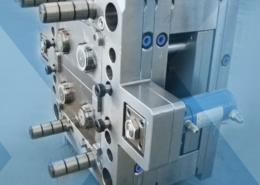
Exploring Plastic Injection Molding Cost
Author:gly Date: 2024-06-08
Introduction
Plastic injection molding is a pivotal process in modern manufacturing, enabling the creation of intricate and durable plastic parts with high precision and efficiency. However, understanding the costs associated with this process is essential for businesses aiming to optimize their production strategies. In this article, we delve into the various facets of plastic injection molding cost to provide a comprehensive understanding for readers.
Cost Factors in Plastic Injection Molding
Material Costs
Material selection plays a crucial role in determining the overall cost of plastic injection molding. Different types of thermoplastics have varying costs, with factors such as resin quality, additives, and required properties influencing the pricing. Additionally, the quantity of material required for each part and any waste generated during the molding process contribute to material costs.
Tooling and Equipment Expenses
Investment in molds and equipment is a significant upfront cost in plastic injection molding. The complexity of the part design, mold material, and anticipated production volume impact tooling expenses. High-quality molds made from durable materials may entail higher initial costs but can offer long-term benefits in terms of production efficiency and part quality.
Labor and Overhead Charges
Labor costs encompass the wages of skilled operators and technicians involved in the injection molding process. Additionally, overhead expenses such as facility maintenance, utilities, and administrative overhead contribute to the overall manufacturing cost. Efficient utilization of labor and optimization of production processes are essential for minimizing these expenditures.
Quality Assurance and Inspection Costs
Ensuring the quality and integrity of molded parts necessitates investment in inspection equipment and quality control measures. Inspection costs include the expenses associated with testing, measuring, and validating parts to meet quality standards. Implementing robust quality assurance protocols is crucial for minimizing defects and rework, thereby reducing overall production costs.
Production Volume and Economies of Scale
The volume of production significantly influences the per-unit cost in plastic injection molding. Higher production volumes often lead to economies of scale, where the fixed costs are spread across a larger number of units, resulting in lower per-part costs. Strategic planning and forecasting are vital for leveraging economies of scale while maintaining optimal inventory levels.
Cost Optimization Strategies
Design for Manufacturability
Adopting design principles that facilitate efficient manufacturing can help reduce plastic injection molding costs. Design for manufacturability (DFM) involves optimizing part geometry, minimizing undercuts and complex features, and selecting suitable materials to streamline the production process and enhance moldability.
Process Optimization and Efficiency Enhancements
Continuous process improvement initiatives, such as lean manufacturing and Six Sigma methodologies, can lead to cost savings in plastic injection molding. Identifying and eliminating waste, optimizing cycle times, and implementing automation technologies contribute to enhanced efficiency and reduced production costs.
Supplier Collaboration and Negotiation
Building strong partnerships with material suppliers, mold makers, and equipment vendors can yield cost-saving opportunities through bulk purchasing, favorable pricing agreements, and collaborative problem-solving. Effective negotiation skills and transparent communication are essential for securing competitive pricing and favorable terms.
Conclusion
Understanding the intricacies of plastic injection molding cost is imperative for businesses seeking to optimize their manufacturing processes and maintain competitiveness in the market. By considering factors such as material costs, tooling expenses, labor charges, and production volume, companies can develop effective cost optimization strategies. Embracing initiatives such as design for manufacturability, process optimization, and supplier collaboration can drive significant cost savings and foster sustainable growth in the plastic injection molding industry.
Suggestions for Future Research
Future research endeavors could focus on exploring advanced materials and technologies that offer cost-effective alternatives in plastic injection molding. Additionally, investigating the integration of digital manufacturing solutions, such as additive manufacturing and predictive maintenance, may provide insights into further enhancing cost efficiency and productivity in the industry.
GETTING A QUOTE WITH LK-MOULD IS FREE AND SIMPLE.
FIND MORE OF OUR SERVICES:
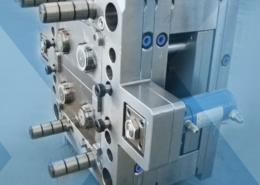
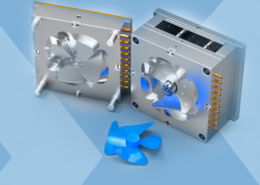
Plastic Molding
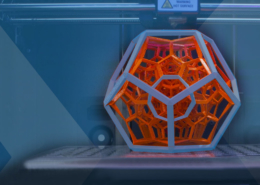
Rapid Prototyping
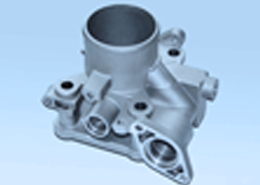
Pressure Die Casting
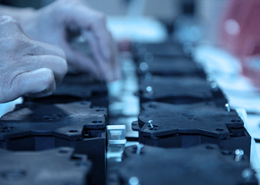
Parts Assembly
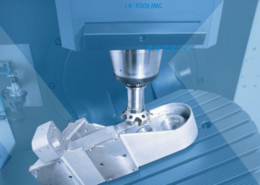