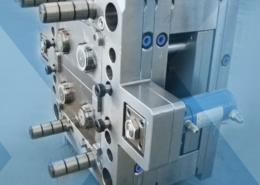
Medical Injection Molding: Innovating Healthcare Solutions
Author:gly Date: 2024-06-08
Introduction
Medical injection molding stands at the forefront of healthcare innovation, revolutionizing the production of intricate medical devices and components. In an era where precision, reliability, and patient safety are paramount, this manufacturing technique plays a pivotal role in advancing medical technology. This article provides an in-depth exploration of medical injection molding, offering insights into its applications, benefits, and future prospects.
Medical injection molding involves the manufacturing of medical devices and components through the injection of specialized materials into precise molds. This process enables the production of intricate and customized parts essential for various medical applications, including diagnostics, treatment, and patient care.
Material Selection
The choice of materials in medical injection molding is critical to ensuring the safety, efficacy, and regulatory compliance of the final products. Medical-grade polymers such as polyethylene, polypropylene, and thermoplastic elastomers are commonly used due to their biocompatibility, sterilizability, and chemical resistance.
Biocompatibility
Biocompatible materials are essential in medical injection molding to minimize the risk of adverse reactions when the devices come into contact with the human body. Extensive testing and certification processes ensure that materials meet stringent biocompatibility standards, including ISO 10993, to guarantee patient safety.
Sterilization Compatibility
Medical devices must undergo sterilization to eliminate pathogens and ensure their safety for clinical use. Materials used in medical injection molding must withstand various sterilization methods such as steam autoclaving, ethylene oxide (EtO) sterilization, and gamma irradiation without compromising their mechanical properties or integrity.
Design and Engineering
The design and engineering phase of medical injection molding is crucial for developing devices that meet the stringent requirements of the healthcare industry. Advanced CAD software and simulation tools facilitate the design of complex geometries, ensuring optimal functionality, manufacturability, and regulatory compliance.
Complex Geometries
Medical devices often feature intricate designs and fine details to perform specific functions effectively. Medical injection molding allows for the production of complex geometries with high precision and repeatability, enabling the creation of innovative devices such as microfluidic components, catheters, and surgical instruments.
Tooling and Mold Design
The design and fabrication of molds play a significant role in the success of medical injection molding processes. High-precision tooling and mold design ensure the accurate replication of intricate features, tight tolerances, and minimal part defects, ultimately contributing to the quality and performance of medical devices.
Regulatory Compliance
Compliance with regulatory standards and requirements is paramount in the medical device industry to ensure patient safety and product quality. Medical injection molding manufacturers must adhere to stringent regulations set forth by regulatory bodies such as the U.S. Food and Drug Administration (FDA) and the European Medicines Agency (EMA).
FDA Approval Process
The FDA approval process for medical devices involves rigorous testing, documentation, and regulatory submissions to demonstrate safety and efficacy. Medical injection molding manufacturers must navigate the complex regulatory landscape, including premarket notifications (510(k)), premarket approval (PMA), and quality system regulations (QSR), to bring their products to market.
Quality Management Systems
Implementing robust quality management systems (QMS) is essential for ensuring compliance with regulatory requirements and maintaining product quality throughout the manufacturing process. Medical injection molding facilities adhere to standards such as ISO 13485, which outline requirements for quality management systems specific to the medical device industry.
Applications
Medical injection molding finds extensive applications across various healthcare sectors, contributing to advancements in diagnostics, treatment, and patient care. From disposable syringes to implantable devices, medical injection molding plays a crucial role in improving healthcare outcomes and enhancing patient experiences.
Diagnostic Devices
Diagnostic devices such as blood glucose meters, test strips, and diagnostic cartridges rely on precise and reliable components produced through medical injection molding. These devices enable rapid and accurate diagnosis of medical conditions, empowering healthcare professionals to make informed treatment decisions.
Implantable Devices
Implantable medical devices, including pacemakers, orthopedic implants, and drug delivery systems, benefit from the customization and biocompatibility offered by medical injection molding. These devices improve patients' quality of life by restoring function, alleviating symptoms, and delivering targeted therapies with minimal invasiveness.
Future Directions
The future of medical injection molding holds exciting possibilities for innovation and advancement in healthcare technology. Emerging trends such as additive manufacturing, biodegradable materials, and personalized medicine are poised to reshape the landscape of medical device manufacturing and patient care.
Additive Manufacturing
Additive manufacturing techniques such as 3D printing offer new opportunities for rapid prototyping, customization, and on-demand manufacturing of medical devices. Incorporating additive manufacturing into medical injection molding processes enables the production of patient-specific implants, personalized prosthetics, and anatomical models for surgical planning.
Biodegradable Materials
The development of biodegradable materials for medical injection molding presents a sustainable solution for reducing environmental impact and improving patient outcomes. Biodegradable polymers such as polylactic acid (PLA) and polyglycolic acid (PGA) offer biocompatibility and mechanical properties comparable to traditional materials, making them ideal for disposable medical devices and implants.
Conclusion
Medical injection molding plays a pivotal role in driving innovation and advancement in healthcare technology, enabling the production of precise, reliable, and customized medical devices and components. From material selection to design engineering and regulatory compliance, every aspect of the manufacturing process is meticulously executed to ensure patient safety and product quality. As technology continues to evolve and new materials and processes emerge, the future of medical injection molding holds immense potential for improving healthcare outcomes and enhancing patient care.
In conclusion, medical injection molding is not only a manufacturing technique but also a catalyst for transformative change in the healthcare industry. By leveraging the latest advancements in materials science, design engineering, and regulatory compliance, medical injection molding continues to push the boundaries of innovation, driving towards a future where healthcare is more accessible, efficient, and personalized.
GETTING A QUOTE WITH LK-MOULD IS FREE AND SIMPLE.
FIND MORE OF OUR SERVICES:
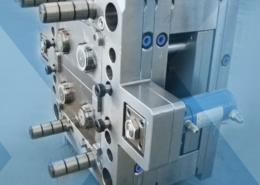
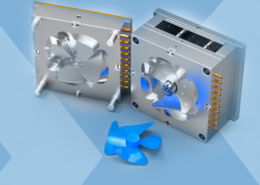
Plastic Molding
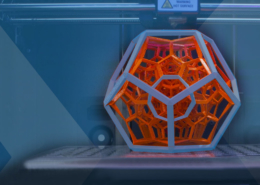
Rapid Prototyping
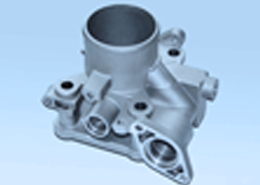
Pressure Die Casting
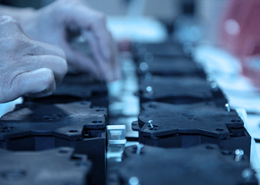
Parts Assembly
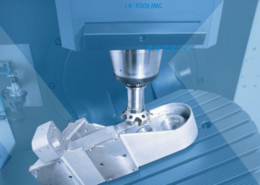