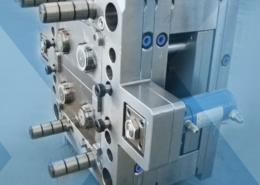
The Craft of Mold Plastic Injection: A Comprehensive Guide
Author:gly Date: 2024-06-01
In the intricate world of manufacturing, the process of mold plastic injection holds a pivotal position. It is the driving force behind the creation of an array of products, ranging from the smallest components of electronic devices to the largest parts of automobiles and construction equipment. This article aims to delve deeply into the workings of mold plastic injection, discussing its principles, applications, and the crucial steps involved in the process.
Understanding the Basics
Mold plastic injection, often referred to as injection molding, is a manufacturing technique that involves the injection of molten plastic into a mold cavity. The mold, which is typically made of metal, is designed to replicate the desired shape and dimensions of the final product. Once the molten plastic is injected, it solidifies within the mold, adopting its shape. The cooled and hardened plastic is then ejected from the mold, resulting in the finished part.
The heart of the injection molding process lies in the injection molding machine. These machines are highly specialized and come in various sizes, depending on the scale of production required. They typically consist of three main components: the injection unit, the clamping unit, and the mold. The injection unit is responsible for heating and injecting the plastic into the mold, while the clamping unit secures the mold in place during the injection and cooling process.
The Craft of Mold Design
Mold design is a crucial aspect of the injection molding process. It requires a blend of engineering expertise and creativity, as the mold must not only replicate the desired shape but also accommodate for shrinkage, warping, and other potential deformations that can occur during the cooling process. The design must also take into account the ease of mold opening and the ejection of the finished part.
Modern mold design often incorporates advanced technologies like CAD (Computer-Aided Design) and CAM (Computer-Aided Manufacturing) software, which allow for precise modeling and simulation of the injection molding process. This helps in identifying and rectifying potential issues early in the design stage, ensuring a smooth and efficient production run.
Selection of Plastics
The choice of plastic is crucial in determining the final properties of the injection-molded part. There are hundreds of different types of plastics available, each with its unique mechanical, chemical, and thermal properties. Selection must be made based on the requirements of the application, such as strength, durability, temperature resistance, and cost considerations.
Common plastics used in injection molding include thermoplastics like polypropylene (PP), polyethylene (PE), and acrylonitrile butadiene styrene (ABS). Thermosets, which cannot be reheated and remolded, are also sometimes used, particularly in applications that require high heat resistance.
The Injection Molding Process
The injection molding process can be broken down into several distinct steps:
1. Mold Preparation: The mold is assembled and prepared for injection. This involves ensuring that the mold is clean and free of any debris that could affect the quality of the final part.
2. Injection: The molten plastic is injected into the mold cavity under high pressure. The temperature and pressure are carefully controlled to ensure a uniform and complete filling of the mold.
3. Cooling and Solidification**: The injected plastic is allowed to cool and solidify within the mold. This step is crucial as it determines the final shape and dimensions of the part.
4. Ejection: Once the plastic has cooled and solidified, the mold is opened, and the finished part is ejected. This is typically done using ejector pins or similar mechanisms.
5. Post-Processing: The ejected part may require further processing, such as trimming, deburring, or surface treatment, to achieve the desired finish.
Quality Control and Defect Prevention
Quality control is essential in the injection molding process. Regular inspections of the mold, plastics, and production process help identify and correct any issues that could lead to defects in the finished parts. Common defects in injection molding include shrinkage, warping, air bubbles, and surface imperfections.
To prevent these defects, manufacturers often implement strict quality control measures, including the use of high-quality raw materials, regular mold maintenance, and the employment of advanced molding techniques like vacuum molding or gas-assisted molding.
Applications of Injection Molding
The versatility and efficiency of injection molding have made it a ubiquitous presence in various industries. From consumer electronics and automotive parts to medical devices and packaging, injection molding is the backbone of many manufacturing processes.
The automotive industry, for instance, heavily relies on injection molding for the production of components like dashboards, door panels, and interior trim pieces. The electronics industry uses injection molding to create cases, connectors, and other small parts for devices like smartphones and computers.
Conclusion
Mold plastic injection is a highly specialized and crucial aspect of modern manufacturing.
GETTING A QUOTE WITH LK-MOULD IS FREE AND SIMPLE.
FIND MORE OF OUR SERVICES:
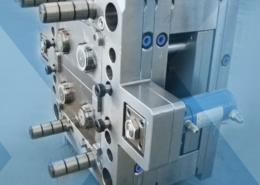
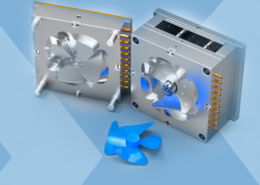
Plastic Molding
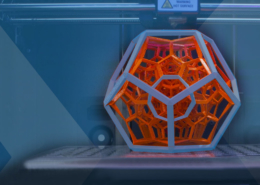
Rapid Prototyping
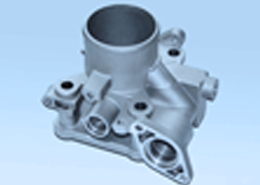
Pressure Die Casting
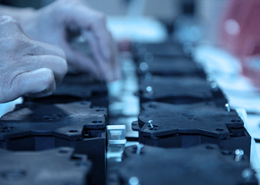
Parts Assembly
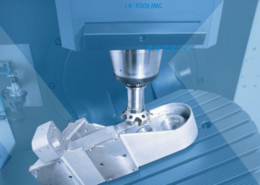