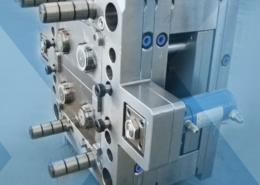
Exploring the World of Melting and Molding Plastic
Author:gly Date: 2024-06-08
In the realm of manufacturing, melting and molding plastic processes have become integral to the production of a wide array of products. From everyday items to complex industrial components, plastic molding techniques have transformed the way we design and fabricate objects. In this comprehensive exploration, we delve into the intricacies of melting and molding plastic, uncovering its mechanisms, applications, advantages, and future prospects.
Unraveling the Mechanisms of Plastic Melting and MoldingPlastic melting and molding involve a series of intricate processes aimed at transforming raw plastic materials into finished products. The journey begins with the selection of suitable polymers, which are then subjected to heat to reach their melting point. Once molten, the plastic is injected, extruded, or compression molded into a mold cavity, where it takes on the desired shape and form. Finally, the molded plastic is cooled and solidified, ready for use in various applications.
These processes offer unparalleled flexibility in design and production, enabling the creation of complex geometries and intricate details with ease. Moreover, advancements in technology have led to the development of innovative molding techniques, such as 3D printing, which further expand the possibilities of plastic fabrication.
Diverse Applications of Plastic Melting and MoldingPlastic melting and molding techniques find widespread applications across industries, ranging from automotive and aerospace to healthcare and consumer goods. In the automotive sector, plastic molding is used to manufacture interior and exterior components, such as dashboards, bumpers, and trim panels, offering lightweight and cost-effective solutions without compromising on quality or performance.
Similarly, in the medical field, plastic molding plays a crucial role in the production of medical devices, implants, and packaging materials. The ability to create custom-designed parts with biocompatible materials has revolutionized healthcare delivery, facilitating advancements in diagnosis, treatment, and patient care.
Advantages and Challenges of Plastic Melting and MoldingThe advantages of plastic melting and molding are manifold. Firstly, these processes offer high efficiency and cost-effectiveness, allowing for mass production of identical parts with minimal material wastage. Additionally, plastic molding enables the incorporation of intricate features and functional elements, enhancing the performance and aesthetics of the final product.
However, challenges such as environmental sustainability and material recyclability remain significant concerns in the plastic molding industry. Addressing these challenges requires innovative solutions, such as the development of biodegradable polymers and closed-loop recycling systems, to minimize the environmental impact of plastic production and consumption.
Future Perspectives and InnovationsLooking ahead, the future of plastic melting and molding holds immense potential for innovation and advancement. Researchers are exploring new materials and processing techniques to enhance the performance, sustainability, and recyclability of molded plastics. Additionally, advancements in digital design and additive manufacturing technologies are expected to further revolutionize the plastic molding industry, enabling rapid prototyping and customization of products.
By embracing these innovations and adopting sustainable practices, the plastic molding industry can contribute to a more environmentally friendly and socially responsible future.
ConclusionIn conclusion, plastic melting and molding processes represent a cornerstone of modern manufacturing, offering unmatched versatility, efficiency, and scalability. From automotive components to medical devices, the applications of plastic molding are diverse and far-reaching, shaping the way we design and fabricate products. By understanding the mechanisms, applications, advantages, and challenges of plastic melting and molding, we can harness the full potential of this transformative technology to drive innovation and progress in the years to come.
GETTING A QUOTE WITH LK-MOULD IS FREE AND SIMPLE.
FIND MORE OF OUR SERVICES:
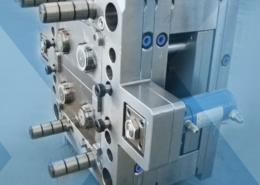
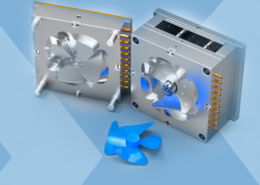
Plastic Molding
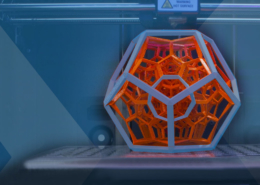
Rapid Prototyping
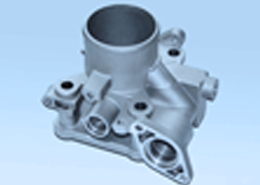
Pressure Die Casting
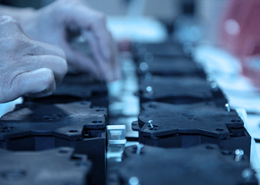
Parts Assembly
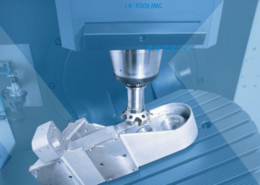