boundaries of what is possible and strive for excellence in molding polystyrene.
GETTING A QUOTE WITH LK-MOULD IS FREE AND SIMPLE.
FIND MORE OF OUR SERVICES:
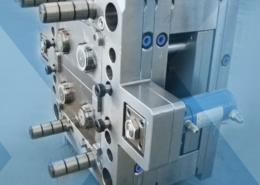
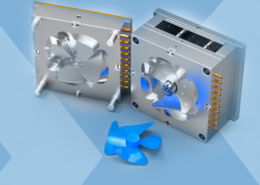
Plastic Molding
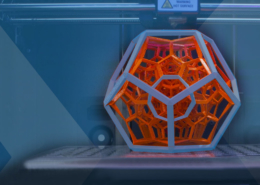
Rapid Prototyping
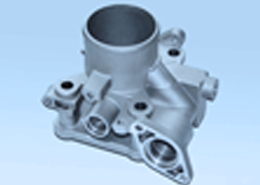
Pressure Die Casting
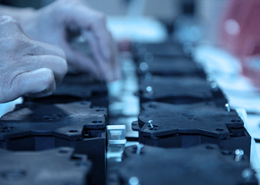
Parts Assembly
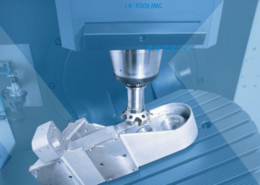