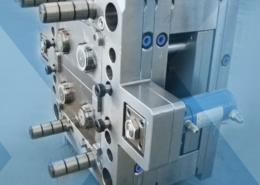
Advancements in Medical Plastic Molding: Revolutionizing Healthcare
Author:gly Date: 2024-06-08
Introduction
Medical plastic molding stands at the forefront of healthcare innovation, encompassing the manufacturing processes vital for producing a wide array of medical devices and components. From intricate surgical tools to essential diagnostic equipment, the realm of medical plastic molding shapes the landscape of modern medicine. This article delves into the intricacies of this technology, exploring its significance, advancements, and impact on healthcare.
Materials Innovation
The foundation of medical plastic molding lies in materials innovation, where polymers are meticulously selected to meet the stringent requirements of medical applications. Polyethylene, polycarbonate, and polypropylene are among the versatile materials tailored for specific medical uses. These materials exhibit exceptional properties such as biocompatibility, sterilizability, and durability, ensuring the safety and efficacy of medical devices.
The advent of bioresorbable polymers represents a revolutionary leap in medical plastic molding. These biodegradable materials gradually degrade within the body, eliminating the need for surgical removal and reducing patient discomfort. The utilization of bioresorbable polymers in implants, sutures, and drug delivery systems heralds a new era in patient care and recovery.
Precision Engineering
Precision engineering lies at the core of medical plastic molding, enabling the fabrication of intricate components with unparalleled accuracy. Advanced molding techniques, including injection molding and extrusion, facilitate the production of complex geometries essential for medical devices. Micro molding, in particular, allows for the creation of miniature components with micron-level precision, revolutionizing minimally invasive procedures.
Computer-aided design (CAD) and computer-aided manufacturing (CAM) further enhance precision and efficiency in medical plastic molding. These digital technologies enable designers to optimize part designs and simulate molding processes, minimizing errors and maximizing yield. The integration of additive manufacturing techniques such as 3D printing offers new avenues for rapid prototyping and customization in medical device development.
Sterilization Compatibility
Sterilization compatibility is paramount in medical plastic molding to ensure the safety and efficacy of devices used in clinical settings. Various sterilization methods, including steam autoclaving, ethylene oxide (EtO) gas sterilization, and gamma irradiation, impose unique challenges on plastic materials. Consequently, materials selection and processing parameters must be meticulously tailored to withstand these sterilization techniques while preserving device integrity.
The emergence of radiation-resistant polymers and antimicrobial additives addresses the evolving needs of sterilization in medical plastic molding. These innovations enhance material durability and mitigate the risk of microbial contamination, reinforcing the reliability of medical devices in critical healthcare environments.
Regulatory Compliance
Regulatory compliance is paramount in the realm of medical plastic molding, ensuring that devices meet stringent safety and performance standards mandated by regulatory authorities such as the FDA and CE. Manufacturers adhere to rigorous quality management systems, encompassing design controls, risk management, and validation processes, to ensure the consistency and reliability of medical devices.
The implementation of quality by design (QbD) principles facilitates proactive risk mitigation and product optimization throughout the product lifecycle. By integrating quality considerations into the design and manufacturing processes, manufacturers enhance product robustness and expedite regulatory approval, expediting market entry and improving patient access to innovative medical technologies.
Conclusion
In conclusion, medical plastic molding epitomizes innovation in healthcare, driving advancements in materials science, engineering precision, sterilization compatibility, and regulatory compliance. The convergence of these factors culminates in the development of safe, reliable, and cost-effective medical devices that transform patient care and clinical outcomes. Looking ahead, continued research and collaboration are essential to further elevate the capabilities of medical plastic molding, paving the way for future breakthroughs in healthcare delivery and patient well-being.
GETTING A QUOTE WITH LK-MOULD IS FREE AND SIMPLE.
FIND MORE OF OUR SERVICES:
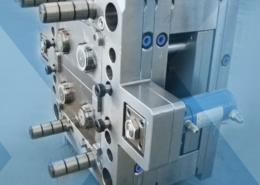
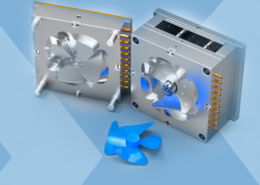
Plastic Molding
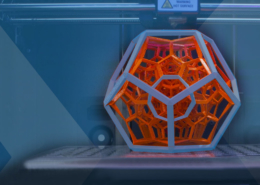
Rapid Prototyping
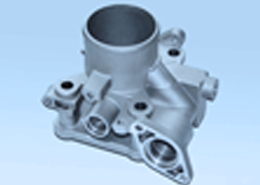
Pressure Die Casting
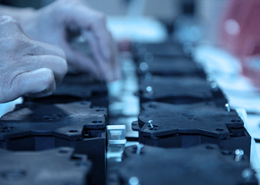
Parts Assembly
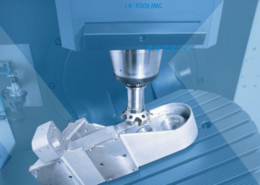