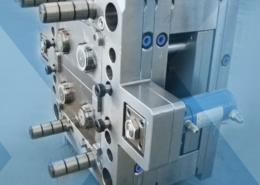
Exploring the Essentials of Molding Tooling
Author:gly Date: 2024-06-08
Introduction
Molding tooling serves as the cornerstone of modern manufacturing, providing the means to shape raw materials into precision-engineered components with unparalleled accuracy and efficiency. From intricate automotive parts to delicate medical devices, molding tooling plays a pivotal role in bringing innovative designs to life. This article delves into the intricacies of molding tooling, unraveling its methodologies, applications, and the critical role it plays in driving progress across industries.
Understanding Molding Tooling
Molding tooling refers to the specialized tools and equipment used in the injection molding process to create intricate parts with precision and repeatability. These tools, commonly referred to as molds or dies, are typically made from hardened steel or aluminum and feature cavities and cores that define the shape and dimensions of the final part. Molding tooling is designed to withstand the high pressures and temperatures of the injection molding process, ensuring the production of high-quality components with minimal defects.
The Design and Manufacturing Process
The design and manufacturing of molding tooling are highly complex processes that require meticulous attention to detail and engineering expertise. The process begins with the design of the mold, which involves CAD modeling and simulation to optimize part geometry, cooling channels, and ejector systems. Once the design is finalized, skilled toolmakers utilize advanced machining techniques, such as CNC milling and EDM (electrical discharge machining), to fabricate the mold components with precision and accuracy. The finished mold undergoes rigorous testing and validation to ensure conformance to design specifications before being deployed for production.
Types of Molding Tooling
Molding tooling encompasses a variety of types and configurations to accommodate different part geometries, materials, and production volumes. Common types of molding tooling include:
Single cavity molds: Ideal for low-volume production and prototyping, single cavity molds consist of a single cavity and core, producing one part per cycle.
Multi-cavity molds: Designed for high-volume production, multi-cavity molds feature multiple cavities arranged in a single mold, enabling simultaneous production of multiple parts in each cycle.
Family molds: Family molds are used to produce multiple different parts in a single mold, reducing tooling costs and increasing production efficiency.
Insert molds: Insert molds incorporate metal or plastic inserts into the mold cavity to form features such as threads, bosses, or inserts in the final part.
Each type of molding tooling offers unique advantages and considerations, depending on the specific requirements of the application.
Advancements and Future Directions
Advancements in materials science, manufacturing technologies, and design software continue to drive innovation in molding tooling. Additive manufacturing techniques, such as 3D printing, offer new possibilities for rapid prototyping and tooling fabrication, enabling faster iteration and reduced time-to-market. Furthermore, the integration of sensors and IoT (Internet of Things) technology into molding tooling allows for real-time monitoring of production processes, enabling predictive maintenance and quality control. Looking ahead, research into novel materials and manufacturing techniques holds promise for further enhancing the performance, efficiency, and sustainability of molding tooling in the years to come.
Conclusion
In conclusion, molding tooling stands as a testament to human ingenuity and technological innovation, enabling the mass production of intricate components across a myriad of industries. From concept to creation, molding tooling plays a vital role in transforming ideas into tangible products that shape our world. As we continue to push the boundaries of what is possible, the evolution of molding tooling will undoubtedly pave the way for new advancements and breakthroughs, driving progress and shaping the future of manufacturing.
GETTING A QUOTE WITH LK-MOULD IS FREE AND SIMPLE.
FIND MORE OF OUR SERVICES:
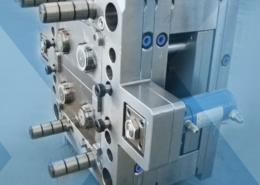
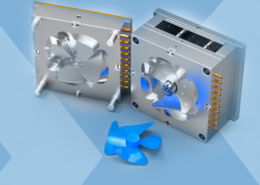
Plastic Molding
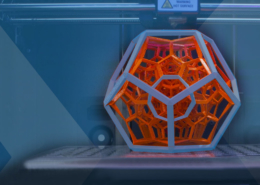
Rapid Prototyping
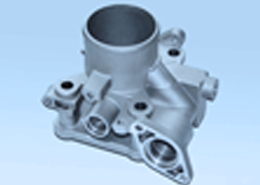
Pressure Die Casting
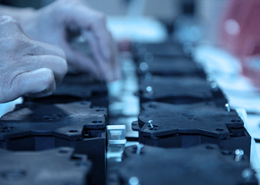
Parts Assembly
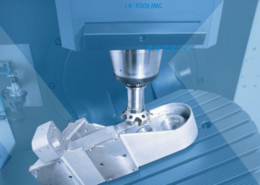