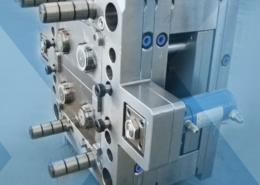
Unveiling the Economics of Injection Moulding Mould Cost: Exploring Factors, Str
Author:gly Date: 2024-06-08
Injection moulding mould cost stands as a pivotal consideration in the realm of manufacturing, exerting profound influences on product viability, production efficiency, and overall profitability. As industries increasingly turn to injection moulding for its versatility and scalability, understanding the intricacies of mould cost dynamics becomes imperative. This article embarks on a comprehensive exploration of injection moulding mould cost, delving into its determinants, optimization strategies, market dynamics, and implications.
The Significance of Injection Moulding Mould Cost
Injection moulding mould cost serves as a cornerstone in manufacturing, encapsulating the expenses associated with tooling, equipment, and materials required for producing plastic components. The upfront investment in moulds constitutes a significant portion of the total production cost, exerting a profound impact on the overall economics of injection moulding operations. Therefore, understanding the factors influencing mould cost and implementing cost-effective strategies are essential for ensuring competitiveness and sustainability in the marketplace.
Determinants of Injection Moulding Mould Cost
The cost of injection moulding moulds is shaped by a myriad of factors, each exerting varying degrees of influence on the overall expense. Material selection, mould complexity, production volume, and mould lifespan emerge as pivotal determinants that warrant meticulous consideration.
Material Selection:
The choice of mould material significantly impacts mould cost, with considerations such as durability, heat resistance, and machinability influencing material selection. High-quality tool steels and advanced alloys command higher prices but offer superior performance and longevity, thereby yielding long-term cost savings.
Mould Complexity:
The intricacy of part geometry directly correlates with mould complexity and, consequently, cost. Simple moulds with straightforward geometries entail lower fabrication costs, whereas complex moulds with undercuts, side actions, and intricate features necessitate specialized machining processes and increased labour hours, driving up expenses.
Production Volume:
Economies of scale play a pivotal role in mould cost, with higher production volumes enabling the amortization of fixed expenses over a larger output, thereby reducing the cost per part. Conversely, low-volume production incurs higher per-unit mould costs due to the inability to leverage scale advantages.
Mould Lifespan:
The durability and longevity of injection moulds directly impact their cost-effectiveness over the lifecycle. Investing in high-quality mould materials, implementing preventive maintenance protocols, and adhering to proper operating practices prolong mould lifespan, thereby amortizing upfront costs and minimizing the need for frequent replacements.
Optimization Strategies for Mould Cost Reduction
Maximizing the efficiency and cost-effectiveness of injection moulding operations necessitates the adoption of optimization strategies throughout the mould lifecycle. From design optimization and material selection to maintenance protocols and mould refurbishment, each stage presents opportunities to mitigate costs and enhance performance.
Design Optimization:
Collaborating with design engineers to optimize part designs for manufacturability can streamline moulding processes, minimize material wastage, and reduce tooling costs. Design considerations such as draft angles, wall thickness uniformity, and gating locations can significantly impact mould complexity and cost.
Material Selection:
Careful evaluation of mould material properties and performance requirements enables informed decisions that balance cost considerations with durability and longevity. Utilizing advanced materials such as tool steels, beryllium copper, or high-performance alloys can enhance mould longevity and reduce lifecycle costs.
Maintenance Protocols:
Implementing proactive maintenance schedules, including regular cleaning, lubrication, and inspection, preserves mould integrity, mitigates wear and tear, and prolongs lifespan. Addressing minor issues promptly prevents costly repairs or replacements and ensures uninterrupted production operations.
Mould Refurbishment:
Engaging in periodic mould refurbishment or refurbishing worn-out mould components can extend mould lifespan and enhance cost-effectiveness. Surface treatments, such as nitriding or coatings, can improve wear resistance and minimize friction, thereby reducing maintenance requirements and enhancing productivity.
Market Dynamics and Implications
The injection moulding market is characterized by dynamic shifts influenced by technological advancements, market demand fluctuations, and competitive pressures. Understanding market dynamics and trends enables stakeholders to adapt strategies, mitigate risks, and capitalize on emerging opportunities.
Technological Advancements:
Advancements in mould design software, simulation tools, and additive manufacturing techniques have revolutionized the injection moulding landscape, offering unprecedented capabilities for design optimization, rapid prototyping, and cost-effective production.
Market Demand Fluctuations:
Fluctuations in market demand, driven by economic cycles, consumer trends, and regulatory changes, impact mould cost dynamics and production volumes. Flexibility, agility, and responsiveness to market fluctuations are essential for maintaining competitiveness and profitability.
Competitive Pressures:
Intensifying competition, globalization, and commoditization exert downward pressure on mould prices, necessitating cost optimization strategies and differentiation to maintain profitability. Embracing lean manufacturing principles, fostering innovation, and cultivating strategic partnerships can confer a competitive edge amidst market challenges.
Conclusion: Navigating the Dynamics of Injection Moulding Mould Cost
In conclusion, injection moulding mould cost represents a critical component of manufacturing economics, exerting significant influence on product viability, production efficiency, and market competitiveness. By understanding the determinants, optimization strategies, and market implications surrounding mould cost, stakeholders can navigate the complexities of injection moulding operations with foresight and agility. As industries continue to evolve and innovate, ongoing research, investment in advanced technologies, and collaboration across the supply chain will be pivotal in driving cost-effective solutions, enhancing competitiveness, and shaping the future trajectory of injection moulding.
GETTING A QUOTE WITH LK-MOULD IS FREE AND SIMPLE.
FIND MORE OF OUR SERVICES:
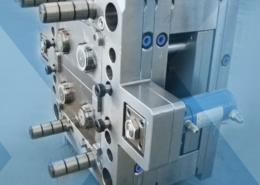
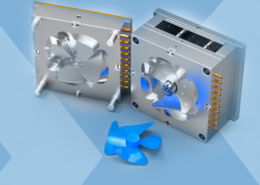
Plastic Molding
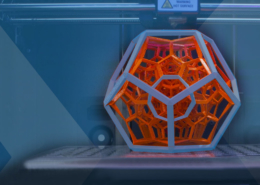
Rapid Prototyping
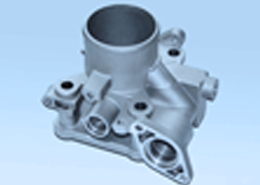
Pressure Die Casting
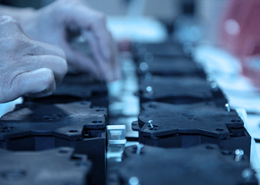
Parts Assembly
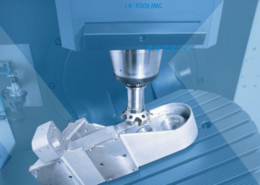