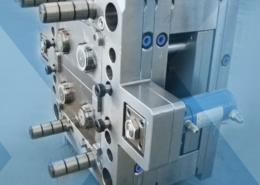
Precision Plastic Molding: Revolutionizing Manufacturing
Author:gly Date: 2024-06-08
Precision plastic molding stands at the forefront of modern manufacturing, offering unparalleled precision, efficiency, and versatility. In this comprehensive exploration, we delve into the intricacies of precision plastic molding, from its fundamental principles to its diverse applications across industries.
Evolution of Precision Plastic Molding
Precision plastic molding has undergone a remarkable evolution since its inception. Initially developed as a method for producing simple plastic components, it has evolved into a sophisticated process capable of creating intricate and complex shapes with utmost accuracy. Advancements in materials science, computer-aided design (CAD), and automation have propelled precision plastic molding into a cornerstone of modern manufacturing.
Historical Perspective
The roots of precision plastic molding can be traced back to the mid-20th century, with the invention of injection molding—a technique that revolutionized the production of plastic parts. Over the decades, continuous innovation and refinement have expanded the capabilities of precision plastic molding, enabling manufacturers to meet the demands of increasingly complex designs and stringent quality standards.
Technological Advancements
The integration of advanced technologies such as computer numerical control (CNC) machining, robotics, and real-time monitoring systems has further enhanced the precision and efficiency of plastic molding processes. These technological advancements have not only optimized production workflows but also enabled greater customization and flexibility in manufacturing.
Key Principles of Precision Plastic Molding
At its core, precision plastic molding relies on several key principles to achieve consistent and high-quality results. Understanding these principles is essential for optimizing the manufacturing process and ensuring the integrity of the final products.
Material Selection
The choice of plastic material plays a critical role in precision plastic molding. Factors such as thermal stability, mechanical properties, and chemical resistance must be carefully considered to ensure compatibility with the intended application. Additionally, the material's flow characteristics and shrinkage behavior influence the design of mold cavities and gating systems.
Mold Design and Fabrication
The design and fabrication of molds are pivotal in achieving precise and repeatable molding outcomes. Utilizing CAD software and advanced machining techniques, mold designers can create intricate geometries with tight tolerances. Furthermore, the selection of mold materials and surface treatments affects part quality, mold longevity, and production efficiency.
Process Optimization
Optimizing process parameters such as temperature, pressure, injection speed, and cooling time is crucial for maximizing efficiency and minimizing defects. Advanced simulation tools allow manufacturers to analyze and optimize the molding process before production, reducing trial and error and accelerating time-to-market.
Applications Across Industries
Precision plastic molding finds application across a myriad of industries, ranging from automotive and aerospace to healthcare and consumer electronics. Its ability to produce complex geometries with tight tolerances makes it indispensable for manufacturing components and products with high performance and reliability.
Automotive Industry
In the automotive sector, precision plastic molding is utilized for producing interior and exterior components, under-the-hood parts, and structural elements. Lightweight yet durable plastic components contribute to fuel efficiency, vehicle safety, and design aesthetics.
Medical Devices
The medical device industry relies on precision plastic molding for manufacturing surgical instruments, diagnostic equipment, and implantable devices. Biocompatible materials and strict quality control measures ensure the safety and efficacy of medical products, meeting regulatory requirements and patient needs.
Electronics and Consumer Goods
In the realm of electronics and consumer goods, precision plastic molding enables the production of miniature components, enclosures, and connectors. High-precision molding processes facilitate the integration of electronic functionalities while maintaining compact designs and aesthetic appeal.
Conclusion: Shaping the Future of Manufacturing
In conclusion, precision plastic molding represents a paradigm shift in modern manufacturing, offering unmatched precision, efficiency, and versatility across diverse industries. By leveraging advanced technologies and adhering to rigorous quality standards, manufacturers can unlock new opportunities for innovation and competitiveness. As we look to the future, continued research and development in materials science, process optimization, and sustainable practices will further propel the evolution of precision plastic molding, shaping the landscape of manufacturing for generations to come.
GETTING A QUOTE WITH LK-MOULD IS FREE AND SIMPLE.
FIND MORE OF OUR SERVICES:
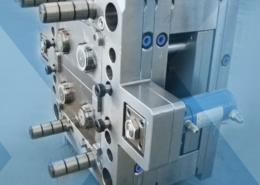
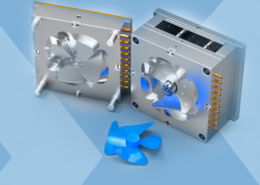
Plastic Molding
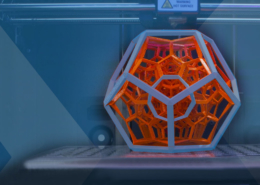
Rapid Prototyping
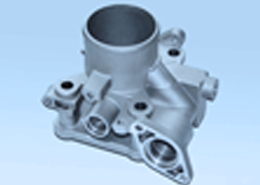
Pressure Die Casting
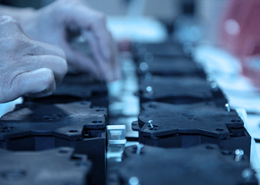
Parts Assembly
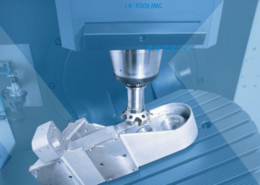