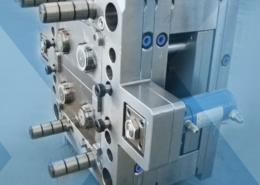
Injection Molding: Revolutionizing Manufacturing Processes
Author:gly Date: 2024-06-08
Injection molding stands as a cornerstone in modern manufacturing, revolutionizing industries by enabling efficient mass production of complex plastic parts. Its significance permeates various sectors, from automotive to consumer goods, owing to its versatility, precision, and cost-effectiveness.
Introduction to Injection Molding
Injection molding, a manufacturing process for producing parts by injecting molten material into a mold, traces its roots back to the mid-19th century. Since then, it has undergone significant advancements, becoming the preferred method for manufacturing intricate components with high accuracy and consistency.
Process Overview
Molten Material Injection
The process initiates with the feeding of raw material, usually thermoplastic or thermosetting polymers, into a heated barrel. The material is then liquefied and injected into a mold cavity under high pressure.
Mold Cavity Filling
Once injected, the molten material fills the mold cavity, taking its shape. The cavity design is meticulously crafted to ensure precise replication of the desired part geometry.
Cooling and Solidification
After filling the cavity, the molten material undergoes rapid cooling, solidifying into the desired shape. Proper cooling is crucial to achieve the desired part properties and minimize cycle time.
Ejection of Finished Part
Once solidified, the finished part is ejected from the mold, ready for further processing or assembly. Ejection mechanisms vary depending on the complexity of the part and the mold design.
Advantages
High Efficiency
Injection molding offers unparalleled efficiency, enabling high-volume production of parts with minimal waste. The ability to produce multiple parts simultaneously further enhances productivity.
Cost-effectiveness
Despite initial setup costs, injection molding proves cost-effective in the long run, particularly for large production runs. The automated nature of the process reduces labor costs and ensures consistent part quality.
Design Flexibility
The process accommodates a wide range of part designs, from simple to highly intricate geometries. With advanced mold technologies, manufacturers can achieve complex shapes and features with exceptional precision.
Material Versatility
Injection molding supports a plethora of materials, including various thermoplastics, thermosets, elastomers, and even metals. This versatility enables manufacturers to select materials tailored to specific application requirements.
Challenges and Innovations
Tooling Complexity
Designing and fabricating molds for injection molding can be intricate and time-consuming, particularly for complex parts. However, advancements in mold-making technologies, such as additive manufacturing, mitigate these challenges.
Material Selection
Choosing the right material is critical for part performance and durability. Innovations in material science continue to expand the range of materials compatible with injection molding, offering enhanced properties and sustainability.
Sustainability Concerns
The reliance on plastic materials in injection molding has raised concerns regarding environmental sustainability. To address this, manufacturers are exploring biodegradable and recycled materials, as well as optimizing processes to minimize waste.
Conclusion
In conclusion, injection molding stands as a pivotal process in modern manufacturing, driving innovation and efficiency across diverse industries. Its ability to produce intricate parts with high precision, coupled with cost-effectiveness and design flexibility, positions it as a cornerstone of mass production. While challenges persist, ongoing advancements in materials, technology, and sustainability initiatives promise to further enhance the capabilities and sustainability of injection molding. Embracing these innovations will undoubtedly shape the future of manufacturing, paving the way for more sustainable and efficient production processes.
In essence, injection molding embodies the convergence of precision engineering, material science, and innovation, underpinning the manufacturing landscape of the 21st century.
GETTING A QUOTE WITH LK-MOULD IS FREE AND SIMPLE.
FIND MORE OF OUR SERVICES:
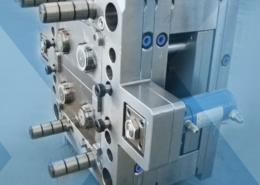
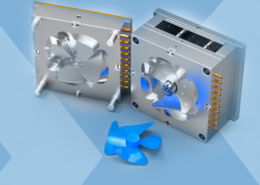
Plastic Molding
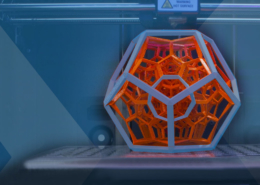
Rapid Prototyping
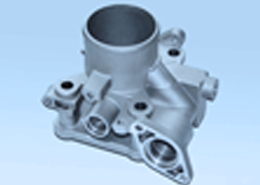
Pressure Die Casting
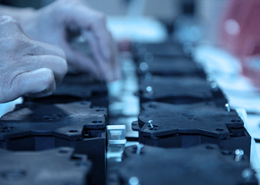
Parts Assembly
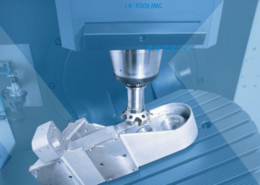