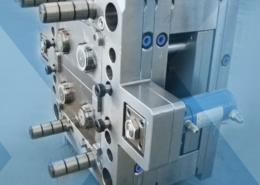
Unraveling the Marvels of Large Injection Moulding
Author:gly Date: 2024-06-08
Introduction: Igniting Curiosity
Large injection moulding stands as a pinnacle of modern manufacturing, captivating the imagination with its ability to craft intricate, oversized components with precision and efficiency. As we delve into the realm of large injection moulding, we embark on a journey through its evolution, applications, technological intricacies, and future prospects. This article aims to unravel the mysteries surrounding this transformative process, shedding light on its significance in today's industrial landscape.
1. Evolution of Large Injection Moulding
The evolution of large injection moulding traces back to the origins of conventional injection moulding in the early 20th century. Initially confined to the production of small to medium-sized parts, the advent of high-tonnage machines and advanced materials paved the way for scaling up the process to accommodate larger components. Over the decades, continuous innovations in machinery, materials, and process optimization have propelled large injection moulding into prominence, revolutionizing manufacturing across diverse industries.
Large injection moulding represents a convergence of precision engineering, materials science, and automation, enabling the production of oversized parts with unparalleled accuracy and consistency. From automotive body panels to industrial machinery components, the scope of applications for large injection moulding continues to expand, driving advancements in product design and performance.
2. Technological Marvels
At the heart of large injection moulding lies a synergy of cutting-edge technologies, each playing a crucial role in shaping the process's efficacy and versatility. High-tonnage injection moulding machines equipped with sophisticated control systems and robotic automation ensure precise material distribution and uniformity across large mould cavities. Advanced mold design and simulation software enable engineers to optimize part geometry, cooling channels, and gating systems, enhancing production efficiency and quality.
Furthermore, the integration of real-time monitoring sensors and predictive analytics algorithms enables proactive maintenance and quality control, minimizing downtime and defects. These technological marvels not only enhance the performance of large injection moulding but also pave the way for continuous improvement and innovation in the field.
3. Diverse Applications
The applications of large injection moulding span across a multitude of industries, ranging from automotive and aerospace to consumer goods and medical devices. In the automotive sector, large injection moulding is instrumental in the production of vehicle body panels, structural components, and interior trims, offering lightweight solutions without compromising on durability and aesthetics.
Similarly, in aerospace applications, large injection moulding facilitates the fabrication of aircraft fuselages, wing components, and interior fittings, where precision engineering and material performance are paramount. Moreover, the consumer goods industry benefits from large injection moulding for manufacturing oversized products such as furniture, appliances, and recreational equipment, catering to diverse consumer preferences and market demands.
4. Future Perspectives
Looking ahead, the future of large injection moulding holds immense promise, driven by ongoing research and development in materials, processes, and sustainability initiatives. Emerging trends such as additive manufacturing, advanced composite materials, and digital twin technologies are poised to revolutionize the landscape of large injection moulding, offering new avenues for design optimization, customization, and waste reduction.
Furthermore, the adoption of circular economy principles and eco-friendly practices will be integral to ensuring the long-term viability and environmental sustainability of large injection moulding processes. By embracing innovation and collaboration, stakeholders can unlock the full potential of large injection moulding, ushering in a new era of manufacturing excellence and sustainability.
Conclusion: Charting a Course for Innovation
In conclusion, large injection moulding stands as a beacon of innovation and progress in the realm of manufacturing, offering boundless opportunities for creativity, efficiency, and sustainability. Through its evolution, technological advancements, diverse applications, and future prospects, large injection moulding continues to redefine the boundaries of what is possible, inspiring generations of engineers, designers, and manufacturers to push the limits of imagination and ingenuity. As we navigate the complexities of today's industrial landscape, let us embrace the transformative potential of large injection moulding, charting a course towards a future defined by innovation, collaboration, and sustainability.
GETTING A QUOTE WITH LK-MOULD IS FREE AND SIMPLE.
FIND MORE OF OUR SERVICES:
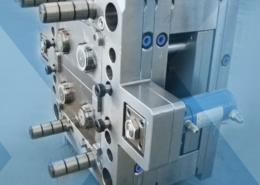
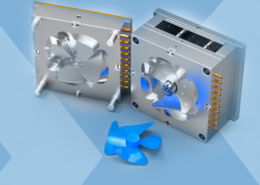
Plastic Molding
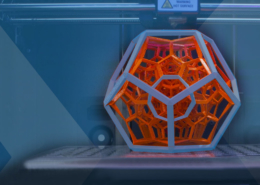
Rapid Prototyping
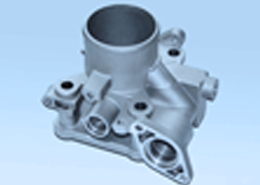
Pressure Die Casting
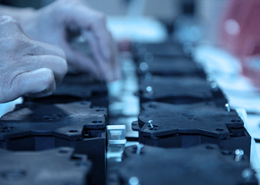
Parts Assembly
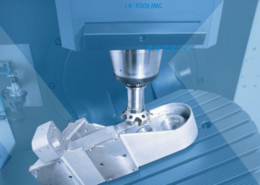