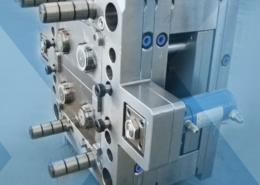
Exploring the Realm of Injection Parts: Precision and Innovation in Manufacturin
Author:gly Date: 2024-06-08
Injection parts are integral components of countless products that shape our daily lives, from the intricate components of electronics to the durable casings of automotive components. As such, understanding the intricacies of injection parts not only piques curiosity but also offers insights into the sophisticated world of manufacturing. In this article, we delve into the realm of injection parts, unraveling their significance, manufacturing processes, and impact on various industries.
Unveiling Injection Parts
The Essence of Injection Parts
Injection parts, also known as molded parts, are manufactured through the injection molding process, wherein molten material is injected into a mold cavity, cooled, and solidified to form the desired shape. This versatile manufacturing technique enables the production of complex geometries with high precision and repeatability, making injection parts indispensable in a wide range of applications.
Applications Across Industries
Injection parts find applications across diverse industries, including automotive, electronics, healthcare, consumer goods, and more. From automotive components such as interior trim panels and exterior body parts to medical devices such as syringes and IV catheters, injection-molded parts play a pivotal role in enhancing functionality, durability, and aesthetics in various products.
Key Considerations in Injection Part Manufacturing
Material Selection
The choice of material is a critical consideration in injection part manufacturing, as it directly impacts the performance, durability, and cost-effectiveness of the final product. Factors such as mechanical properties, chemical resistance, thermal stability, and aesthetic requirements influence material selection decisions. Common materials used in injection molding include thermoplastics, thermosets, elastomers, and composites, each offering unique advantages and limitations.
Design Optimization
Design optimization is essential to maximize the efficiency and functionality of injection-molded parts. Leveraging computer-aided design (CAD) software, engineers can create intricate geometries and optimize part designs for manufacturability, minimizing material waste and production costs. Considerations such as draft angles, wall thickness uniformity, gating and venting, and part consolidation are integral to achieving optimal part performance and quality.
Advancements in Injection Part Manufacturing
Industry 4.0 Integration
The integration of digital technologies and Industry 4.0 principles is revolutionizing injection part manufacturing, enabling real-time monitoring, predictive maintenance, and data-driven decision-making. Smart injection molding systems equipped with sensors, connectivity, and analytics capabilities optimize production processes, enhance quality control, and improve overall efficiency, driving continuous improvement and innovation in the industry.
Advanced Materials and Additive Manufacturing
Advancements in materials science and additive manufacturing technologies are expanding the horizons of injection part manufacturing. From biodegradable polymers and recycled materials to advanced ceramics and metal alloys, a diverse range of materials are now accessible for injection molding applications, offering enhanced performance, sustainability, and customization possibilities. Additive manufacturing techniques such as 3D printing complement traditional injection molding processes, enabling rapid prototyping, on-demand production, and complex geometries that were previously unattainable.
Conclusion: Navigating the Future of Injection Part Manufacturing
In conclusion, injection parts represent a cornerstone of modern manufacturing, driving innovation, efficiency, and quality across diverse industries. As technologies continue to evolve and market demands evolve, the injection molding industry must adapt and innovate to meet the challenges and opportunities that lie ahead. By embracing advancements in materials, design, and manufacturing processes, injection molding companies can unlock new possibilities and redefine the future of injection part manufacturing. Through collaboration, research, and a commitment to excellence, the injection molding industry is poised to shape a more resilient, sustainable, and innovative future for generations to come.
GETTING A QUOTE WITH LK-MOULD IS FREE AND SIMPLE.
FIND MORE OF OUR SERVICES:
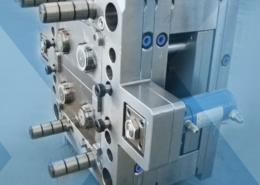
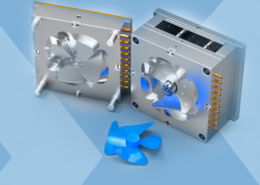
Plastic Molding
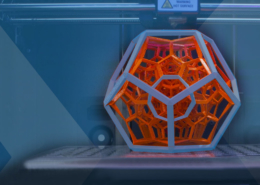
Rapid Prototyping
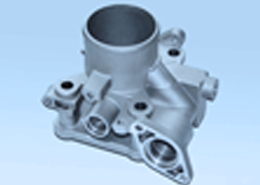
Pressure Die Casting
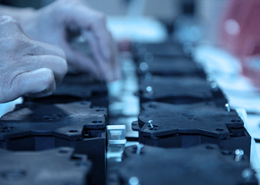
Parts Assembly
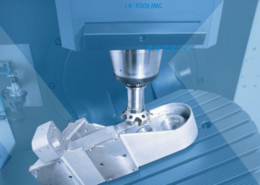