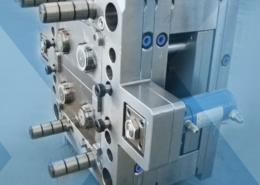
Injection Molding of Medical Plastics: Revolutionizing Healthcare
Author:gly Date: 2024-06-08
Introduction
The utilization of injection molding in the production of medical plastics has revolutionized healthcare in recent decades. This manufacturing process, characterized by its efficiency and precision, plays a pivotal role in the creation of various medical devices and components, ranging from syringes to complex surgical instruments. This article delves into the multifaceted aspects of injection molding medical plastics, elucidating its significance, applications, advancements, and future prospects.
Applications in Medical Devices
Enhancing Patient Care
Injection molding facilitates the production of medical devices with superior precision, durability, and biocompatibility, ensuring optimal patient care. Devices such as catheters, respiratory masks, and implantable components are manufactured with intricate designs and stringent quality standards, contributing to improved treatment outcomes and patient comfort.
Addressing Complex Healthcare Needs
The versatility of injection molding allows for the creation of customized medical devices tailored to meet specific healthcare requirements. From orthopedic implants to diagnostic equipment, the adaptability of this manufacturing process enables the development of innovative solutions to address complex medical conditions, fostering advancements in treatment modalities.
Ensuring Safety and Reliability
With stringent regulatory standards governing the medical industry, injection molding plays a pivotal role in ensuring the safety and reliability of medical devices. Through meticulous quality control measures and material selection, manufacturers uphold the highest standards of product efficacy, minimizing risks associated with device malfunction or contamination.
Technological Advancements
Integration of Additive Manufacturing
The integration of additive manufacturing techniques, such as 3D printing, with injection molding has revolutionized the production of medical plastics. This hybrid approach enables the creation of intricate geometries and patient-specific designs, enhancing the functionality and performance of medical devices while streamlining the manufacturing process.
Development of Advanced Materials
Ongoing research and development efforts have led to the emergence of advanced materials tailored for medical applications. Biocompatible polymers, antimicrobial additives, and bioresorbable compounds are among the innovations driving the evolution of injection molding in healthcare, expanding the scope of possibilities for medical device manufacturers.
Implementation of Smart Manufacturing
The adoption of smart manufacturing technologies, including IoT-enabled sensors and data analytics, optimizes the injection molding process in real-time. By monitoring key parameters such as temperature, pressure, and cycle time, manufacturers can enhance productivity, minimize defects, and ensure consistent product quality, thereby meeting the dynamic demands of the healthcare industry.
Challenges and Future Directions
Regulatory Compliance
Navigating the regulatory landscape poses challenges for manufacturers seeking to introduce new materials and technologies in medical device production. Striking a balance between innovation and compliance remains paramount, necessitating collaboration between industry stakeholders, regulatory agencies, and healthcare professionals to ensure the safe and effective deployment of injection molding in healthcare.
Sustainability and Environmental Impact
Addressing concerns related to plastic waste and environmental sustainability presents an ongoing challenge for the medical industry. As the demand for single-use medical devices continues to rise, efforts to develop biodegradable materials and implement recycling initiatives are imperative to mitigate the environmental footprint associated with injection molding processes.
Integration of Advanced Manufacturing Techniques
The convergence of injection molding with emerging manufacturing techniques, such as microfluidics and nanotechnology, holds promise for the development of next-generation medical devices. By leveraging these technologies, manufacturers can enhance the functionality, performance, and miniaturization of medical devices, opening new avenues for personalized medicine and point-of-care diagnostics.
Conclusion
In conclusion, injection molding of medical plastics stands at the forefront of innovation in healthcare, driving advancements in medical device manufacturing, materials science, and smart manufacturing technologies. By addressing complex healthcare needs, ensuring product safety and reliability, and embracing technological innovations, injection molding continues to shape the future of healthcare delivery. Moving forward, collaborative efforts aimed at overcoming regulatory challenges, promoting sustainability, and integrating advanced manufacturing techniques are essential to unlock the full potential of injection molding in improving patient outcomes and advancing global healthcare initiatives.
GETTING A QUOTE WITH LK-MOULD IS FREE AND SIMPLE.
FIND MORE OF OUR SERVICES:
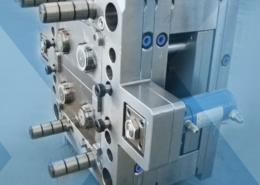
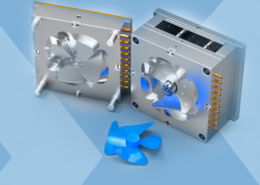
Plastic Molding
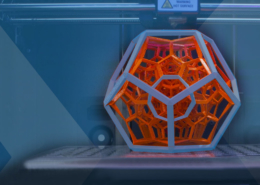
Rapid Prototyping
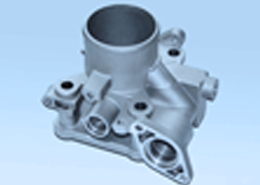
Pressure Die Casting
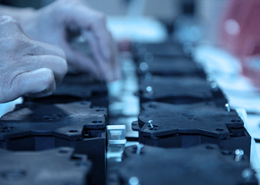
Parts Assembly
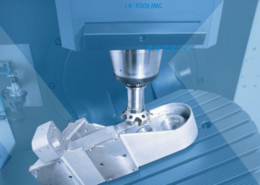