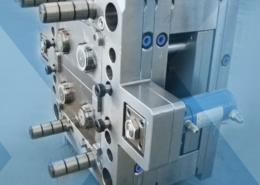
Exploring the World of Plastic Injection Products
Author:gly Date: 2024-06-08
Plastic injection products have become ubiquitous in our modern world, shaping various aspects of our daily lives. From the smallest components in electronic devices to the largest automotive parts, plastic injection molding has revolutionized manufacturing processes across industries. This article aims to delve into the realm of plastic injection products, unraveling their significance, applications, and future prospects.
The Process of Plastic Injection Molding
Plastic injection molding is a manufacturing process wherein molten plastic is injected into a mold cavity under high pressure. The process begins with the design phase, where engineers create precise molds tailored to the desired product specifications. Next, plastic pellets are melted and injected into the mold, where they cool and solidify into the final product shape. This highly versatile process enables the production of complex geometries with exceptional accuracy and consistency.
The Advantages of Injection Molding
One of the key advantages of plastic injection molding is its ability to mass-produce identical parts with minimal variation. This efficiency makes it ideal for large-scale manufacturing, where consistency and cost-effectiveness are paramount. Additionally, injection molding allows for the use of a wide range of materials, including thermoplastics, thermosets, and elastomers, offering versatility in product design and performance.
Sustainable Practices in Injection Molding
In recent years, there has been a growing emphasis on sustainability within the plastics industry. Manufacturers are increasingly adopting eco-friendly materials, optimizing production processes to minimize waste, and exploring recycling solutions for post-consumer plastics. These initiatives aim to mitigate the environmental impact of plastic injection products while maintaining the benefits of this versatile manufacturing technique.
Applications Across Industries
The versatility of plastic injection molding has led to its widespread adoption across diverse industries, ranging from healthcare to consumer electronics.
Automotive Sector
In the automotive sector, plastic injection products are integral components of vehicle interiors, exteriors, and engine compartments. From dashboard panels to bumper covers, injection-molded parts contribute to vehicle aesthetics, functionality, and safety. The lightweight nature of plastics also aids in fuel efficiency and reduces carbon emissions, aligning with automotive industry trends towards sustainability.
Medical Devices
Plastic injection molding plays a crucial role in the production of medical devices, where precision and reliability are paramount. From syringes to implantable components, injection-molded parts offer sterile, biocompatible solutions for various medical applications. Advanced materials and manufacturing techniques ensure compliance with stringent regulatory standards, safeguarding patient safety and well-being.
Consumer Electronics
The consumer electronics industry relies heavily on plastic injection molding to produce intricate components for smartphones, tablets, laptops, and other electronic devices. High-performance plastics, such as polycarbonate and ABS, offer durability, thermal stability, and aesthetic appeal, meeting the demanding requirements of modern electronics. Miniaturization trends drive the need for smaller, more intricate parts, driving innovation in injection molding technology.
Challenges and Innovations
Despite its numerous benefits, plastic injection molding faces challenges related to material selection, design complexity, and environmental sustainability.
Material Selection and Performance
The choice of plastic material significantly influences product performance, durability, and cost. Manufacturers must carefully evaluate the mechanical properties, chemical resistance, and processing characteristics of different polymers to ensure optimal performance in specific applications. Advances in material science continue to expand the range of available options, offering tailored solutions for diverse industry needs.
Design Complexity and Tooling
Complex part geometries present challenges in mold design, tooling fabrication, and injection molding process optimization. Design for manufacturability (DFM) principles help engineers optimize part designs for injection molding, minimizing production defects and cycle times. Innovations in mold-making technologies, such as 3D printing and CNC machining, streamline the prototyping and production process, enabling faster time-to-market for new products.
Future Outlook and Trends
Looking ahead, the future of plastic injection products is shaped by technological advancements, market dynamics, and evolving consumer preferences.
Digitalization and Industry 4.0
The integration of digital technologies, such as IoT sensors, AI-driven analytics, and cloud-based manufacturing platforms, is transforming the landscape of injection molding. Smart factories equipped with real-time monitoring and predictive maintenance capabilities optimize production efficiency, reduce downtime, and enhance quality control. Industry 4.0 principles drive automation, connectivity, and agility, enabling manufacturers to adapt to changing market demands swiftly.
Sustainable Solutions and Circular Economy
The imperative for sustainability drives innovation in materials, processes, and business models within the plastics industry. From bio-based polymers to closed-loop recycling systems, stakeholders are exploring holistic approaches to minimize environmental impact and promote circularity. Collaborative initiatives across the value chain foster resource efficiency, waste reduction, and responsible consumption, paving the way for a more sustainable future for plastic injection products.
Conclusion
In conclusion, plastic injection molding continues to be a cornerstone of modern manufacturing, enabling the production of diverse products that shape our everyday lives. From automotive components to medical devices, injection-molded plastics offer unparalleled versatility, performance, and cost-effectiveness. Despite facing challenges related to sustainability and design complexity, ongoing innovations and technological advancements drive the evolution of injection molding towards a more sustainable, efficient, and interconnected future. By embracing digitalization, sustainable practices, and collaborative partnerships, the plastics industry can navigate towards a brighter and more resilient tomorrow.
GETTING A QUOTE WITH LK-MOULD IS FREE AND SIMPLE.
FIND MORE OF OUR SERVICES:
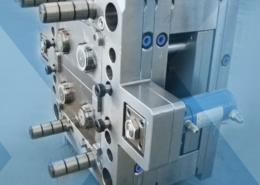
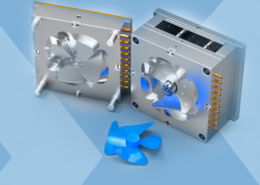
Plastic Molding
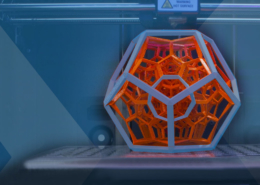
Rapid Prototyping
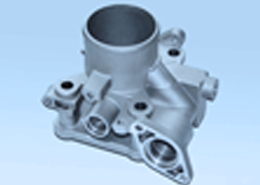
Pressure Die Casting
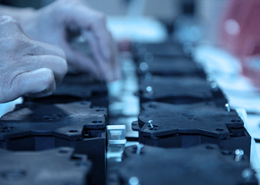
Parts Assembly
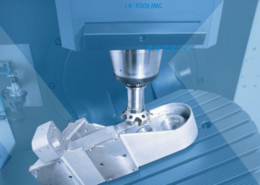