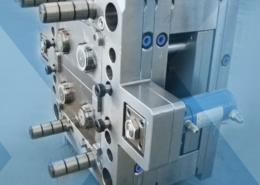
Exploring the Art of Thin Wall Moulding: Precision in Plastics
Author:gly Date: 2024-06-08
Thin wall moulding stands at the intersection of art and engineering, offering a fascinating glimpse into the world of precision plastic manufacturing. This article aims to unravel the complexities of thin wall moulding, offering insights into its techniques, applications, challenges, and future directions.
Introduction to Thin Wall Moulding
Thin wall moulding represents a specialized injection moulding technique used to produce plastic parts with exceptionally thin walls and high precision. This process involves injecting molten plastic into intricate moulds with thin cross-sections, resulting in lightweight yet durable components. Thin wall moulding finds applications across various industries, including packaging, automotive, electronics, and medical devices, where lightweight, high-strength components are desired.
Techniques and Considerations
Achieving success in thin wall moulding requires a combination of advanced mould design, material selection, and process optimization. Techniques such as rapid cooling, high injection speeds, and precise control of melt temperature and pressure are essential to ensure uniform filling of the mould cavity and prevent defects such as sink marks, warpage, and dimensional inaccuracies. Additionally, considerations such as gate design, wall thickness distribution, and material flow dynamics play a crucial role in achieving optimal part quality and performance.
Applications Across Industries
Thin wall moulding finds extensive applications in industries where lightweight, high-strength components are required. In the packaging industry, thin wall moulding enables the production of thin-walled containers, lids, and closures that offer superior strength-to-weight ratios and enhanced product protection. In the automotive sector, thin wall moulding is used to manufacture lightweight, fuel-efficient components such as interior panels, trim pieces, and under-the-hood components. Similarly, in the electronics and medical device industries, thin wall moulding enables the production of compact, lightweight components with intricate geometries and tight tolerances.
Challenges and Future Directions
Despite its advantages, thin wall moulding presents several challenges, including maintaining part quality, minimizing cycle times, and optimizing material usage. Future research and development efforts in thin wall moulding are expected to focus on advancements in mould design, material science, and process optimization. Techniques such as in-mould sensing, advanced cooling technologies, and real-time process monitoring are anticipated to enhance the efficiency, reliability, and sustainability of thin wall moulding processes.
Conclusion
In conclusion, thin wall moulding represents a pinnacle of precision engineering and craftsmanship in the realm of plastic manufacturing. Its ability to produce lightweight, high-strength components with intricate geometries and tight tolerances makes it indispensable across a myriad of industries. As we venture into the future, continued innovation and advancements in thin wall moulding technology hold the promise of unlocking new possibilities, pushing the boundaries of what is achievable in precision plastic manufacturing.
GETTING A QUOTE WITH LK-MOULD IS FREE AND SIMPLE.
FIND MORE OF OUR SERVICES:
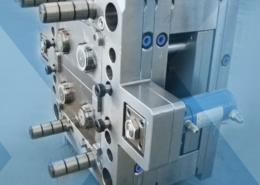
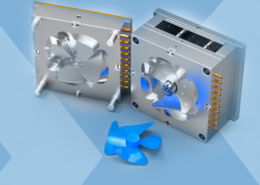
Plastic Molding
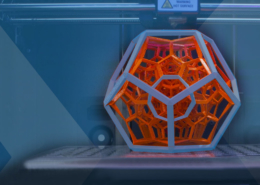
Rapid Prototyping
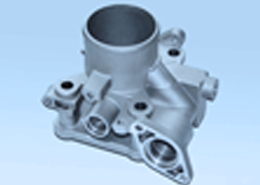
Pressure Die Casting
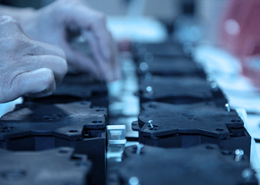
Parts Assembly
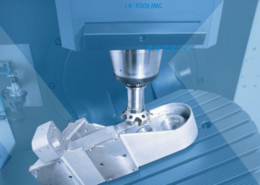