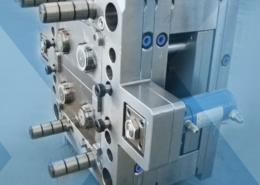
Unveiling the Potential of Plastic Overmolding
Author:gly Date: 2024-06-08
Introduction
Plastic overmolding is a sophisticated manufacturing technique that involves the injection molding of one material over another to create a composite part with enhanced functionality and aesthetics. This process has garnered significant attention in various industries for its ability to produce complex, multi-material components with superior performance characteristics. In this article, we delve into the realm of plastic overmolding, exploring its applications, benefits, challenges, and future prospects.
Unraveling the Applications
Diverse Industrial Applications
Plastic overmolding finds widespread application across diverse industries, including automotive, electronics, medical devices, and consumer goods. In the automotive sector, overmolded parts are utilized for interior trim, handles, and seals, enhancing both aesthetics and functionality. Similarly, in the electronics industry, overmolding is employed to encapsulate sensitive components, providing protection against moisture, shock, and vibration.
Enhancing Product Design
The versatility of plastic overmolding enables designers to create innovative products with unique shapes, textures, and functionalities. By combining different materials with varying properties, such as hardness, flexibility, and color, designers can achieve custom solutions tailored to specific application requirements. This flexibility in product design opens up avenues for creativity and differentiation in the marketplace.
Improving Ergonomics and Comfort
Overmolding offers the advantage of integrating soft-touch or ergonomic features into rigid components, enhancing user comfort and usability. Soft, elastomeric materials can be overmolded onto handle grips, control buttons, and wearable devices, providing a tactile and comfortable interface for users. This capability is particularly valuable in applications where ergonomics and user experience are paramount.
Embracing the Benefits
Enhanced Durability and Performance
The combination of multiple materials in a single overmolded part can result in enhanced durability, resilience, and performance characteristics. By selecting materials with complementary properties, such as strength, chemical resistance, and UV stability, manufacturers can create composite parts that outperform traditional single-material components in demanding environments.
Cost Efficiency and Simplified Assembly
Plastic overmolding offers potential cost savings by consolidating multiple components into a single, integrated part, reducing assembly time, labor costs, and inventory requirements. Additionally, overmolded parts often eliminate the need for secondary operations such as bonding, welding, or fastening, streamlining the manufacturing process and improving overall efficiency.
Design Freedom and Customization
The versatility of plastic overmolding provides designers with unparalleled freedom to create complex geometries, intricate textures, and multi-color patterns in molded parts. This design flexibility enables customization to meet specific branding, aesthetic, or functional requirements, fostering product differentiation and market competitiveness.
Addressing Challenges and Future Directions
Material Compatibility and Adhesion
Achieving strong adhesion between different materials is crucial for the success of plastic overmolding. Challenges may arise due to differences in material properties, thermal expansion coefficients, and surface characteristics. Future research could focus on developing advanced bonding techniques, surface treatments, and compatibilizers to improve interfacial adhesion and durability in overmolded parts.
Process Optimization and Efficiency
Optimizing the overmolding process parameters, such as temperature, pressure, and cycle time, is essential for achieving consistent part quality and minimizing production costs. Advances in process monitoring, automation, and predictive modeling can help optimize process parameters, reduce cycle times, and enhance production efficiency in plastic overmolding.
Sustainability and Material Innovation
Incorporating sustainable materials and eco-friendly manufacturing practices is an emerging trend in the field of plastic overmolding. Researchers are exploring bio-based polymers, recycled plastics, and biodegradable additives as alternatives to conventional materials, aiming to reduce environmental impact and meet evolving regulatory requirements.
Conclusion
Plastic overmolding represents a convergence of innovation, design, and manufacturing excellence, offering a myriad of opportunities for product enhancement and differentiation across diverse industries. By harnessing the benefits of overmolding, manufacturers can create high-performance, customized parts that meet the evolving demands of the market. As the industry continues to evolve, addressing challenges, embracing innovation, and fostering collaboration will be essential for unlocking the full potential of plastic overmolding in the future.
Future Perspectives
Future research endeavors could focus on advancing material science, process optimization techniques, and sustainability initiatives to further expand the capabilities and applications of plastic overmolding. Additionally, interdisciplinary collaboration between material scientists, engineers, and designers could lead to breakthroughs in composite material development, surface engineering, and additive manufacturing techniques, paving the way for a more sustainable and innovative approach to plastic overmolding.
GETTING A QUOTE WITH LK-MOULD IS FREE AND SIMPLE.
FIND MORE OF OUR SERVICES:
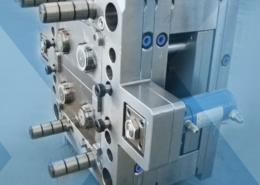
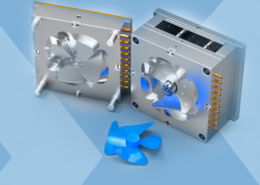
Plastic Molding
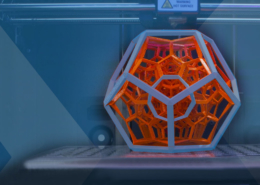
Rapid Prototyping
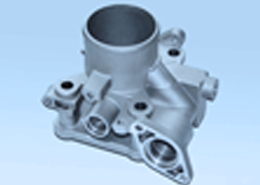
Pressure Die Casting
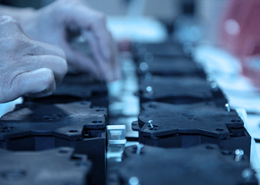
Parts Assembly
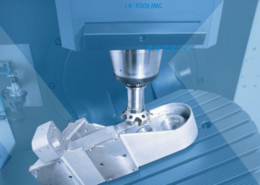