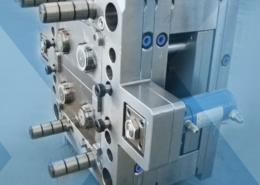
The Craft of Plastic Molding: An Insight into the Technique and Its Applications
Author:gly Date: 2024-06-01
Plastic molding, a vital process in the manufacturing industry, has revolutionized the way we produce and use plastic products. From household items to complex industrial components, plastic molding enables the creation of diverse and durable products that cater to a wide range of applications. This article delves into the intricacies of plastic molding, discussing its principles, techniques, and applications.
Principles of Plastic Molding
Plastic molding involves the shaping of plastic materials into desired forms by applying heat and pressure. The process begins with selecting the appropriate plastic resin, which is then heated to a semi-liquid state, allowing it to flow into a mold cavity. The mold, which is specifically designed to create the desired shape, is closed, and pressure is applied to ensure that the plastic fills the cavity evenly. As the plastic cools and solidifies, it takes the shape of the mold cavity, producing a product that closely matches the desired dimensions and features.
The success of the molding process depends on several key factors, including the selection of the appropriate plastic material, the design of the mold, the temperature and pressure settings, and the duration of the molding cycle. Each of these factors can significantly impact the quality, durability, and cost-effectiveness of the final product.
Types of Plastic Molding Techniques
1. Injection Molding: Injection molding is one of the most common plastic molding techniques. It involves injecting molten plastic into a mold cavity under high pressure. The mold is then cooled, and the solidified plastic is ejected, resulting in a finished product. Injection molding is suitable for producing large quantities of identical parts and components.
2. Compression Molding: Compression molding involves placing a heated plastic material into a closed mold cavity and applying pressure to compress and shape it. This technique is often used for thermosetting plastics that cannot be easily melted. Compression molding is suitable for creating products with intricate details and complex shapes.
3. Blow Molding: Blow molding is a process where a hollow plastic parison (a tube-like structure) is inflated with air while inside a mold cavity, causing it to expand and take the shape of the mold. This technique is commonly used to produce containers, bottles, and other hollow plastic products.
4. Rotational Molding: Rotational molding, also known as rotomolding, involves placing powdered plastic into a mold that rotates on two axes. The mold is then heated, causing the plastic to melt and coat the inside of the mold evenly. As the mold cools, the plastic solidifies, resulting in a hollow product with a smooth finish. Rotational molding is suitable for creating large, hollow plastic products such as tanks, watercraft, and signs.
Applications of Plastic Molding
Plastic molding finds applications across various industries, including automotive, electronics, medical, packaging, and construction. In the automotive industry, plastic molding is used to produce components such as dashboards, door panels, and bumpers. In the electronics industry, plastic molded parts are essential for housing electronic components and creating connectors and cables. The medical industry relies on plastic molding to produce medical devices, surgical instruments, and disposable healthcare products. Packaging industries use plastic molding to create containers, packaging materials, and labels. The construction industry benefits from plastic molding for creating pipes, ducts, and other structural components.
Challenges and Future Trends in Plastic Molding
Despite its widespread use and benefits, plastic molding faces several challenges, including environmental concerns, material limitations, and technological advancements. The disposal of plastic waste is a significant environmental issue, as plastics are not biodegradable and can accumulate in landfills or leak into water bodies, causing pollution.
To address these challenges, manufacturers are exploring sustainable alternatives such as biodegradable plastics and recycled plastic materials. These alternatives aim to reduce the environmental impact of plastic molding while maintaining product quality and performance.
Future trends in plastic molding include the integration of advanced technologies such as additive manufacturing (3D printing) and digital twin modeling. These technologies enable the creation of complex shapes and customized products, improving design flexibility and production efficiency. Additionally, the rise of Industry 4.0 and smart manufacturing systems is expected to revolutionize plastic molding, introducing automation, data analytics, and connectivity to enhance productivity, quality control, and sustainability.
In conclusion, plastic molding is a crucial process in the manufacturing industry, offering a range of benefits and applications. Its principles, techniques, and applications have evolved over time, responding to market demands and technological advancements. However, the industry faces challenges related to sustainability and waste management, necessitating innovative solutions and alternatives. By investing in research and development, adopting sustainable practices, and integrating advanced technologies, the plastic molding industry can continue to thrive and contribute to sustainable development.
GETTING A QUOTE WITH LK-MOULD IS FREE AND SIMPLE.
FIND MORE OF OUR SERVICES:
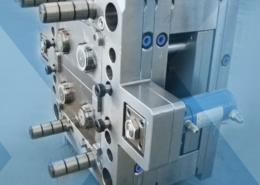
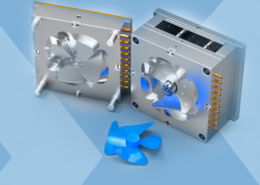
Plastic Molding
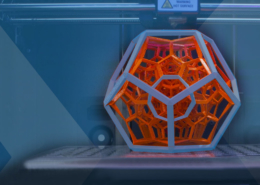
Rapid Prototyping
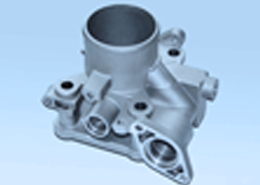
Pressure Die Casting
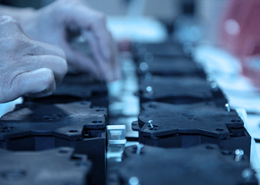
Parts Assembly
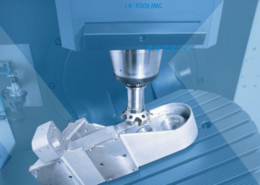