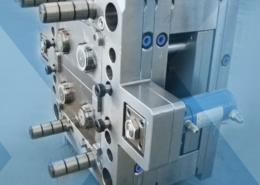
Exploring the Advancements in Rapid Injection Molds
Author:gly Date: 2024-06-08
Rapid injection molds have emerged as a game-changer in the field of manufacturing, offering accelerated production cycles, reduced costs, and enhanced design flexibility. This article delves into the intricacies of rapid injection molds, from their inception to their widespread applications and future prospects, providing readers with a comprehensive understanding of this innovative technology.
Introduction to Rapid Injection Molds
Rapid injection molds, also known as rapid tooling or rapid prototyping molds, revolutionize the traditional injection molding process by expediting the design iteration and production phases. These molds enable manufacturers to quickly and cost-effectively produce prototype parts and low-volume production runs, facilitating rapid product development and market entry.
Advantages of Rapid Injection Molds
Rapid injection molds offer numerous advantages, including:
Speed
: Rapid molds significantly reduce lead times compared to conventional tooling methods, allowing for quick turnaround from design to production.
Cost-Effectiveness
: By eliminating the need for expensive tooling and setup costs associated with traditional molds, rapid injection molds lower the barrier to entry for new product development.
Design Flexibility
: Rapid molds facilitate design iteration and optimization, enabling engineers to quickly test multiple iterations and make adjustments as needed.
Low-Volume Production
: Rapid molds are ideal for producing small quantities of parts for market testing, validation, or niche markets, without the high upfront costs of traditional tooling.
Technological Innovations
Technological advancements play a crucial role in the evolution of rapid injection molds. Key innovations include:
Advanced Materials
: The development of high-performance thermoplastics and composite materials expands the range of applications for rapid injection molding, allowing for the production of functional prototypes and end-use parts with superior mechanical properties.
Additive Manufacturing Integration
: Integration with additive manufacturing technologies such as 3D printing enables the rapid fabrication of mold inserts and tooling components, further reducing lead times and enhancing design freedom.
Simulation and Optimization Software
: Simulation software allows engineers to predict and optimize mold performance, reducing the need for physical testing and iteration cycles.
Applications of Rapid Injection Molds
Rapid injection molds find applications across various industries, including:
Product Development
: Rapid molds facilitate rapid prototyping and iteration during the product development phase, enabling designers to validate concepts and refine designs before full-scale production.
Customized Manufacturing
: Rapid molds are ideal for producing customized or low-volume parts for niche markets, allowing manufacturers to meet specific customer requirements without incurring high tooling costs.
Medical Devices
: The medical industry benefits from rapid injection molds for producing prototypes and low-volume production of medical devices and components, where speed and flexibility are paramount.
Challenges and Future Directions
Despite their advantages, rapid injection molds face challenges such as:
Material Limitations
: Some materials may not be suitable for rapid injection molding due to their processing requirements or performance characteristics.
Surface Finish
: Achieving high-quality surface finishes and dimensional accuracy can be challenging with rapid molds, especially for complex geometries.
Future research directions in rapid injection molding include:
Material Development
: Continued research into advanced materials and processing techniques will expand the capabilities of rapid injection molding and improve part quality.
Process Optimization
: Optimization of process parameters and mold design will further enhance the speed, efficiency, and reliability of rapid injection molding technologies.
In conclusion, rapid injection molds represent a paradigm shift in the field of manufacturing, offering speed, flexibility, and cost-effectiveness for product development and low-volume production. By leveraging technological innovations and addressing challenges, rapid injection molding continues to pave the way for faster, more efficient, and more agile manufacturing processes.
GETTING A QUOTE WITH LK-MOULD IS FREE AND SIMPLE.
FIND MORE OF OUR SERVICES:
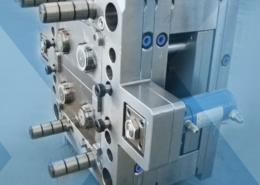
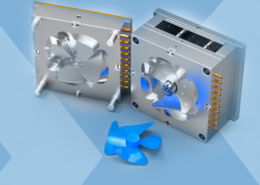
Plastic Molding
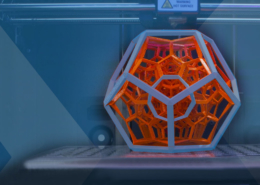
Rapid Prototyping
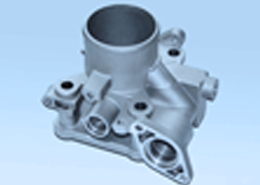
Pressure Die Casting
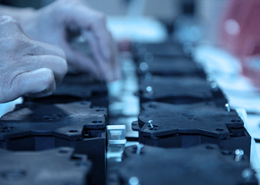
Parts Assembly
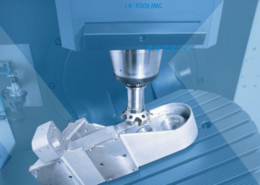