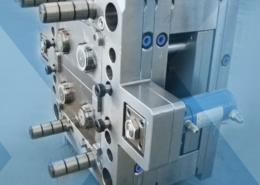
Exploring Large Injection Molding: Revolutionizing Manufacturing
Author:gly Date: 2024-06-08
Injection molding, a cornerstone of modern manufacturing, has undergone significant evolution with the advent of large injection molding techniques. This advanced process enables the creation of intricate, large-scale plastic components with remarkable efficiency and precision. In this article, we delve into the realm of large injection molding, exploring its intricacies, applications, and implications for the industry.
1. Evolution of Injection Molding
Injection molding has a rich history dating back to the late 19th century. Initially employed for producing simple items like buttons and combs, it has since evolved into a sophisticated process capable of crafting complex components for various industries. The development of large injection molding has been a natural progression, driven by the demand for oversized plastic parts in automotive, aerospace, and consumer goods sectors.
Large injection molding represents a paradigm shift in manufacturing, pushing the boundaries of what was once deemed feasible. With advancements in technology and machinery, manufacturers can now produce massive components with intricate details and structural integrity previously unattainable.
The evolution of large injection molding has not only expanded the scope of manufacturing possibilities but has also led to improvements in product design, material utilization, and cost efficiency.
2. Technological Innovations
The emergence of large injection molding owes much to technological innovations in machinery, materials, and process control. High-tonnage injection molding machines equipped with advanced robotics and automation systems enable the production of large parts with unparalleled precision and consistency.
Moreover, developments in material science have broadened the range of polymers suitable for large injection molding, offering enhanced properties such as durability, heat resistance, and lightweight construction. This versatility allows manufacturers to meet the diverse requirements of modern applications, from automotive body panels to industrial enclosures.
Furthermore, advancements in process monitoring and optimization have significantly enhanced the efficiency and reliability of large injection molding operations. Real-time data analytics, predictive maintenance, and quality control measures ensure consistent part quality while minimizing downtime and waste.
3. Applications Across Industries
Large injection molding finds extensive applications across a myriad of industries, revolutionizing the production of critical components and assemblies. In the automotive sector, it enables the fabrication of lightweight yet robust body panels, interior trims, and structural components, contributing to fuel efficiency and vehicle performance.
In aerospace and defense, large injection molding is utilized for manufacturing aircraft fuselages, interior components, and engine housings, where precision engineering and stringent quality standards are paramount.
Moreover, the consumer goods industry benefits from large injection molding for producing oversized products such as furniture, appliances, and recreational equipment, where aesthetics, functionality, and durability are key considerations.
4. Environmental Considerations
While large injection molding offers numerous advantages in terms of efficiency and production capabilities, it also raises environmental concerns related to material consumption, energy usage, and waste management. The scale of production inherent in large injection molding can result in substantial material waste if not properly optimized.
However, advancements in sustainable materials, recycling technologies, and energy-efficient processes are mitigating these concerns, paving the way for a more environmentally friendly approach to large injection molding. By adopting circular economy principles and embracing eco-friendly practices, manufacturers can minimize their environmental footprint while maximizing resource utilization and operational efficiency.
Conclusion: Shaping the Future of Manufacturing
In conclusion, large injection molding represents a transformative force in the manufacturing landscape, enabling the production of oversized plastic components with unprecedented precision and efficiency. Through technological innovations, diverse applications, and environmental considerations, this advanced process is reshaping industries and driving innovation across the globe.
As we look towards the future, continued research and development in large injection molding technology hold the promise of further advancements in efficiency, sustainability, and cost-effectiveness. By embracing these opportunities and addressing the associated challenges, we can unlock new possibilities and propel the manufacturing industry towards a more sustainable and prosperous future.
GETTING A QUOTE WITH LK-MOULD IS FREE AND SIMPLE.
FIND MORE OF OUR SERVICES:
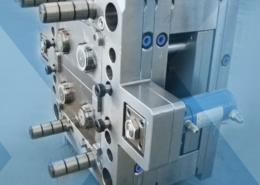
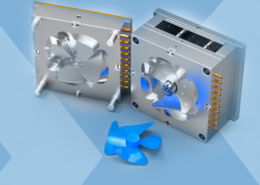
Plastic Molding
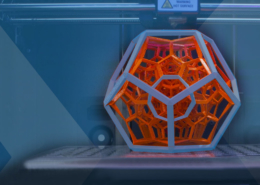
Rapid Prototyping
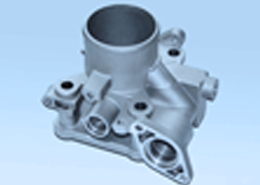
Pressure Die Casting
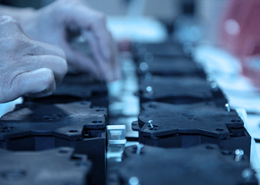
Parts Assembly
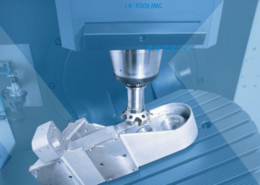