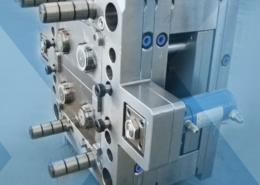
Unveiling the Versatility of Nylon Injection Molding
Author:gly Date: 2024-06-08
Introduction:
Nylon injection molding stands as a cornerstone of modern manufacturing, offering unparalleled versatility, durability, and performance across a myriad of applications. This sophisticated process involves the injection of molten nylon resin into precise molds, where it solidifies to form robust and intricately detailed parts. In this article, we embark on a journey to explore the intricacies of nylon injection molding, uncovering its applications, advantages, challenges, and future prospects.
Exploring the Origins of Nylon Injection Molding
The roots of nylon injection molding can be traced back to the mid-20th century when the DuPont Corporation introduced nylon, the first synthetic thermoplastic polymer. This groundbreaking material, renowned for its strength, flexibility, and chemical resistance, revolutionized various industries, including automotive, aerospace, consumer goods, and beyond. Nylon's exceptional properties, coupled with the advent of injection molding technology, propelled it to the forefront of modern manufacturing, enabling the production of complex and durable components with unmatched precision and efficiency.
Nylon in Injection Molding:
Nylon's suitability for injection molding stems from its unique combination of properties, including high tensile strength, impact resistance, abrasion resistance, and dimensional stability. These characteristics make it an ideal candidate for applications requiring structural integrity, toughness, and longevity, such as gears, bearings, bushings, and structural components. Moreover, nylon's low coefficient of friction, self-lubricating properties, and resistance to chemicals and moisture enhance its versatility and reliability in challenging environments.
The Injection Molding Process:
The injection molding process for nylon follows a series of precise steps to ensure optimal part quality and performance. It begins with the selection of suitable nylon resins, tailored to meet specific mechanical, thermal, and environmental requirements. The resin pellets are then fed into the hopper of the injection molding machine, where they are heated to their melting point and injected into a pre-designed mold cavity under high pressure. Once injected, the molten nylon fills the mold cavity, conforming to its intricate geometry and features. After a brief cooling period, the mold opens, and the solidified part is ejected, ready for secondary operations or assembly.
Applications Across Industries:
Nylon injection molding finds extensive use across diverse industries, owing to its exceptional properties and versatility. In the automotive sector, nylon components are utilized in engine parts, transmission systems, under-the-hood applications, and interior trim components, where high strength, heat resistance, and dimensional stability are critical. Similarly, in the consumer goods industry, nylon injection molding enables the production of sporting goods, appliances, power tools, and electronic enclosures, where durability, impact resistance, and aesthetic appeal are paramount. Moreover, in the aerospace and defense sectors, nylon components serve in aircraft interiors, structural reinforcements, and lightweight assemblies, where performance, reliability, and compliance with stringent regulations are essential.
Challenges and Future Directions:
Despite its myriad benefits, nylon injection molding poses certain challenges, including warping, shrinkage, and mold design complexity. Addressing these challenges requires a comprehensive understanding of material behavior, process parameters, and mold design principles. Moreover, the future of nylon injection molding holds promise for further innovation and advancement, driven by advancements in material science, process optimization, and digital technologies. The integration of sustainable materials, such as bio-based nylons and recycled resins, offers opportunities to reduce environmental impact and promote circular economy principles. Furthermore, the convergence of additive manufacturing, artificial intelligence, and predictive analytics paves the way for smart manufacturing solutions, enabling real-time monitoring, optimization, and customization of injection molding processes.
Conclusion:
In conclusion, nylon injection molding stands as a testament to human ingenuity and engineering excellence, offering a versatile, reliable, and cost-effective solution for producing complex and durable plastic components across industries. Its evolution from a pioneering material to a sophisticated manufacturing process underscores its enduring relevance and adaptability in an ever-changing world. By embracing technological advancements, sustainability initiatives, and collaborative partnerships, the realm of nylon injection molding continues to push the boundaries of innovation, driving progress and prosperity for generations to come.
GETTING A QUOTE WITH LK-MOULD IS FREE AND SIMPLE.
FIND MORE OF OUR SERVICES:
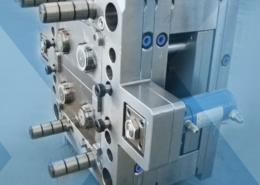
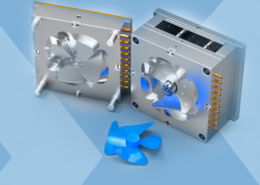
Plastic Molding
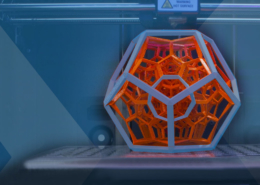
Rapid Prototyping
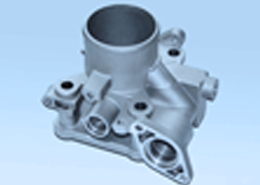
Pressure Die Casting
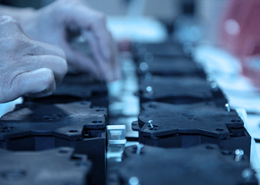
Parts Assembly
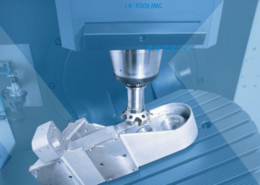