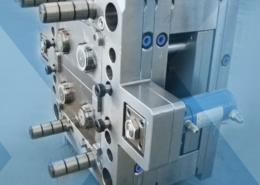
Unraveling the Dynamics of Plastic Molding Costs
Author:gly Date: 2024-06-08
Plastic molding costs stand as a pivotal consideration in manufacturing, influencing product feasibility, pricing, and competitiveness. Delving into the intricacies of these costs reveals a complex interplay of factors that shape the economic landscape of plastic molding. This article aims to dissect the various facets of plastic molding costs, shedding light on their significance, determinants, and implications.
Introduction
The realm of plastic molding costs encompasses a wide array of expenses incurred throughout the manufacturing process. From material procurement to tooling, labor, and overhead, each component contributes to the overall cost structure. Understanding the nuances of these costs is paramount for manufacturers seeking to optimize efficiency, enhance profitability, and maintain competitiveness in the market.
Factors Influencing Costs
Several factors exert influence over plastic molding costs, each playing a unique role in shaping the economic landscape of production. Material selection stands as a primary determinant, with different polymers varying in price and performance characteristics. Additionally, the complexity of the part geometry, mold design, and production volume all contribute to cost variability. Furthermore, factors such as labor rates, energy costs, and regulatory compliance requirements further compound the intricacies of plastic molding costs.
Cost Optimization Strategies
In response to the multifaceted nature of plastic molding costs, manufacturers employ various strategies to optimize efficiency and minimize expenses. Design for manufacturability (DFM) principles guide product development, emphasizing simplicity, moldability, and material efficiency. Concurrent engineering practices facilitate collaboration between design, engineering, and manufacturing teams, streamlining the production process and reducing lead times. Additionally, advancements in automation and process optimization technologies enhance productivity while reducing labor costs.
Environmental and Social Considerations
Beyond economic considerations, plastic molding costs also intersect with environmental and social dimensions. With growing concerns over sustainability and environmental impact, manufacturers are increasingly adopting eco-friendly materials and processes. Recycling initiatives, waste reduction measures, and energy-efficient practices not only mitigate environmental harm but also contribute to cost savings in the long run. Moreover, addressing social responsibility entails fair labor practices, employee welfare initiatives, and community engagement efforts, all of which may impact production costs but are integral to ethical business conduct.
Global Trends and Future Outlook
Looking ahead, the landscape of plastic molding costs is poised for continued evolution in response to shifting market dynamics and technological advancements. Emerging trends such as additive manufacturing, digital twin technology, and the Internet of Things (IoT) hold promise for enhancing efficiency, reducing costs, and enabling greater customization in plastic molding processes. Furthermore, as sustainability concerns intensify and regulatory frameworks evolve, manufacturers will be compelled to adopt greener practices and embrace circular economy principles, reshaping the cost dynamics of plastic molding in the years to come.
Conclusion
In conclusion, plastic molding costs represent a multifaceted realm encompassing various expenses and considerations throughout the manufacturing process. From material selection and design optimization to environmental and social responsibilities, the determinants of plastic molding costs are diverse and interconnected. By understanding these dynamics and embracing innovative strategies, manufacturers can navigate the complexities of plastic molding costs, drive efficiency, and sustain competitiveness in an ever-evolving landscape.
GETTING A QUOTE WITH LK-MOULD IS FREE AND SIMPLE.
FIND MORE OF OUR SERVICES:
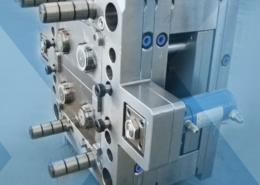
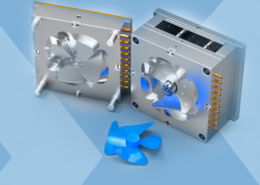
Plastic Molding
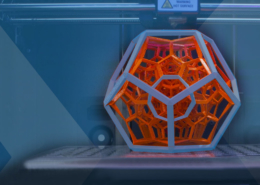
Rapid Prototyping
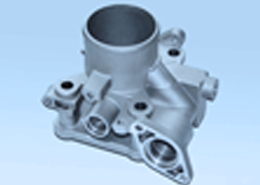
Pressure Die Casting
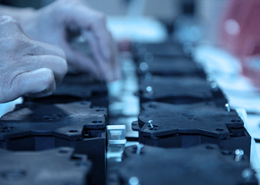
Parts Assembly
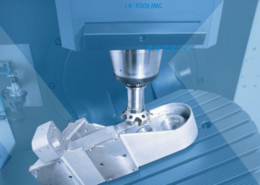