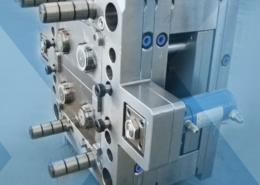
Exploring Kilang Plastic Injection Moulding
Author:gly Date: 2024-06-08
Introduction: Unveiling a Hub of Innovation
Kilang plastic injection moulding serves as a dynamic hub of innovation, where precision engineering meets cutting-edge technology to shape the future of manufacturing. Nestled within industrial landscapes, kilang plastic injection moulding facilities are centers of excellence, driving advancements in product design, production efficiency, and material sustainability. In this article, we embark on a journey to unravel the intricacies of kilang plastic injection moulding, exploring its significance, capabilities, applications, and future prospects.
1. Precision Engineering at its Core
At the heart of kilang plastic injection moulding lies a commitment to precision engineering, where every component, from mould design to machine calibration, is meticulously crafted to exacting specifications. The process begins with the creation of a mould cavity, typically made from hardened steel or aluminum, which serves as the negative impression of the desired plastic part.
Advanced CAD/CAM software enables engineers to design intricate mould geometries with precise tolerances, ensuring optimal material flow, cooling, and ejection. CNC machining and EDM (Electrical Discharge Machining) techniques are then employed to manufacture the mould components to micron-level accuracy, enabling the production of high-quality plastic parts with minimal defects.
2. Technological Advancements
Kilang plastic injection moulding facilities leverage state-of-the-art technologies to enhance efficiency, quality, and productivity throughout the manufacturing process. High-speed, high-precision injection moulding machines equipped with advanced control systems and robotic automation ensure consistent material distribution, cycle time optimization, and part quality verification.
Furthermore, real-time monitoring sensors and predictive analytics algorithms enable proactive maintenance and quality control, minimizing downtime and defects. The integration of Industry 4.0 principles, such as IoT connectivity and data-driven decision-making, empowers kilang plastic injection moulding facilities to adapt and thrive in an increasingly competitive market landscape.
3. Diverse Applications Across Industries
The applications of kilang plastic injection moulding span across diverse industries, ranging from automotive and electronics to medical devices and consumer goods. In the automotive sector, kilang plastic injection moulding facilities produce a wide range of components, including interior trims, exterior panels, and functional parts, where lightweighting, durability, and aesthetic appeal are paramount.
Similarly, in the electronics industry, kilang plastic injection moulding facilities manufacture housings, enclosures, and connectors for electronic devices, ensuring precise fit, electromagnetic compatibility, and thermal management. Moreover, in the medical field, kilang plastic injection moulding plays a critical role in producing surgical instruments, medical implants, and diagnostic devices, where biocompatibility, sterilizability, and regulatory compliance are essential.
4. Future Prospects and Sustainability Initiatives
Looking ahead, the future of kilang plastic injection moulding holds promise for continued innovation and sustainability initiatives. Emerging trends such as additive manufacturing, bio-based polymers, and closed-loop supply chains are reshaping the landscape of plastic manufacturing, offering new opportunities for efficiency, customization, and environmental responsibility.
Additive manufacturing techniques like 3D printing enable rapid prototyping, on-demand production, and design optimization, reducing lead times and material waste. Furthermore, the development of bio-based polymers derived from renewable sources offers alternatives to conventional plastics, reducing reliance on fossil fuels and mitigating environmental impact.
By embracing these innovations and collaborating with stakeholders across the value chain, kilang plastic injection moulding facilities can drive positive change and pave the way towards a more sustainable and resilient future for the manufacturing industry.
Conclusion: Navigating the Path to Excellence
In conclusion, kilang plastic injection moulding stands as a testament to human ingenuity and technological prowess, driving advancements in precision manufacturing and sustainable development. Through precision engineering, technological advancements, diverse applications, and sustainability initiatives, kilang plastic injection moulding facilities are shaping the future of manufacturing, one plastic part at a time.
As we navigate the complexities of the modern industrial landscape, let us embrace the transformative potential of kilang plastic injection moulding to drive innovation, efficiency, and sustainability. By leveraging precision engineering, technological advancements, and collaborative partnerships, we can unlock new opportunities for growth, prosperity, and societal well-being in the years to come.
GETTING A QUOTE WITH LK-MOULD IS FREE AND SIMPLE.
FIND MORE OF OUR SERVICES:
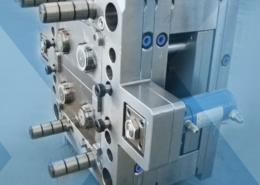
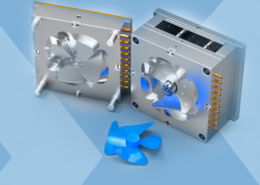
Plastic Molding
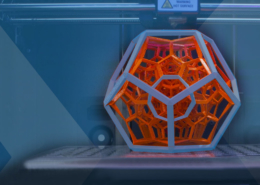
Rapid Prototyping
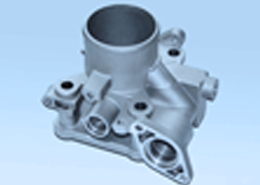
Pressure Die Casting
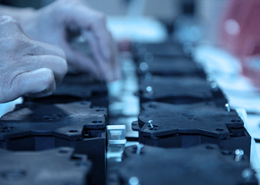
Parts Assembly
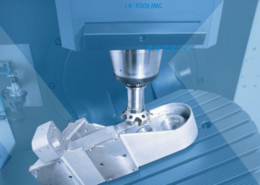