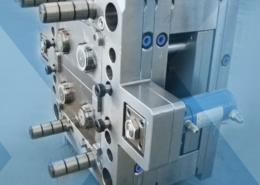
Exploring the World of Plastic Press Molding
Author:gly Date: 2024-06-08
Plastic press molding, a pivotal process in modern manufacturing, offers a fascinating intersection of innovation and practicality. Originating from the necessity to efficiently produce plastic components, this method has evolved into a cornerstone of various industries, from automotive to electronics. In this article, we delve into the intricacies of plastic press molding, unraveling its mechanisms, applications, challenges, and future prospects.
The Basics
Plastic press molding, also known as compression molding, involves the shaping of plastic materials through the application of heat and pressure. It operates on the principle of forcing molten plastic into a pre-designed mold cavity, where it solidifies and takes the desired shape upon cooling. This method stands distinguished for its versatility, accommodating a wide range of thermoplastic and thermosetting materials. With its roots tracing back to the early 20th century, plastic press molding has undergone significant advancements, refining its precision and efficiency.
The process begins with the preparation of raw materials, which are typically in the form of pellets, powders, or preforms. These materials are loaded into the molding machine, where they undergo heating and compression within the mold cavity. The mold, often crafted from steel or aluminum, defines the final geometry of the product. Once the plastic material conforms to the mold's contours, it undergoes cooling, enabling the solidification of the desired shape. The resultant product is then ejected from the mold, ready for further finishing or assembly.
Applications
The versatility of plastic press molding renders it indispensable across a spectrum of industries. In the automotive sector, it finds widespread use in the fabrication of interior components, exterior panels, and engine parts. Its ability to produce intricate shapes with high structural integrity makes it an ideal choice for aerospace applications, where lightweight yet durable components are paramount. Moreover, the electronics industry leverages plastic press molding for manufacturing casings, connectors, and circuit board components, owing to its cost-effectiveness and scalability.
Beyond these traditional domains, plastic press molding has found novel applications in emerging fields such as biomedical engineering and renewable energy. In the medical sector, it facilitates the production of surgical instruments, implantable devices, and diagnostic equipment. Similarly, in the realm of renewable energy, it contributes to the manufacturing of solar panels, wind turbine components, and energy storage systems. This diversification underscores the adaptability and enduring relevance of plastic press molding in an ever-evolving industrial landscape.
Challenges and Innovations
Despite its widespread adoption, plastic press molding is not without its challenges. One primary concern is achieving uniformity and consistency in product quality, especially with complex geometries and thin-walled parts. Variations in material properties, mold design, and processing parameters can lead to defects such as voids, warpage, and sink marks. Addressing these challenges necessitates continuous innovation in materials science, mold technology, and process optimization.
Recent advancements in computational modeling and simulation have revolutionized the design and optimization of plastic press molding processes. Finite element analysis (FEA) enables engineers to predict flow patterns, temperature distributions, and stress concentrations within the mold cavity, thereby optimizing parameters for enhanced product quality and production efficiency. Furthermore, the integration of sensor technologies and real-time monitoring systems allows for precise control and adjustment of process variables, minimizing defects and maximizing yield.
Future Directions
Looking ahead, the future of plastic press molding holds promise for further breakthroughs and refinements. The convergence of additive manufacturing techniques, such as 3D printing, with traditional molding processes opens new avenues for rapid prototyping and customized production. Moreover, the quest for sustainable materials and environmentally friendly processes drives research into bio-based polymers, recycled plastics, and energy-efficient molding technologies. Embracing these innovations fosters a greener, more agile manufacturing ecosystem, poised to meet the evolving needs of society while minimizing environmental impact.
In conclusion, plastic press molding stands as a testament to human ingenuity and engineering prowess, serving as a linchpin of modern manufacturing across diverse industries. Its evolution from a rudimentary process to a sophisticated technology underscores its enduring relevance and adaptability in an ever-changing landscape. By addressing challenges, fostering innovation, and embracing emerging trends, the realm of plastic press molding continues to chart new frontiers, poised for a future defined by excellence and sustainability.
GETTING A QUOTE WITH LK-MOULD IS FREE AND SIMPLE.
FIND MORE OF OUR SERVICES:
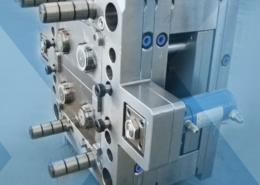
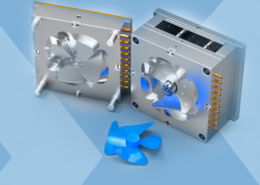
Plastic Molding
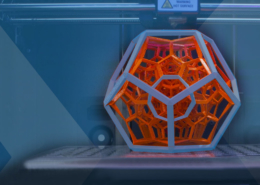
Rapid Prototyping
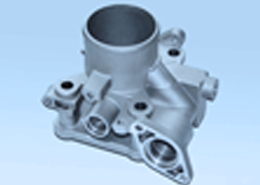
Pressure Die Casting
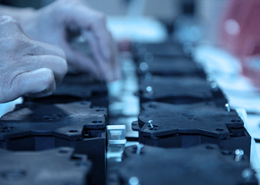
Parts Assembly
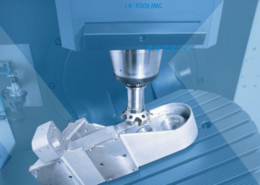