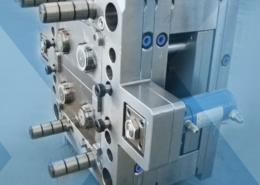
The Evolution of Plastic Injection Molding Services: Revolutionizing Manufacturi
Author:gly Date: 2024-06-08
Plastic injection molding services represent a pivotal cornerstone in modern manufacturing, enabling the mass production of intricate plastic components with unparalleled precision and efficiency. As technology progresses, the capabilities and applications of injection molding continue to expand, driving innovation across various industries. This article delves into the intricacies of plastic injection molding services, exploring its evolution, applications, benefits, challenges, and future prospects.
Evolution of Injection Molding Technology
Injection molding has undergone a remarkable evolution since its inception in the late 19th century. Initially developed for producing simple celluloid objects, such as buttons and combs, the process has evolved into a sophisticated technique capable of fabricating complex parts for diverse industries. Advancements in materials, machinery, and computer-aided design (CAD) have revolutionized injection molding, facilitating the production of highly precise and customized components at scale.
Historical Development
The journey of injection molding began with the invention of the first injection molding machine by John Wesley Hyatt in 1872. Subsequent innovations, including the introduction of thermoplastics in the 20th century and the adoption of computerized controls in the late 20th century, propelled the industry forward. Today, injection molding stands as a cornerstone of modern manufacturing, driving efficiency, versatility, and cost-effectiveness.
Technological Advancements
Technological advancements have been instrumental in enhancing the capabilities of injection molding. The integration of robotics, automation, and real-time monitoring systems has optimized production processes, minimizing defects and maximizing output. Additionally, innovations in mold design, such as conformal cooling and multi-cavity molds, have further improved efficiency and product quality.
Applications Across Industries
Plastic injection molding services find applications across a myriad of industries, ranging from automotive and aerospace to healthcare and consumer goods. The versatility of injection molding enables the production of diverse components, including housing enclosures, automotive parts, medical devices, and consumer electronics.
Automotive Industry
In the automotive sector, injection molding is widely used for manufacturing interior and exterior components, such as dashboards, bumpers, and door panels. The process offers automotive manufacturers the flexibility to create lightweight, durable, and aesthetically pleasing parts while maintaining cost efficiency.
Healthcare Sector
In the healthcare industry, injection molding plays a critical role in producing medical devices, equipment, and packaging. From syringes and IV components to prosthetic devices and surgical instruments, injection molding ensures the precise fabrication of sterile, biocompatible, and functional products that meet stringent regulatory standards.
Consumer Electronics
The consumer electronics sector relies heavily on injection molding for producing casings, connectors, and other components. With the demand for sleek, ergonomic designs and high-performance materials, injection molding enables manufacturers to meet consumer expectations while optimizing production costs and lead times.
Benefits and Challenges
Plastic injection molding offers numerous benefits, including:
Cost Efficiency:
Injection molding enables high-volume production at low per-unit costs, making it economically viable for mass production.
Precision and Complexity:
The process allows for the fabrication of intricate and highly precise components with consistent quality.
Material Versatility:
Injection molding supports a wide range of thermoplastic and thermosetting materials, offering flexibility in design and functionality.
However, injection molding also presents certain challenges, such as:
Initial Tooling Costs:
The upfront costs associated with mold design and fabrication can be substantial, particularly for complex parts.
Lead Time:
Developing molds and initiating production may require significant lead time, impacting time-to-market for new products.
Design Limitations:
Certain design features, such as undercuts and thin walls, may pose challenges in moldability and part quality.
Future Prospects and Innovations
Looking ahead, the future of plastic injection molding services is poised for further innovation and growth. Emerging trends such as 3D printing of molds, advanced simulation technologies, and sustainable materials are shaping the trajectory of the industry. Moreover, the integration of artificial intelligence (AI) and machine learning promises to optimize production processes, reduce waste, and enhance product performance.
In conclusion, plastic injection molding services have revolutionized modern manufacturing, offering unparalleled precision, efficiency, and versatility. As technology continues to advance, injection molding will remain a cornerstone of industrial production, driving innovation across diverse sectors. By embracing emerging technologies and addressing inherent challenges, the industry is poised for sustained growth and continued evolution.
GETTING A QUOTE WITH LK-MOULD IS FREE AND SIMPLE.
FIND MORE OF OUR SERVICES:
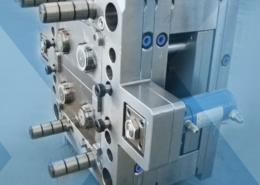
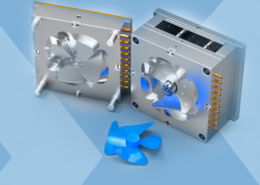
Plastic Molding
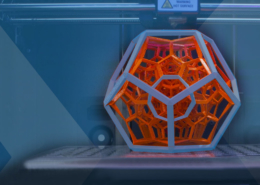
Rapid Prototyping
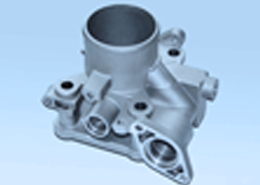
Pressure Die Casting
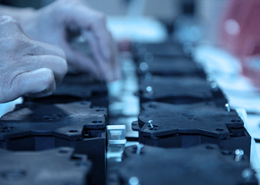
Parts Assembly
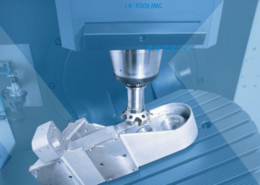