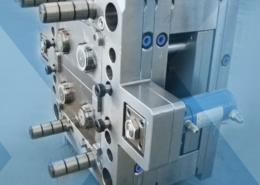
Plastic Molding: Revolutionizing Manufacturing
Author:gly Date: 2024-06-08
Plastic molding stands as a cornerstone in modern manufacturing, revolutionizing industries with its versatility, efficiency, and cost-effectiveness. This article delves into the intricacies of plastic molding, exploring its various facets and its profound impact on contemporary production processes.
Introduction: Unveiling the Magic of Plastic Molding
Plastic molding, an engineering marvel, encompasses a diverse set of manufacturing techniques aimed at shaping molten plastic into a desired form. From simple household items to complex automotive components, plastic molding serves as the backbone of numerous industries worldwide.
Historical Perspective
The genesis of plastic molding traces back to the mid-19th century, marked by the invention of the first injection molding machine by John Wesley Hyatt in 1872. Since then, technological advancements and innovations have propelled plastic molding into the forefront of modern manufacturing.
Process Overview
At its core, plastic molding involves the heating of plastic resin pellets until they liquefy, followed by injecting the molten material into a mold cavity to take on a specific shape. Once cooled and solidified, the molded part is ejected, ready for use or further processing.
Types of Plastic Molding
Plastic molding encompasses a plethora of techniques, each tailored to meet specific requirements and production demands.
Injection Molding
Injection molding reigns supreme as the most widely used plastic molding method, offering unparalleled precision, repeatability, and efficiency. It finds application across diverse industries, from consumer goods to aerospace components.
Blow Molding
Utilized primarily for hollow objects such as bottles and containers, blow molding involves inflating a heated plastic tube within a mold cavity, thus conforming to its shape.
Compression Molding
Compression molding entails the compression of preheated plastic sheets or pellets within a mold cavity, ideal for high-strength, low-volume production runs.
Rotational Molding
Rotational molding, also known as rotomolding, employs rotational movement to evenly distribute molten plastic within a hollow mold, facilitating the production of seamless, stress-free parts.
Advantages of Plastic Molding
The widespread adoption of plastic molding can be attributed to its myriad benefits, driving efficiency, cost-effectiveness, and product innovation.
Design Flexibility
Plastic molding offers unparalleled design freedom, enabling the creation of intricate geometries and complex features that are otherwise unattainable through traditional manufacturing methods.
Cost Efficiency
The mass production capabilities of plastic molding translate into significant cost savings, as it minimizes material wastage and reduces labor costs associated with manual assembly.
Material Versatility
With a vast array of plastic resins available, ranging from commodity polymers to engineering-grade thermoplastics, plastic molding accommodates diverse performance requirements and environmental conditions.
Challenges and Future Outlook
Despite its widespread adoption and undeniable benefits, plastic molding faces certain challenges, including environmental concerns regarding plastic waste and the need for sustainable alternatives.
Sustainability Initiatives
Efforts are underway to develop biodegradable and recyclable plastics, along with implementing eco-friendly manufacturing practices to mitigate the environmental impact of plastic molding.
Technological Advancements
The advent of digital technologies, such as 3D printing and computer-aided design (CAD), continues to revolutionize plastic molding, offering enhanced customization and rapid prototyping capabilities.
Conclusion: Shaping the Future of Manufacturing
In conclusion, plastic molding stands as a testament to human ingenuity, reshaping industries and driving innovation on a global scale. While challenges persist, the relentless pursuit of sustainable practices and technological advancements promises a bright future for plastic molding, cementing its position as a cornerstone of modern manufacturing.
Through its versatility, efficiency, and transformative capabilities, plastic molding remains at the forefront of innovation, heralding a new era of possibilities in the ever-evolving landscape of manufacturing.
GETTING A QUOTE WITH LK-MOULD IS FREE AND SIMPLE.
FIND MORE OF OUR SERVICES:
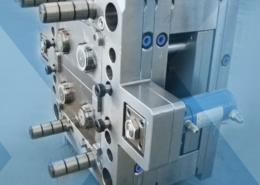
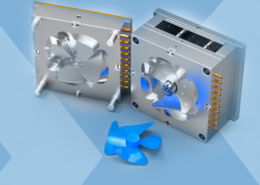
Plastic Molding
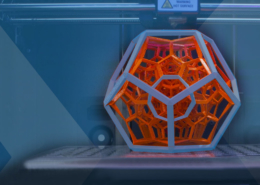
Rapid Prototyping
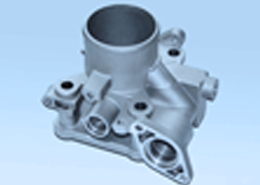
Pressure Die Casting
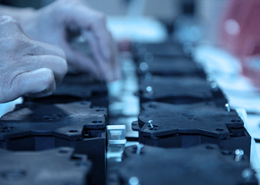
Parts Assembly
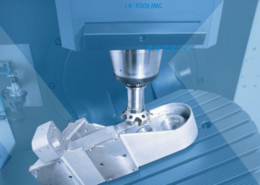