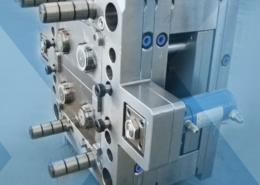
Exploring the Innovations of Medical Injection Moulding
Author:gly Date: 2024-06-08
Introduction
Medical injection moulding, a pivotal technology in modern healthcare, plays a vital role in the production of medical devices and components. Its significance lies in its ability to manufacture intricate and precise parts essential for various medical applications. This article delves into the realm of medical injection moulding, exploring its intricacies, applications, advancements, and future prospects.
Understanding Medical Injection Moulding
Medical injection moulding involves the process of injecting molten material into a mould cavity, where it solidifies to form the desired component. This technique offers high precision, repeatability, and cost-effectiveness, making it indispensable in medical device manufacturing.
Process Overview
The process begins with the selection of suitable materials, typically polymers such as thermoplastics or elastomers. These materials undergo melting and are injected into a mould under high pressure. Once the material cools and solidifies, the mould opens, releasing the finished product.
Key Components
Critical to the success of medical injection moulding are the moulds themselves, which must be meticulously designed and fabricated to meet stringent medical standards. Additionally, precision injection moulding machines equipped with advanced controls ensure consistent and accurate production.
Quality Assurance
Quality control is paramount in medical device manufacturing. Medical injection moulding processes undergo rigorous validation and verification procedures to ensure compliance with regulatory requirements, such as ISO 13485 and FDA guidelines.
Applications in Healthcare
Medical injection moulding finds widespread applications across various medical fields, contributing to advancements in patient care, diagnostics, and treatment.
Implantable Devices
The production of implantable medical devices, such as pacemaker components and orthopedic implants, relies heavily on the precision and biocompatibility offered by injection moulding techniques.
Drug Delivery Systems
Injection moulding facilitates the manufacturing of intricate drug delivery systems, including syringes, insulin pens, and inhalers, ensuring precise dosing and administration for patients.
Diagnostic Equipment
Components for diagnostic equipment, such as test cartridges and imaging device parts, benefit from the high precision and consistency achieved through injection moulding processes.
Advancements and Future Directions
Continual innovation drives the evolution of medical injection moulding, paving the way for enhanced performance, efficiency, and customization in medical device manufacturing.
Material Innovations
Ongoing research focuses on the development of advanced materials with enhanced properties, such as biocompatibility, antimicrobial resistance, and radiopacity, expanding the possibilities for medical applications.
Automation and Robotics
The integration of automation and robotics streamlines production processes, improving efficiency, reducing waste, and enabling the fabrication of increasingly complex medical components with higher precision.
3D Printing Integration
The convergence of 3D printing technologies with injection moulding offers new avenues for rapid prototyping, customization, and on-demand production of medical devices tailored to individual patient needs.
Conclusion
In conclusion, medical injection moulding stands as a cornerstone of modern healthcare, driving innovation and enabling the production of critical medical devices and components. Through a thorough understanding of its processes, applications, and ongoing advancements, stakeholders in the medical industry can harness the full potential of this technology to improve patient outcomes and advance the field of medicine. Continued research and collaboration will further propel the evolution of medical injection moulding, opening new possibilities for future medical innovations and patient care.
GETTING A QUOTE WITH LK-MOULD IS FREE AND SIMPLE.
FIND MORE OF OUR SERVICES:
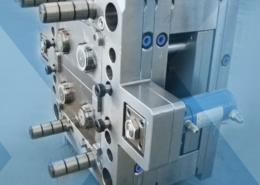
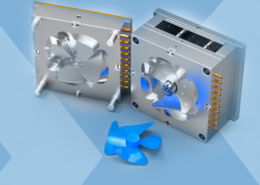
Plastic Molding
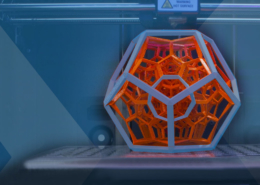
Rapid Prototyping
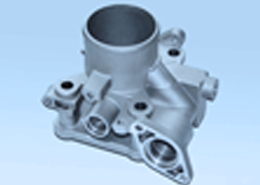
Pressure Die Casting
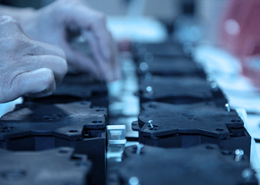
Parts Assembly
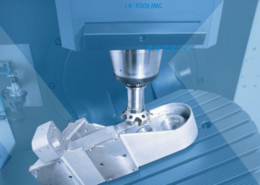